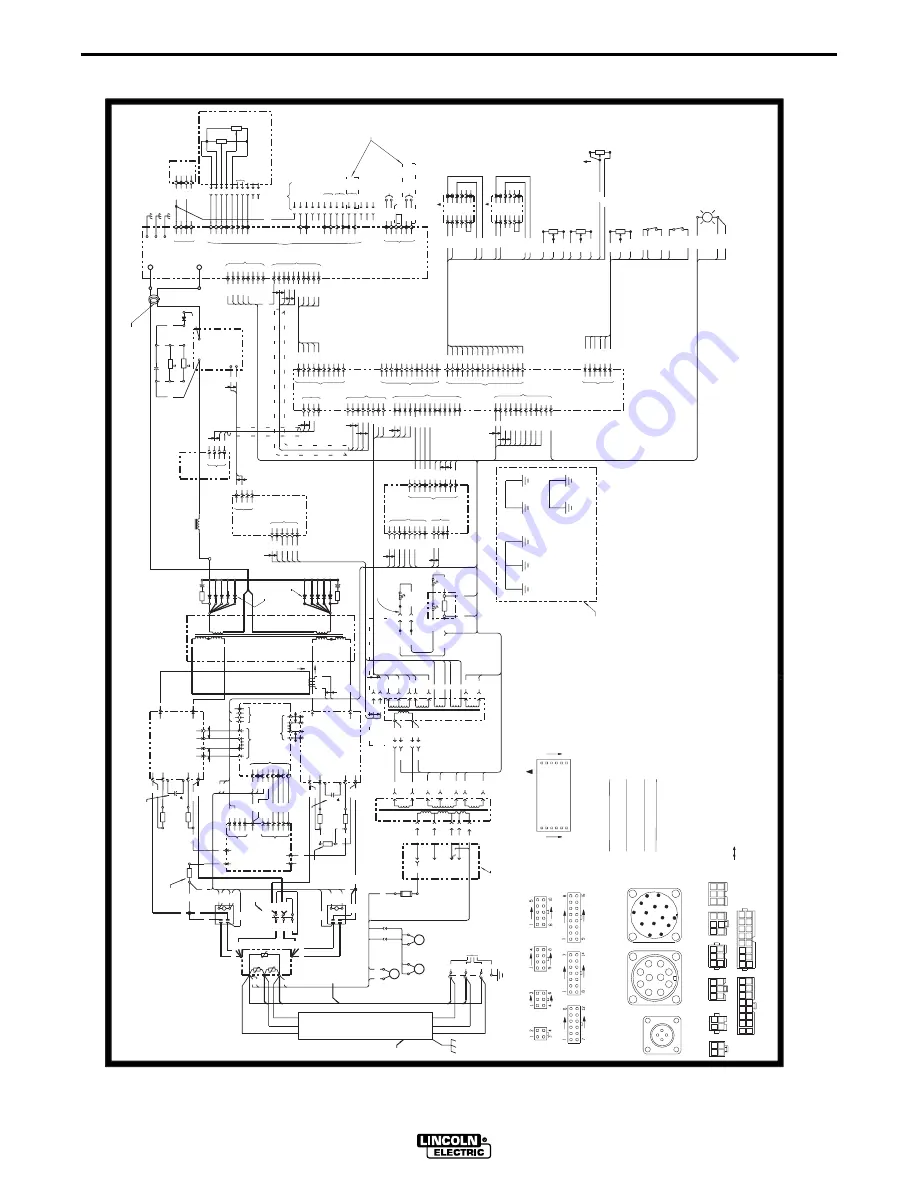
F-1
DIAGRAMS
F-1
INVERTEC STT II
R
32A
32B
15
16
J22
R
B
18V
32C
43A
R
U
3
18V
501
B
504
W
4
5
5
275
1
8
6
3
311
10
J6
1
212A
9
7
212
352
212B
503A
Y
301
305
245
223
8
11
3
1
3
503
24V
351
244
CASE
CASE
BACK
PLATFORM
4 AMP
S
BOTTOM
S
OUTSIDE
I
YY
4,5
12D
N
O
O
12
H3
H1
FAN
SLOW
12B
RIGHT
MOTOR
BLOW
H1
1
J11
6
5
379
2
J9
CR2
H3
3
4
2W
10K
CW (MAX)
353
362
363
CONTROL
BACKGROUND
2
12
6
7
4
10
3
N.L.
ASSEMBLY
INPUT
LINE
POWER
LINE
LOAD
D
C
B
A
F
S1
POWER
OFF
W
ON
U
A
INPUT
PER
R
N.A.
V
B
B
W
C
G
C
B
C
A
B
FILTER
A
52
TRIGGER
CORE
3
1
7
5
6
8
2
4
8
7
14
12C
12D
- ARC
+ ARC
CURRENT
METER
VAC
12D
A
378
11
363
J4
CW (MAX)
11
22
33
44
5
6
5
359
358
2W
10K
R11
3
5
377
5
6
6
TRANSFORMER
D1
O
374
N
I
O
T3
CURRENT
N
2
5
N.E.
4
371
1
3
4
3
10
J5
R
210
211A
502
246
212C
J3
6
B
Y
9
364
365
366
2
5
1
367
369
368
W
B
2
4
12
9
1
5
7
8
9
13
10
1
J28
10
11
8
9
7
5
8
10
5
3
1
4
2
4
6
6
J33
2
372
372
4
371
5
J1
6
7
J27
2
376
R
1
1
4
370
370
376
374
371
B
3
8
12
115V
374
10
1
32
2
33B
8
7
33A
J26
B
3
E
R
B
W
4
290A
1
10
367A
369
.045
502
(-)
INDICATOR
J25
115
223
357
356
5
355
6
354
6
2
1
CB2
J37
403
504
TRANSFORMER
AUXILIARY
T1
AUXILIARY
T4
N.D.
TRANSFORMER
13
1
501
220-
212A
150 5W
4
0V
H3
H2
H1
H1
9A
9A
9D
9A
PROTECTION
13
9C
R
W
S7
RECONNECT
1
12B
12B
212C
287
43A
R
18V
4
13
359
7
14
2
356
358
355
354
357
352
16
10
351
360
15
353
361
2
1
362
244
303
303
242
302
371A
302
374A
304
304
275
305
243
2
301
4
240
241
DARLINGTON
12
52
2
12D
2
4
W
1
D3
4
S
F
5
D4
1
BOARD
3
J16
TOP
D5
5
7
DRIVER
F
12B
MOTOR
FAN
LEFT
H1
MOTOR
TOP
H3
FAN
H1
H3
H1
D13
RECTIFIER
TP2
TP1
-
TP3
9D
J16, J28
J34
A
N.K.
413
416
405
408
406
VAC
1
VAC
7
3
4
3
2
1
F
8
52
314
315
J13
ELECTRODE SENSE LEAD
360
367
S2
VAC
368
367A
STAINLESS
R12
42
S3
.035
INTERFACE
503
TRIGGER
MILD
378
PEAK
377
PEAK
METER
BACKGROUND
CONTROL
HOT START
CW
WIRE TYPE
2W
500K
TAILOUT
CONTROL
R14
N.J.
REMOTE
1
5
407
2
6
6
3
115
350
J35
9
12
11
6
J17
J23
J24
METER PINOUT (VIEWED FROM BACK OF METER)
ELECTRICAL SYMBOLS PER E1537
W
18V
N
J2
2
J23
Y
380-
4
415V
H3
1
H2
H3
230V
200-
208V
N.M.
BACK
FOR SINGLE PHASE INPUT: CONNECT GREEN LEAD TO GROUND PER NATIONAL ELECTRIC CODE.
6V
10V
J24
18V
THERMOSTAT
COLOR CODE:
U
FAN
U
Y
WRAP RED LEAD WITH TAPE TO PROVIDE 600V. INSULATION.
J26
CONNECT BLACK & WHITE LEADS TO SUPPLY CIRCUIT.
B = BLACK
CASE
TRAY
G = GREEN
N = BROWN
FRONT
NOTES:
O = ORANGE
R = RED
W = WHITE
N.A.
J25
Y = YELLOW
U = BLUE
1. FOR MACHINES SUPPLIED WITH INPUT CABLE
N.M. PRESENT ON EUROPEAN VERSIONS, CODE 10383 AND HIGHER.
FOR SINGLE PHASE INPUT: GROUND MACHINE PER NATIONAL AND LOCAL ELECTRICAL CODES.
CONNECT TERMINALS U, V & W TO SUPPLY CIRCUIT.
CONNECT TERMINALS U & W TO SUPPLY CIRCUIT.
FOR THREE PHASE INPUT: GROUND MACHINE PER NATIONAL AND LOCAL ELECTRICAL CODES.
N.B. SINCE COMPONENTS OR CIRCUITRY OF A PRINTED CIRCUIT BOARD MAY CHANGE WITHOUT AFFECTING
COMPONENTS OR CIRCUITRY HAVING A COMMON CODE NUMBER.
THE INTERCHANGEABILITY OF A COMPLETE BOARD, THIS DIAGRAM MAY NOT SHOW THE EXACT
CONNECTION SHOWN IS FOR 440-460V OPERATION.
N.D. PLACE "A" LEAD ON APPROPRIATE CONNECTION FOR INPUT VOLTAGE.
N.E. D1 THRU D5 OUTPUT DIODES ARE A MATCHED SET.
D7 THRU D11 OUTPUT DIODES ARE A MATCHED SET.
9
N.F. R1, R9 BLEEDER RESISTORS ARE A MATCHED SET.
J21
1
N.G. C1, C2 CAPACITORS ARE A MATCHED SET.
P21
2
PINOUT OF FRONT PANEL CONNECTORS (REAR VIEW)
3
4
3
5
J29. J31
2
CONNECTION SHOWN IS FOR 380-460V OPERATION.
6
N.H. PLACE SWITCH IN APPROPRIATE POSITION FOR INPUT VOLTAGE.
1
6
N.I. DENOTES A TWISTED WIRE PAIR OR GROUP.
1
5
P29, P31
2
4
3
J30
4
3
5
2
6
1
P30
6
1
1
5
J22
9
FOR THREE PHASE INPUT: CONNECT GREEN LEAD TO GROUND PER NATIONAL ELECTRIC CODE.
2
2
4
3
2
N.K. NOT PRESENT ON EUROPEAN VERSIONS, CODE 10309 AND HIGHER.
4
1
10
5
3
11
4
6
12
N.L. PRESENT ON EUROPEAN VERSIONS, CODE 10309 AND HIGHER.
4
13
8
3
14
P22
15
8
16
7
6
5
16
4
15
3
14
2
13
1
12
11
10
7
J38
J19
N.J. NOT PRESENT ON EUROPEAN VERSION.
2. FOR MACHINES NOT SUPPLIED WITH INPUT CABLE
CONNECT BLACK, RED & WHITE LEADS TO SUPPLY CIRCUIT.
J39
1
2
3
4
310
309
310A
310
309A
309A
310A
2
6
J7
224A
10
2W
309
INSIDE
12B
25W
+
2200 F
C1
-
BOARD
25
450V
R4
(RIGHT)
3
4
1
5
307
2
3
6
308
J10
8
9D
4
52
52
2
B
2
9
J34
J36
C4
2W
R3
10
.001/400
N.E.
5
W
12C
12A
S
F
OUTSIDE
TOP
CHOKE
BOARD
3
12A
J12
J8
14
N.H.
BOARD
224
R
310
J15
316
9B
9B
12B
401, 403
1, 8
8
371
J22
51
12B
12B
TOP
12B
.001/400
CR1
25
2200 F
450V
9A
25W
-
+
53
9A
+
N.G.
9
R6
12A
R7
12A
12
R
W
R
W
401, 403
402, 404
(LEFT)
BOARD
SWITCH
1, 8
25W
25
4, 5
I
21
WIRE
81
82
GND
4
2
42
41
FEEDER
32
31
J39
N
B
H
L
M
42
414
B
H1
+
C
4
3
2
J
A
8
12
TRANSFORMER
C8
288
4
2 300W
289
R16
288A
SENSE
C2
L3
4
MAIN
1
3
289A
20/400
D11
T2
2
J18
4
F
S
4
313
3
3
2
J14
210A
210
THERMOSTAT
CHOKE
FAN
CASE
BOTTOM
1
1
S
INSIDE
F
BOTTOM
D9
BOTTOM
D10
1
14
311
53
3
4
33C
N
J30
33
1
2
6
6
224
H6
H4
A
440-
460V
A
5
9
J31
42V
H5
H4
115V
J21
R15
C
E
2 300W
G
J38
409
A
412
D
404
CURRENT
F
411
291
H
GND
B
MODULE
B
R
DRIVE
BOARD
14
317
9
9B
9B
402, 404
+
N.G.
N.F.
R5
25
25W
25W
7500
R9
9B
SWITCH
SHROUD
J6, J27, J33
J2, J36
J18, J37
J11, J12, J14
J1, J8,
P.C. BOARD CONNECTOR CAVITY NUMBERING SEQUENCE
212B
32C
33C
D12
J3, J9,
DARLINGTON
E
B
B
402
W
401
W
C
J
410
10K
PB
10K
OPTIONAL
D
CB1
C
76
75
6AMP
F
G
43B
42
9A
9D
9C
3
4
5
BOARD
POWER
8
309
7
308
307
W
14
THERMOSTAT
W
HEATSINK
J22
503A
DARLINGTON
503B
242
243
241
240
374A
371A
11
211A
9
350
5
R1
25W
7500
N.F.
D7
D8
R2
1
2
W
D2
C3
3
53
14
J5, J7,
(VIEWED FROM COMPONENT SIDE OF BOARD)
J15, J35
J10, J13,
J4, J17
E
1
I
3
4
77
K
Y
R13
(+)
10K
2
2W
CW (MAX)
3
361
CONTROL
366
503A
WIRE SIZE
THERMAL
OVERLOAD
364
365
7
6
8
5
16
13
15
14
4
12
11
CONTROL
CURRENT
BOARD
415
31A
33D
6AMP
4
6
246
245
212
2
INLINE CONNECTOR CAVITY NUMBERING SEQUENCE
313
G3136
WIRING DIAGRAM - INVERTEC STT II
(VIEWED FROM WIRE SIDE OF CONNECTOR)
1-9-98B
BG
SENSE
(-)
VOLTAGE
CONNECTION
(+)
2
1
J19
290
PROTECTION BOARD
REMOTE
288B
TOROIDAL
289B
374
3
51
H5
6
51
9B
N.L.
H
N
K
I
B
G
J
A
F
L
M
H
C
A
E
G
D
I
4
F
B
J
E
3
C
2
D
1
NOTE: This diagram is for reference only. It may not be accurate for all machines covered by this manual. The specific diag
ram for a particular code is pasted inside
the machine on one of the enclosure panels. If the diagram is illegible, write to the Service Department for a replacement. G
ive the equipment code number..