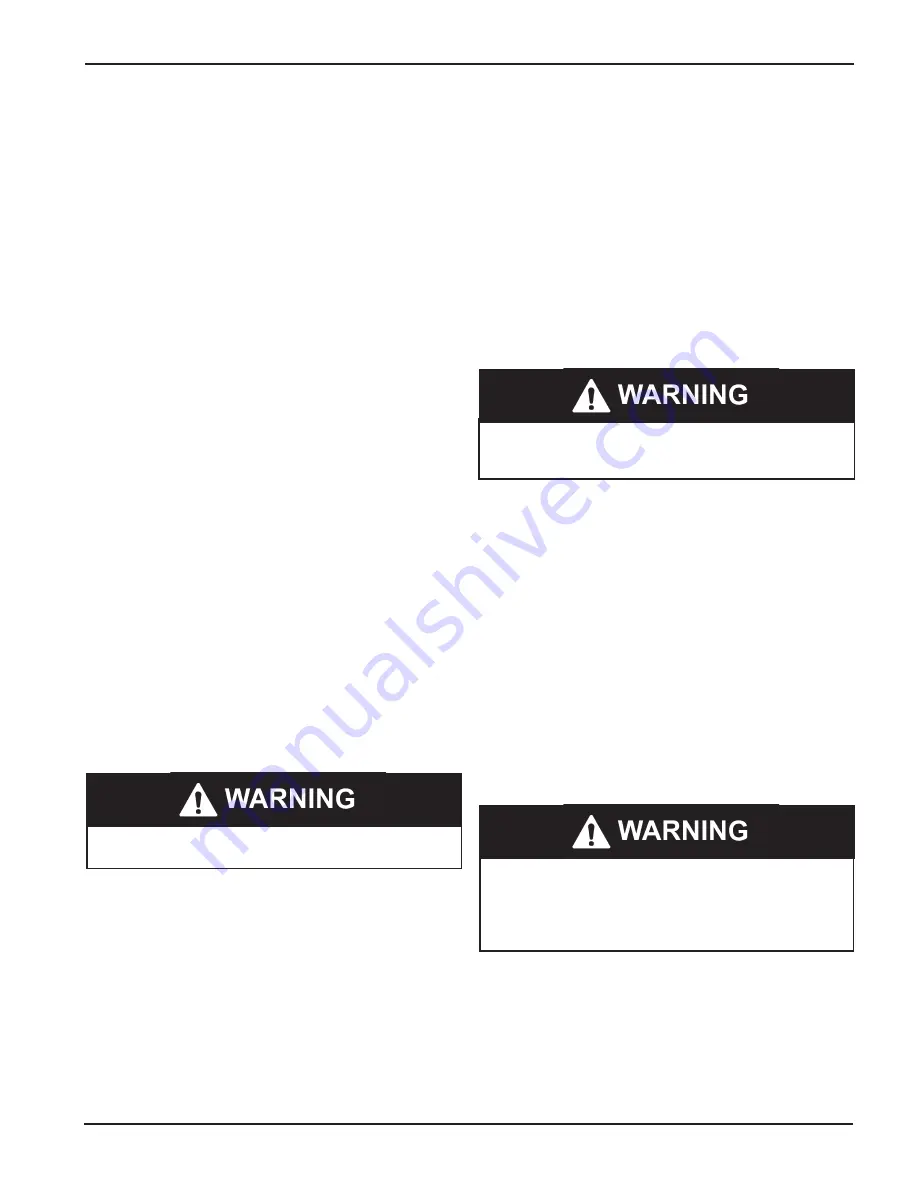
Page Number - 3
Form 403511
ACCESSORIES
Filter/Regulator/Lubricator and Gauge.
Eyebolt Kit.
Follower Plate - 120 lb., 400 lb.
Drum Cover - 120 lb., 400 lb.
Drum Cover with Tie Rods.
1709 Hoist.
PRESSURE RELIEF PROCEDURE
Always perform this procedure when the pump is shut off
and before checking, servicing, installing, cleaning or
repairing any part of this system.
Perform the following procedure:
A. Disconnect the air supply to the pump.
B. Point the dispensing valve away from yourself and
others.
C. Open the dispensing valve into an appropriate container
until the pressure is relieved.
If the above procedure does not relieve the pressure, the
dispensing valve or hose may be restricted. To relieve the
pressure, very slowly loosen the hose end coupling. Then
loosen completely and clear the dispensing valve and/or
hose.
OPERATION
INSPECTION BEFORE USING PUMP
Prior to operation or maintenance a visual inspection
shall be made. Check pump system for leaks, worn or
missing parts.
Any pump that appears to be damaged in any way, is
badly worn or operates abnormally shall be removed from
use until repairs are made. Contact a factory authorized
service center for repairs.
If overpressurizing of the equipment is believed to have
occurred, contact a factory authorized service center for
inspection of the pump.
Annual inspection by a factory authorized service center
is recommended.
To prevent personal injury, perform PRESSURE RELIEF
PROCEDURE before and after operating the pump.
To start pump, turn on the main air supply. Slowly open the
air regulator. Regulate air pressure from 20-40 psig and
throttle to prime pump. Open the dispensing valve to allow
air to be purged from the system. Allow pump to cycle until
grease without air pockets flows from dispensing valve,
then close dispensing valve.
After pump is primed, adjust air pressure to achieve a
smooth flow of grease from the dispensing valve. Do not
allow pump to operate when out of material. Pump will
accelerate quickly and run too fast, resulting in costly
damage to the pump.
If the pump accelerates quickly or is running too fast, stop it
immediately. Check the grease supply and refill it if
necessary. Prime the pump to remove all air from the
system, or flush the pump and relieve pressure.
In a circulating system, the pump runs continuously and
slows down or speeds up as supply demands, until the air
supply is shut off.
In a direct supply system, with adequate air pressure
supplied to the motor, the pump starts when the gun or
dispensing valve is opened and stalls against pressure
when it is closed.
Use the air regulator to control pump speed and grease
pressure. Always use the lowest pressure required to
achieve the desired results. Higher pressures will cause
pump packings to wear prematurely.
MAINTENANCE
To prevent personal injury, perform PRESSURE
RELIEF PROCEDURE before and after operating the
pump and before any maintenance.
LUBRICATION
An air line filter/regulator/lubricator is recommended for use
with your Lincoln pump to remove harmful dirt and moisture
from your compressor air supply, and to provide automatic air
motor lubrication.
If an air line lubricator is not used, the following procedure
should be performed daily:
A. Disconnect air coupler from air fitting.
B. Fill air coupler with NO. 10 SAE motor oil and reconnect to
air fitting.
C. Operate pump to distribute lubricant.
To reduce the risk of injury from splashing or static
sparking when flushing the pump with solvents, always
hold a metal part of the dispensing valve firmly to the
side of a grounded metal pail and operate pump at
lowest possible fluid pressure.
MATERIAL RESTRICTION PREVENTION
Flush the system as required with a compatible solvent to
prevent material buildup when pumping material that dries
or hardens.
CORROSION PREVENTION
To prevent water or air corrosion, never leave the pump
filled with water or air. Flush the pump first with a compat-
ible solvent and then again with mineral spirits or oil based
solvent.