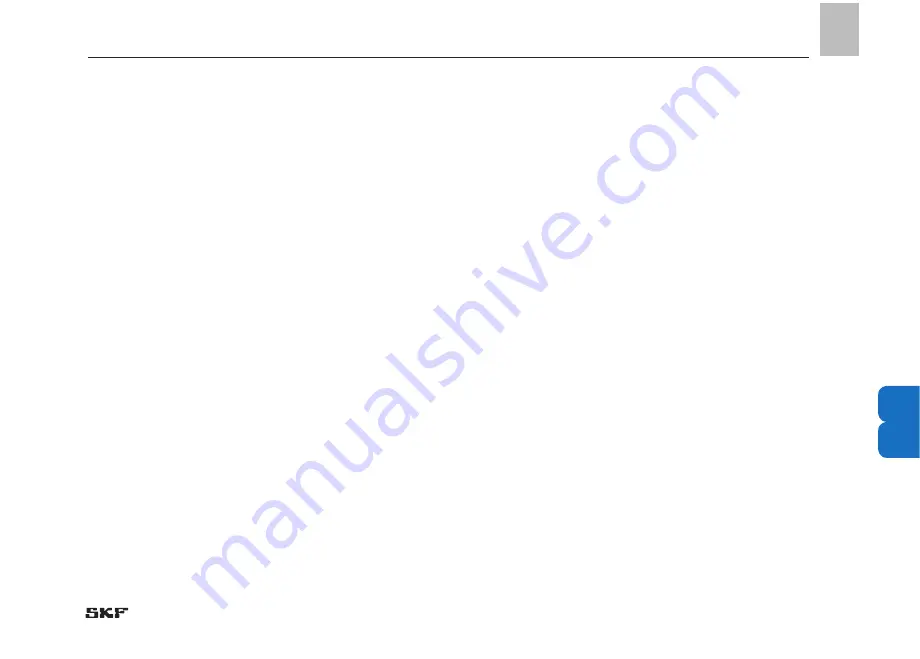
37
11
11. Spare parts
Battery spare parts kit
Part no.: 541-34901-2
consisting of:
○
Battery lid assy.
(incl. seal and screws)
Bracket spare parts kit
Part no.: 541-34901-3
consisting of:
○
Bracket
○
Fixing material (stainless steel)
2 x countersink screw M 6 x 20
DIN ISO 10642
2x washer
DIN 125 A6,4
2x hexagon nut M 6 A2
Closure plug spare parts kit
Part no.: 541-34901-4
consisting of:
○
Closure plug assy.
(incl. seal)
Battery holder spare part
Part no.: 541-34901-6
consisting of:
○
battery holder
Sealing ring spare parts kit
Part no.: 541-34901-5
consisting of:
○
self-adhesive sealing ring
EN
11. Spare parts
10
Summary of Contents for SKF TLMR 101
Page 38: ...38 Notices ...
Page 39: ...39 Notices ...