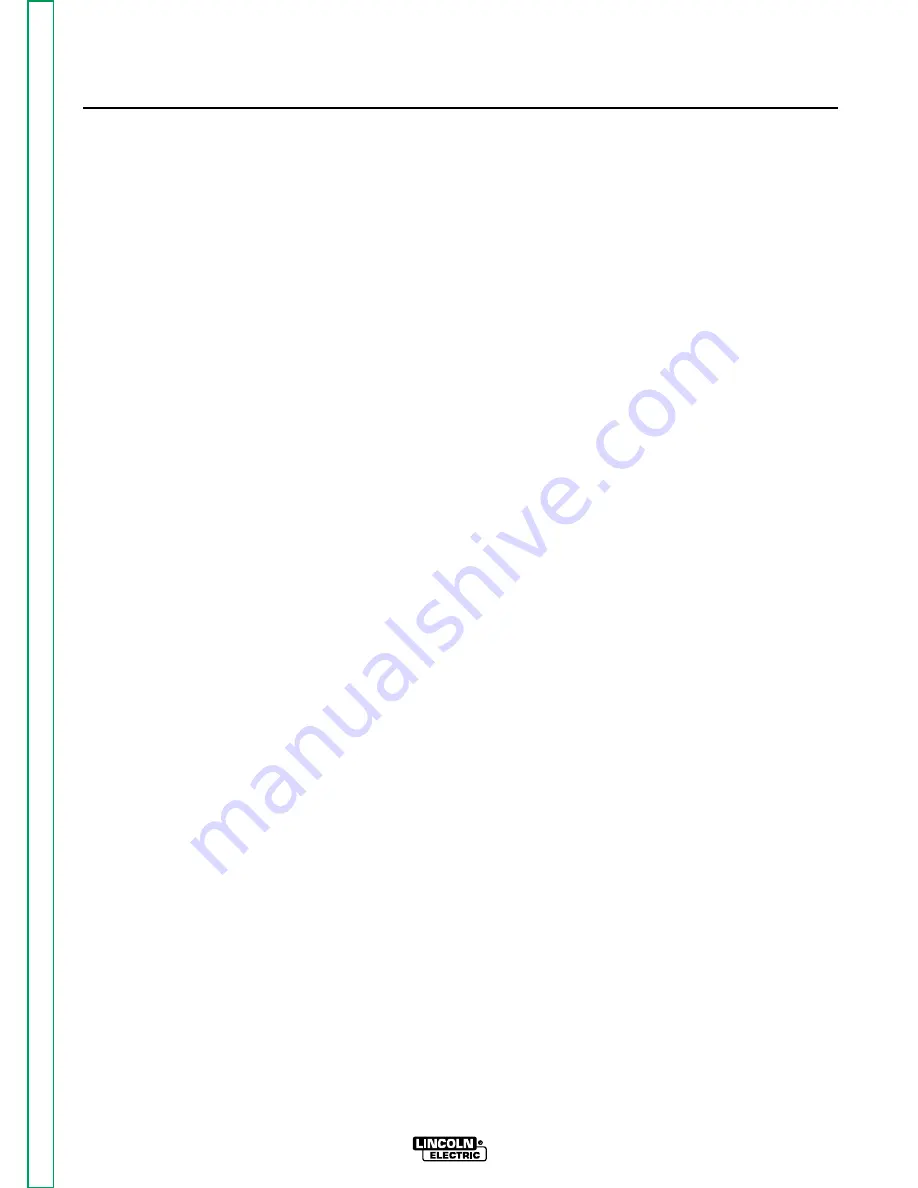
Section B-1
Section B-1
WELDANPOWER 125
TABLE OF CONTENTS
- OPERATION SECTION -
Operation
...............................................................................................................................
Section B
Safety Instructions ......................................................................................................................B-2
General Description ....................................................................................................................B-2
Recommended Applications ......................................................................................................B-3
Welder .................................................................................................................................B-3
Generator .............................................................................................................................B-3
Operational Features and Controls ............................................................................................B-3
Design Features and Advantages...............................................................................................B-3
Welding Capability ......................................................................................................................B-3
Limitations .................................................................................................................................B-3
Controls and Settings ................................................................................................................B-4
Welder/Generator Controls ..................................................................................................B-4
Gasoline Engine Controls.....................................................................................................B-5
Engine Operation ........................................................................................................................B-6
Before Starting the Engine ..................................................................................................B-6
Starting the Engine ..............................................................................................................B-6
Stopping the Engine ............................................................................................................B-7
Break-in Period ....................................................................................................................B-8
Welding Operation ......................................................................................................................B-8
Auxiliary Power Operation ........................................................................................................B-11
Retur
n to Master TOC
Retur
n to Master TOC
Retur
n to Master TOC
Retur
n to Master TOC