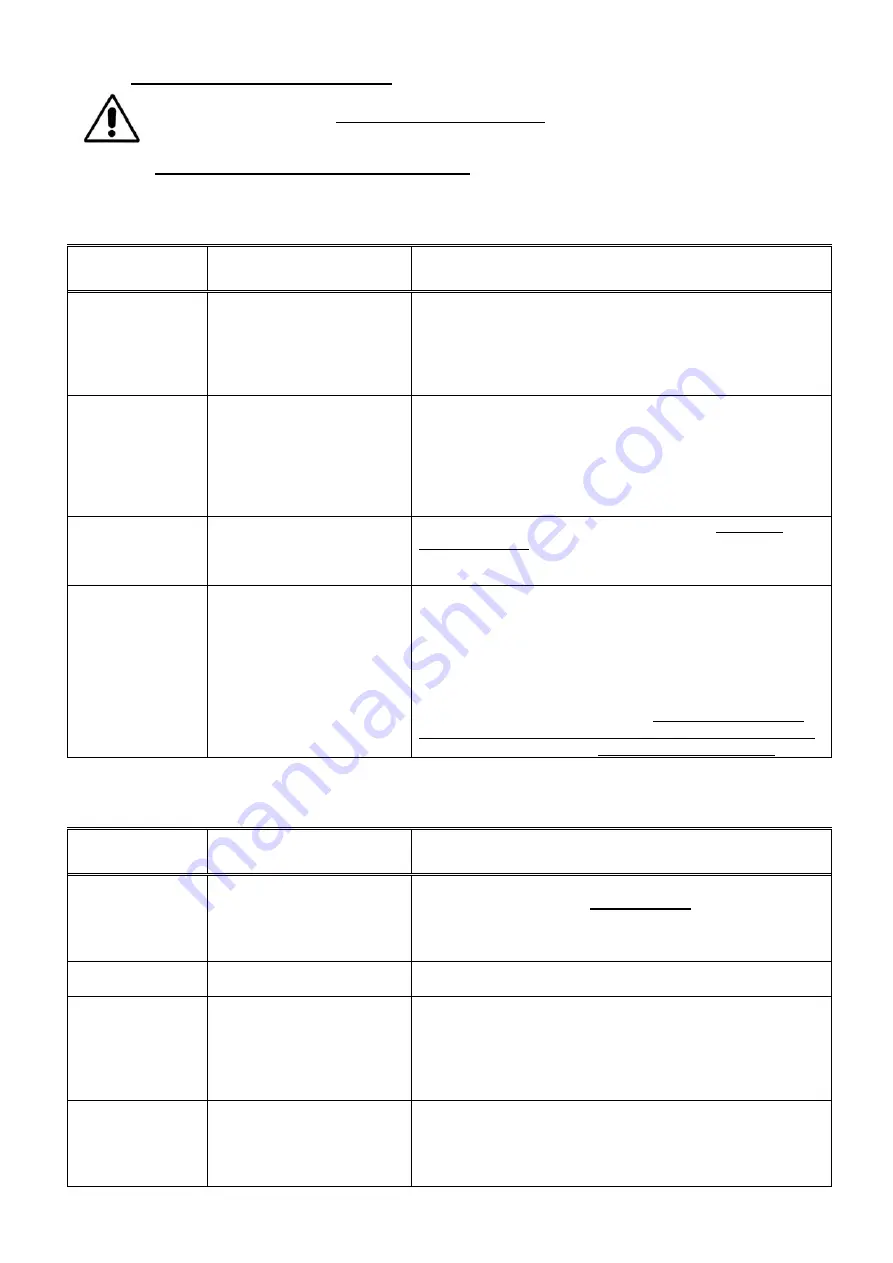
6.3.
ORDINARY MAINTENANCE
The personnel that perform the operations included in the present chapter, besides to present characteristics
showed in the chapter 4 and
must have read and understood
the safety prescriptions showed in the same
chapter 4.
For the selling of the worn and changed materials
, make reference to the prescriptions of the chapter 7.
6.3.1.
ORDINARY MAINTENANCE PERFORMABLE FROM THE OPERATOR
FREQUENCY
VERIFICATION /
CONTROL
MODALITIES AND CHECKS
Before of every
shift
Work area control:
¾
Must be cleaned and
without dust
The work place and the machine external parts must be cleaned;
besides other parts placed on the machine must be that could
prevent the correct functioning and that could compromise the
safety conditions presented at the beginning in the machine.
For any intervention or for the parts change, activate the
maintenance service.
At least once a
week
Verify the functionality:
¾
Of the safety devices of
the chapter 4
¾
Of the stop functions
Perform a visual inspection and a functional test of the safety
devices, of the foreseen interblocks and of the stop functions with
the aim to check their correct functioning and stopping of the
moving elements.
For any intervention or for the parts change, activate the
maintenance service.
At least once a
week
Integrity visual verification
¾
All instruction plates,
signal and warning
In case of their illegibility, or are requested to the Authorized
Assistance Centre or are however changed from the user with
others showing the same information, in accordance with what
showed in the chapter 4.
At least once a
month
Integrity visual verification
¾
Tools and bowl
The tools use determines their wear in the time.
Following the opening operations of the moving shelter, or lifting
the tip-up head, after its cleaning, check visually the absences of
splinterings or rulings in the tool.
In case of negative result of at least a control, proceed with their
change.
The possible change must happen with the manufacturer original
products or at least of quality, safety and equivalent characteristics.
For investigations contact the Authorized Assistance Centre.
6.3.2.
ORDINARY MAINTENANCE PERFORMABLE FROM THE OPERATOR
FREQUENCY
VERIFICATION /
CONTROL
MODALITIES AND CHECKS
At least monthly
Inside the covers – motor
openings
All covers internal parts and the machine openings where the
motors are installed must be
cleaned and dry
.
Provide with adequate and common means (as for example vacuum
cleaner and dry brush for the dust and absorbent clothes for
possible water parts), to maintain adequate spaces.
At least monthly
Efficacy verification:
¾
Mechanical connections
Perform, with the appropriate tools, a tightening control of clamps,
screws, dies, bolts and connections in general.
At least quarterly
Verify the functionality:
¾
Motors run contactors,
¾
All control circuit relays
Perform a visual inspection to check the relays contacts condition,
the contactors power contacts and the canalizations and internal and
external pipes of the covers.
If these ones included the unipolar and/or multi polar cables aren’t
in normal conditions, with the aim to guarantee a correct
functionality, proceed to their change.
At least quarterly
General verifications
¾
Electric equipment
Verify the whole electric equipment for requirements of service and
functioning continuity.
It must be checked that the electric equipment parts subjected to
wear, as for example: cables and canalizations, all control actuators
worked from the operators, etc…, are integral and functional.
0161 696 0052
www.linda-lewis.co.uk