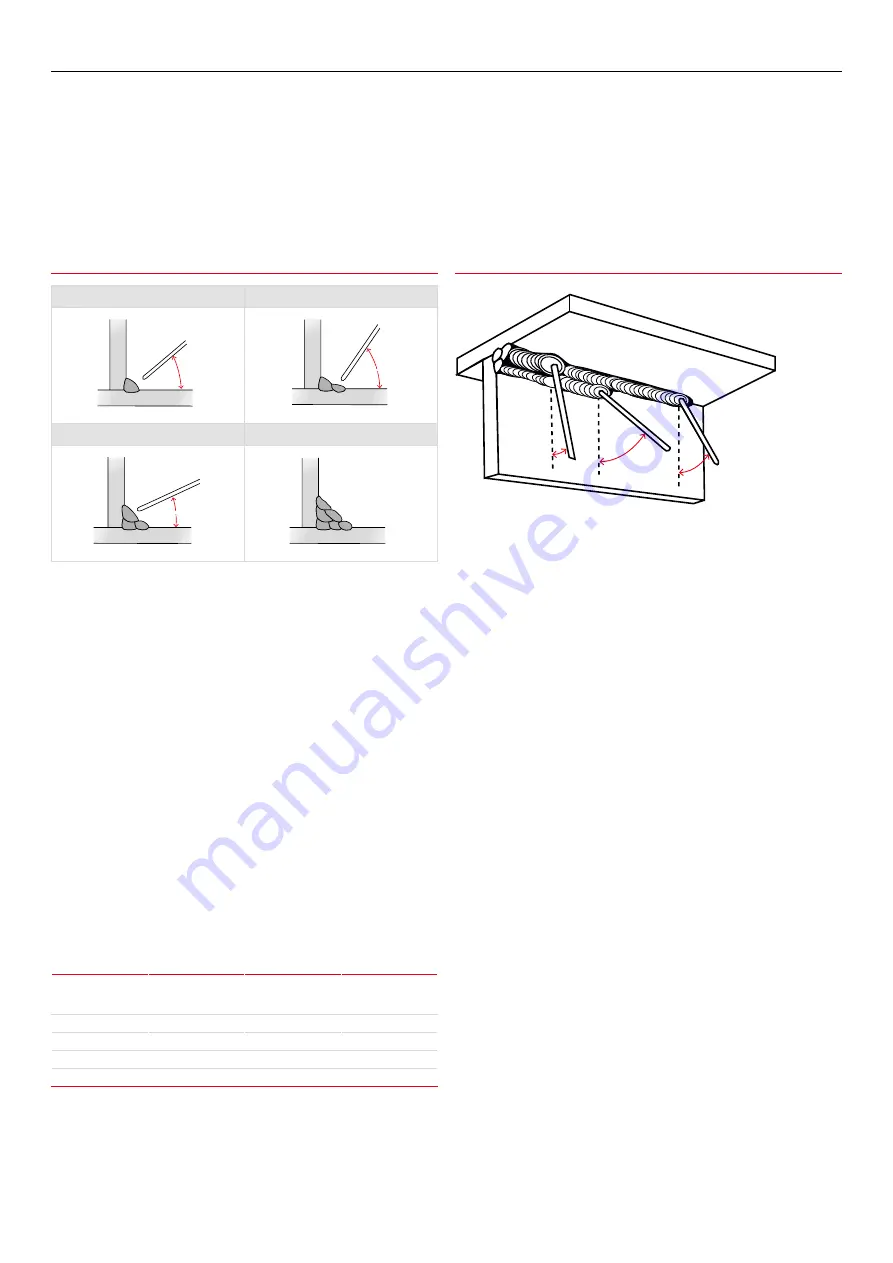
Concave Fillet Weld
A fillet in which the contour of the weld is below a straight line joining
the toes of the weld. It should be noted that a concave fillet weld of
a specified leg length has a throat thickness less than the effective
throat thickness for that size fillet. This means that when a concave
fillet weld is used, the throat thickness must not be less than the
effective measurement. This entails an increase in leg length beyond the
specified measurement.
The size of a fillet weld is affected by the electrode size, welding speed
or run length, welding current and electrode angle. Welding speed and
run length have an important effect on the size and shape of the fillet,
and on the tendency to undercut.
Insufficient speed causes the molten metal to pile up behind the arc
and eventually to collapse. Conversely, excessive speed will produce
a narrow irregular run having poor penetration, and where larger
electrodes and high currents are used, undercut is likely to occur.
Fillet Weld Data
Nominal Fillet
Size (mm)
Minimum Throat
Thickness (mm)
Plate Thickness
(mm)
Electrode Size
(mm)
5.0
3.5
5.0–6.3
3.2
6.3
4.5
6.3–12
4.0
8.0
5.5
8.0–12 & over
4.0
10.0
7.0
10 & over
4.0
Selection of welding current is important. If it is too high the weld
surface will be flattened, and undercut accompanied by excessive spatter
is likely to occur. Alternatively, a current which is too low will produce a
rounded narrow bead with poor penetration at the root. The first run in
the corner of a joint requires a suitably high current to achieve maximum
penetration at the root. A short arc length is recommended for fillet
welding. The maximum size fillet which should be attempted with one
pass of a large electrode is 8.0 mm. Efforts to obtain larger leg lengths
usually result in collapse of the metal at the vertical plate and serious
undercutting. For large leg lengths multiple run fillets are necessary.
These are built up as shown. The angle of the electrode for various runs
in a downhand fillet weld is shown on the next page.
Recommended Electrode Angles for Fillet Welds
Multi-run horizontal fillets have each run made using the same run
lengths (run length per electrode table). Each run is made in the same
direction, and care should be taken with the shape of each, so that it has
equal leg lengths and the contour of the completed fillet weld
is slightly convex with no hollows in the face.
Vertical fillet welds can be carried out using the upwards or downwards
technique. The characteristics of each are: upwards – current used is low,
penetration is good, surface is slightly convex and irregular. For multiple
run fillets large single pass weaving runs can be used. Downwards –
current used is medium, penetration is poor, each run is small, concave
and smooth (only BOC Smootharc 13 is suitable for this position).
The downwards method should be used for making welds on thin
material only. Electrodes larger than 4.0 mm are not recommended
for vertical down welding. All strength joints in vertical plates 10.0
mm thick or more should be welded using the upward technique. This
method is used because of its good penetration and weld metal quality.
The first run of a vertical up fillet weld should be a straight sealing run
made with 3.15 mm or 4.0 mm diameter electrode. Subsequent runs
for large fillets may be either numerous straight runs or several wide
weaving runs.
Recommended Angles for Overhead Fillet Welds
Recommended Electrode Angles for Fillet Welds
1st Run
2nd Run
Elect
rode
40°
55–60°
20–30°
1
2
3
4
5
6
Elect
rode
40°
55–60°
20–30°
1
2
3
4
5
6
3rd Run
Multi-run Fillet
Elect
rode
40°
55–60°
20–30°
1
2
3
4
5
6
Elect
rode
40°
55–60°
20–30°
1
2
3
4
5
6
30˚
45˚
15˚
20
BOC Smootharc Advance II MIG 400R Operating manual