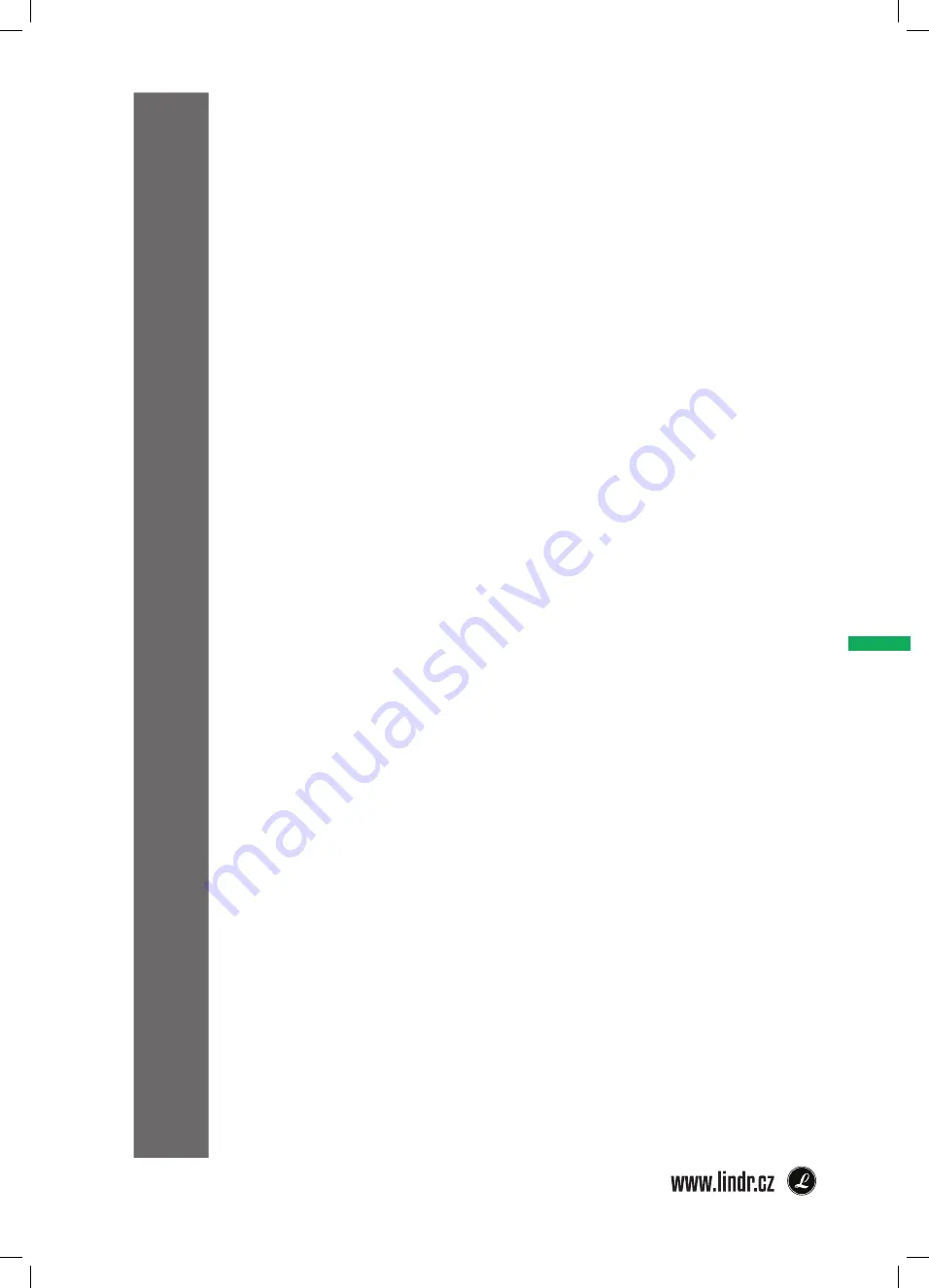
WA
TER COOLER
S
23
PR
ODUC
T
MODEL
COOLING
POWER
OF THE
COMPRESSOR
(HP)
COOLING
POWER
OF THE
COMPRESSOR
(W
)
M
AXIMUM COOLING
CAP
ACIT
Y (L/
HOUR)T
O 0°C/
TK 45°C
CONTINUOUS
COOLING
PERFORM
ANCE
(L/HOUR)
THERM
AL
GR
ADIENT Δt (°C
)
NUMBER OF
TAPS (PCS)
TY
PE OF
REFRIGER
ANT
VOL
TA
GE
POWER
(W
)
A
MPER
AGE
(A
)
DIMENSION OF THE C
ABINE
T
(WxD
xH mm)
NE
T
WEIGHT
(K
G)
CWP 100
GREEN LINE
1/3
860
90
70
10
0
R290
220-240V 50H
z~1
621
2,70
275x340x610
29,0
CWP 200
GREEN LINE
3/4
1550
140
120
10
0
R290
220-240V 50H
z~1
1035
4,50
330x420x680
37,5
CWP 300
GREEN LINE
1
2300
200
180
10
0
R290
220-240V 50H
z~1
1081
4,70
420x510x680
49,0
CWP 200 mobile
GREEN LINE
3/4
1550
140
120
10
2
R290
220-240V 50H
z~1
1081
4.50
335x400x1490
51,0
CWP 300 mobile
GREEN LINE
1
2300
200
180
10
2
R290
220-240V 50H
z~1
1081
4,70
420x530x1520
66,0
CWP 300/k pr
ofi mobile
GREEN LINE
1
2300
200
180
10
2
R290
220-240V 50H
z~1
1311
5,70
420x530x1520
71,0
AS
-40
GREEN LINE
1/8
310
45
25
10
0
R290
220-240V 50H
z~1
322
1,40
440x270x395
18,0
AS
-80
GREEN LINE
1/4
630
80
45
10
0
R290
220-240V 50H
z~1
506
2,20
530x330x475
26,0
AS
-110
GREEN LINE
1/3
860
110
60
10
0
R290
220-240V 50H
z~1
621
2,70
610x420x475
31,5
AS
-110
INO
X TR
OPIC
AL
GREEN LINE
1/3
860
110
60
10
0
R290
220-240V 50H
z~1
621
2,70
640x450x480
32,0
AS
-160
GREEN LINE
3/4
1550
160
110
10
0
R290
220-240V 50H
z~1
874
3,80
660x420x540
40,5
AS
-200
GREEN LINE
3/4
2000
200
150
10
0
R290
220-240V 50H
z~1
782
3,40
660x420x540
42,5
AS
-160
INO
X TR
OPIC
AL
GREEN LINE
3/4
1550
160
110
10
0
R290
220-240V 50H
z~1
874
3,80
730x530x700
44,5
AS
-45
2x T
ap
GREEN LINE
1/8
310
45
25
10
2
R290
220-240V 50H
z~1
322
1,40
440x270x430
21,0
AS
-110
INO
X TR
OPIC
AL
3x T
ap
GREEN LINE
1/3
860
110
60
10
3
R290
220-240V 50H
z~1
529
2,30
640x450x480
38
AS
-160
INO
X TR
OPIC
AL
4x T
ap
GREEN LINE
3/4
1550
160
110
10
4
R290
220-240V 50H
z~1
874
3,80
730x530x700
48,0
26. TECHNIC
AL D
AT
A: