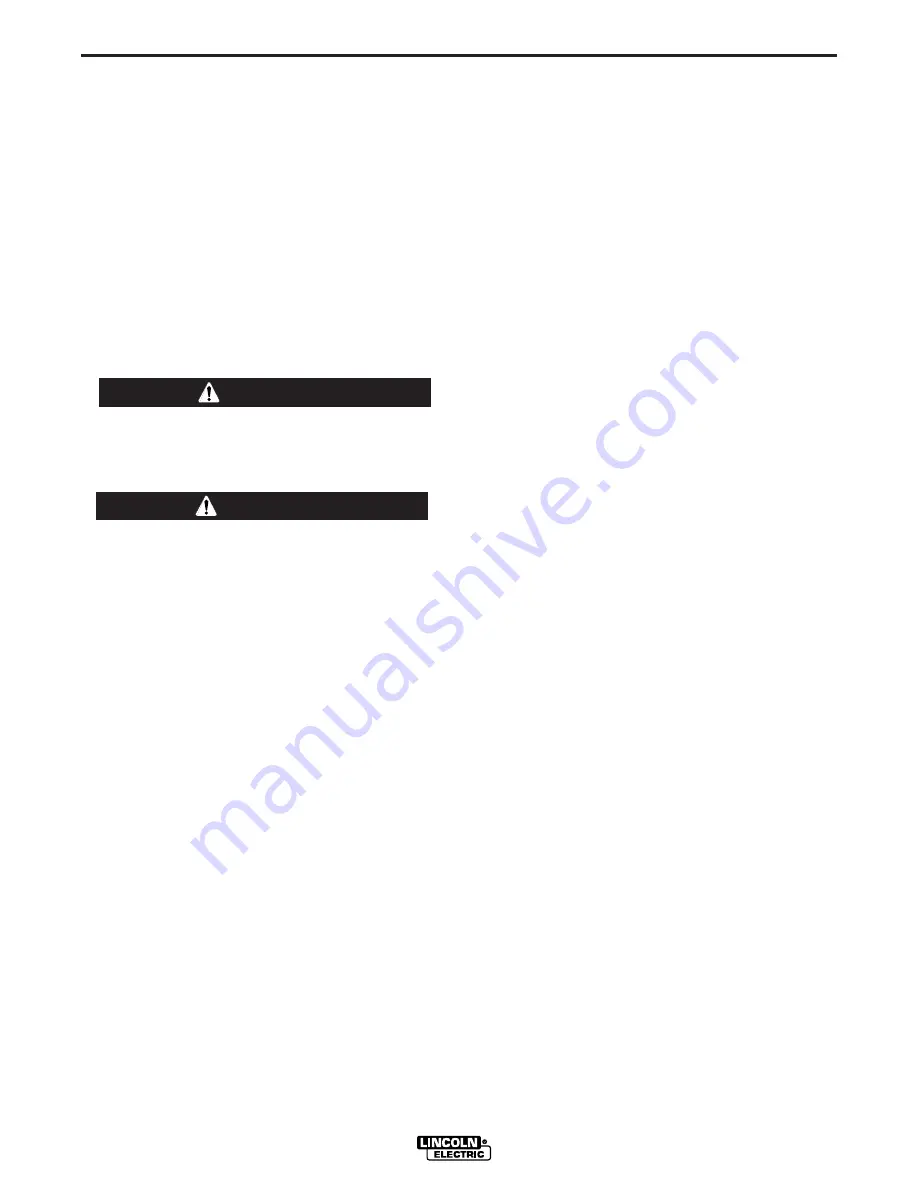
D-5
MAINTENANCE
D-5
RANGER® 250
WELDER / GENERATOR
MAINTENANCE
STORAGE:
Store the RANGER® 250 in clean, dry
protected areas.
CLEANING:
Blow out the generator and controls peri-
odically with low pressure air. Do this at least once a
week in particularly dirty areas.
BRUSH REMOVAL AND REPLACEMENT:
Itʼs nor-
mal for the brushes and slip rings to wear and darken
slightly. Inspect the brushes when a generator over-
haul is necessary.
• Do not attempt to polish slip rings while the
engine is running.
• Service and Repair should only be performed by
Lincoln Electric Factory Trained Personnel.
Unauthorized repairs performed on this equip-
ment may result in danger to the technician and
machine operator and will invalidate your factory
warranty. For your safety and to avoid Electrical
Shock, please observe all safety notes and pre-
cautions.
------------------------------------------------------------------------
WARNING
CAUTION
Summary of Contents for Ranger 250
Page 36: ...F 2 DIAGRAMS F 2 RANGER 250 ...
Page 37: ...F 3 DIAGRAMS F 3 RANGER 250 ...
Page 38: ...F 4 DIAGRAMS F 4 RANGER 250 ...
Page 39: ...F 5 DIAGRAMS F 5 RANGER 250 ...
Page 40: ...F 6 DIAGRAMS F 6 RANGER 250 ...
Page 42: ...F 8 DIAGRAMS F 8 RANGER 250 ...
Page 43: ...F 9 DIAGRAMS F 9 RANGER 250 ...
Page 44: ...F 10 DIAGRAMS F 10 RANGER 250 2 9 03 ...
Page 45: ...F 11 DIAGRAMS F 11 RANGER 250 ...