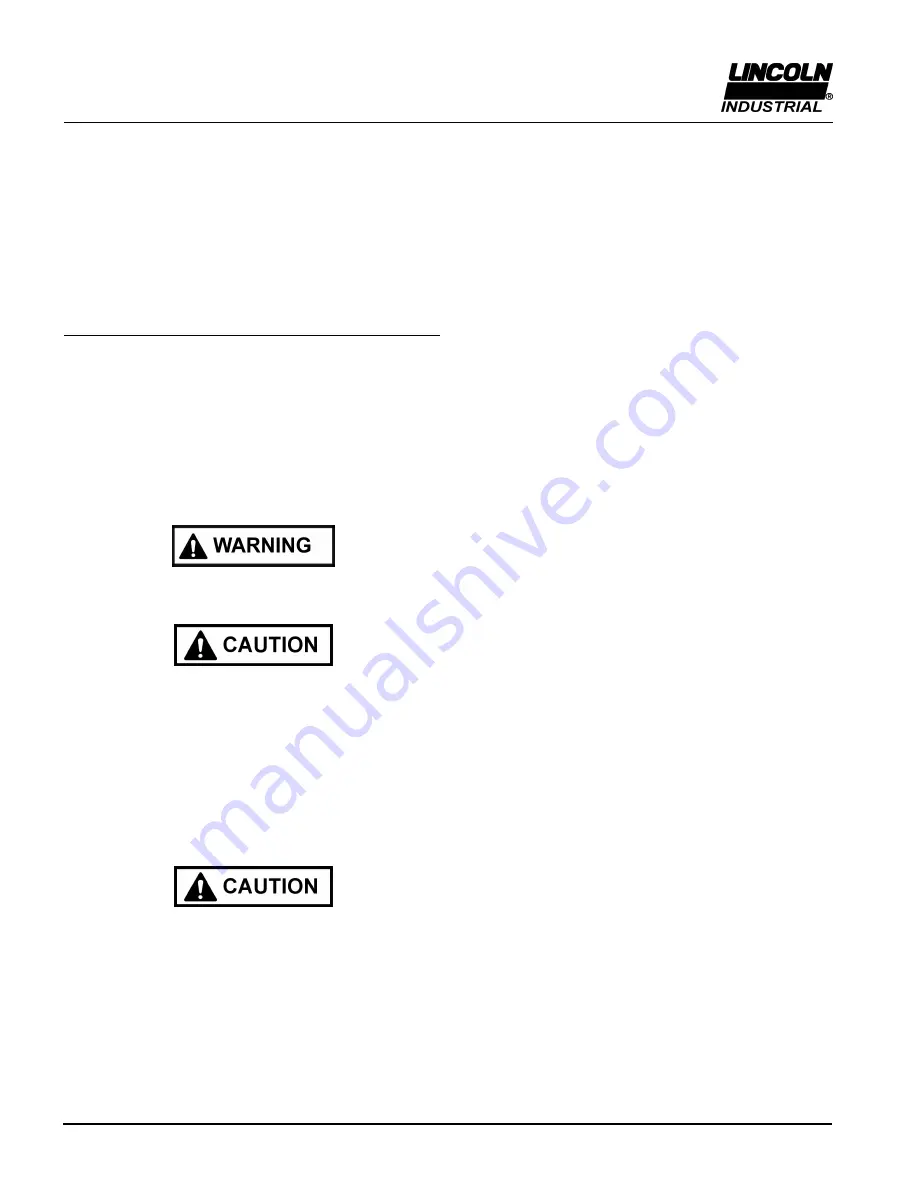
FlowMaster™ Rotary Driven Hydraulic Pump
Series “A”
Page Number - 2
7.5A-18100-A98
Form 402864
Description
85480 - Pump for 120 pound drum (16 gallon)
85481 - Pump for 60 pound drum
85482 - Pump for 400 pound drum (55 gallon)
85483 - Pump for 5 gallon pail
General Description
The Lincoln Industrial rotary Hydraulic Pump is a fully
hydraulically operated grease pump. Grease output is
proportional to the hydraulic input flow. The pump is
primarily designed for centralized lubrication systems such
as the Single Line Parallel, Single Line Progressive and
Two Line systems. An integrated pump control manifold is
incorporated with the motor to control input flow and
pressure. A 24 volt DC solenoid valve is also incorporated
as a method to turn the pump on and off.
The pump is driven by the rotary motion of the hydraulic
motor. Rotary motion is converted to reciprocating motion
through an eccentric crank mechanism. The reciprocating
action causes the pump cylinder to move up and down. The
pump is a positive displacement double acting pump as
grease output occurs during both the up and down stroke of
the pump.
During the down stroke, the pump cylinder is extended into
the grease. Through the combination of shovel action and
vacuum generated in the pump cylinder chamber, the
grease is forced into the pump cylinder. Simultaneously,
grease is discharged through the outlet of the pump. The
volume of grease during intake is twice the amount of
grease output during one cycle. During the upstroke, the
inlet check closes, and one half of the grease taken in
during the previous stroke is transferred through the outlet
check and discharged to the outlet port. Typical output of the
pump is shown on page 4.
Appropriate Use
All pump models are exclusively designed to pump and
dispense lubricants using hydraulic power.
The maximum specification ratings should not be
exceeded.
Any other use not in accordance with instructions will
result in loss of claims for warranty and liability.
service center nearest you for repair or adjustments other
than maintenance specified in this manual.
Annual inspection by the factory authorized warranty and
service center nearest you is recommended.
A list of factory authorized warranty and service centers is
available upon request.
Damaged Pumps
Any pump that appears to be damaged in any way, is badly
worn or operates abnormally, shall be removed from use
until repairs are made. Contact the factory authorized
warranty and service center nearest to you for repairs.
Table of Contents
Page
Safety ….……………………................................................................2
Description....................................................................................2
Appropriate Use................................................................2
Pump Performance and Specifications..............................3
Installing the Pump.....................................................................4
Operation.....................................................................................5
Maintenance and Repair...........................................................5
Pump Dimensions.............................................................7
Repair Parts List................................................................................9
Trouble Shooting.........................................................................10
Safety
Read and carefully observe these operating instructions
before unpacking and operating the pump! The pump must
be operated, maintained and repaired exclusively by per-
sons familiar with the operating instructions. Local safety
regulations regarding installation, operation and
maintenance must be followed.
Operate this pump only after safety instructions and this
service manual are fully understood.
Indicates a potentially hazardous situation which, if not
avoided, could result in death or serious injury.
Indicates a potentially hazardous situation which, if not
avoided, may result in minor or moderate injury.
Safety Instructions
This equipment generates very high grease pressure.
Extreme caution should be used when operating this
equipment as material leaks from loose or ruptured
components can inject fluid through the skin and into the
body causing serious bodily injury. Adequate protection is
recommended to prevent splashing of material onto the
skin or into the eyes.
If any fluid appears to penetrate the skin, get emergency
medical care immediately. Do not treat as a simple cut.
Tell attending physical exactly what fluid was injected.
Inspection
If overpressurizing of the equipment is believed to have
occurred, contact the factory authorized warranty and service
center nearest you for inspection of the pump.
Specialized equipment and knowledge is required for repair
of this pump. Contact the factory authorized warranty and
To order call 1-800-548-1191 or visit www.partdeal.com - [email protected]