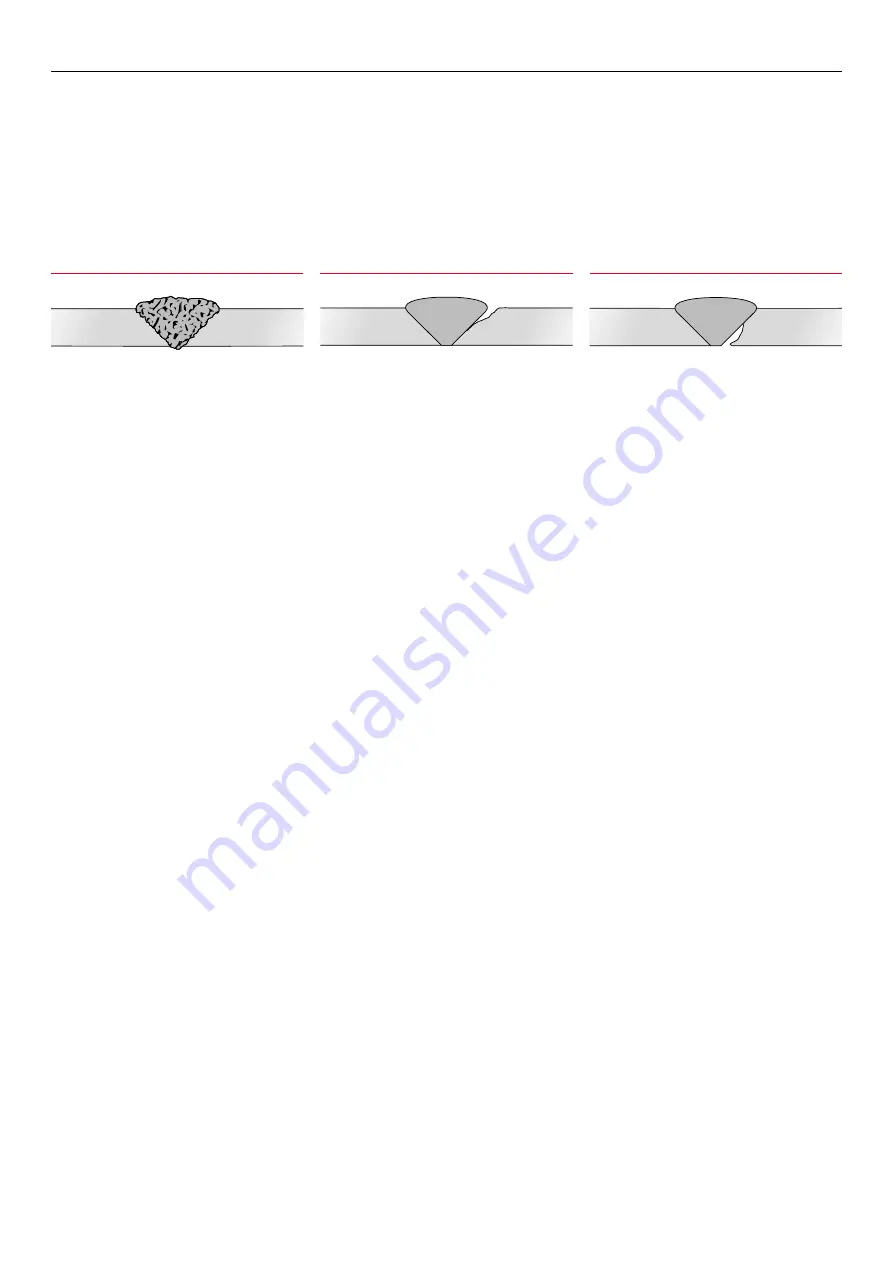
Correct selection of electrodes is important for vertical welding.
In overhead fillet welds, careful attention to technique is necessary to
obtain a sound weld of good profile. Medium current is required for
best results. High current will cause undercutting and bad shape of
the weld, while low current will cause slag inclusions. To produce a
weld having good penetration and of good profile, a short arc length is
necessary. Angle of electrode for overhead fillets is illustrated above.
3.7 Typical Defects Due to Faulty Technique
Shielded metal arc welding, like other welding processes, has welding
procedure problems that may develop which can cause defects in the
weld. Some defects are caused by problems with the materials. Other
welding problems may not be foreseeable and may require immediate
corrective action. A poor welding technique and improper choice of
welding parameters can cause weld defects. Defects that can occur
when using the shielded metal arc welding process are slag inclusions,
wagon tracks, porosity, wormhole porosity, undercutting, lack of
fusion, overlapping, burn through, arc strikes, craters, and excessive
weld spatter. Many of these welding technique problems weaken the
weld and can cause cracking. Other problems that can occur which can
reduce the quality of the weld are arc blow, finger nailing, and improper
electrode coating moisture contents.
Defects caused by welding technique
Slag Inclusions
Slag inclusions occur when slag particles are trapped inside the weld
metal which produces a weaker weld. These can be caused by:
→
erratic travel speed
→
too wide a weaving motion
→
slag left on the previous weld pass
→
too large an electrode being used
→
letting slag run ahead of the arc.
This defect can be prevented by:
→
a uniform travel speed
→
a tighter weaving motion
→
complete slag removal before welding
→
using a smaller electrode
→
keeping the slag behind the arc which is done by shortening the arc,
increasing the travel speed, or changing the electrode angle.
Undercutting
Undercutting is a groove melted in the base metal next to the toe or
root of a weld that is not filled by the weld metal. Undercutting causes a
weaker joint and it can cause cracking.
This defect is caused by:
→
excessive welding current
→
too long an arc length
→
excessive weaving speed
→
excessive travel speed.
On vertical and horizontal welds, it can also be caused by too large
an electrode size and incorrect electrode angles. This defect can be
prevented by:
→
choosing the proper welding current for the type and size of
electrode and the welding position
→
holding the arc as short as possible
→
pausing at each side of the weld bead when a weaving technique
is used
→
using a travel speed slow enough so that the weld metal can
completely fill all of the melted out areas of the base metal.
Undercutting
Lack of Fusion
Slag Inclusions
21
BOC Smootharc Advance II MIG 400R Operating manual