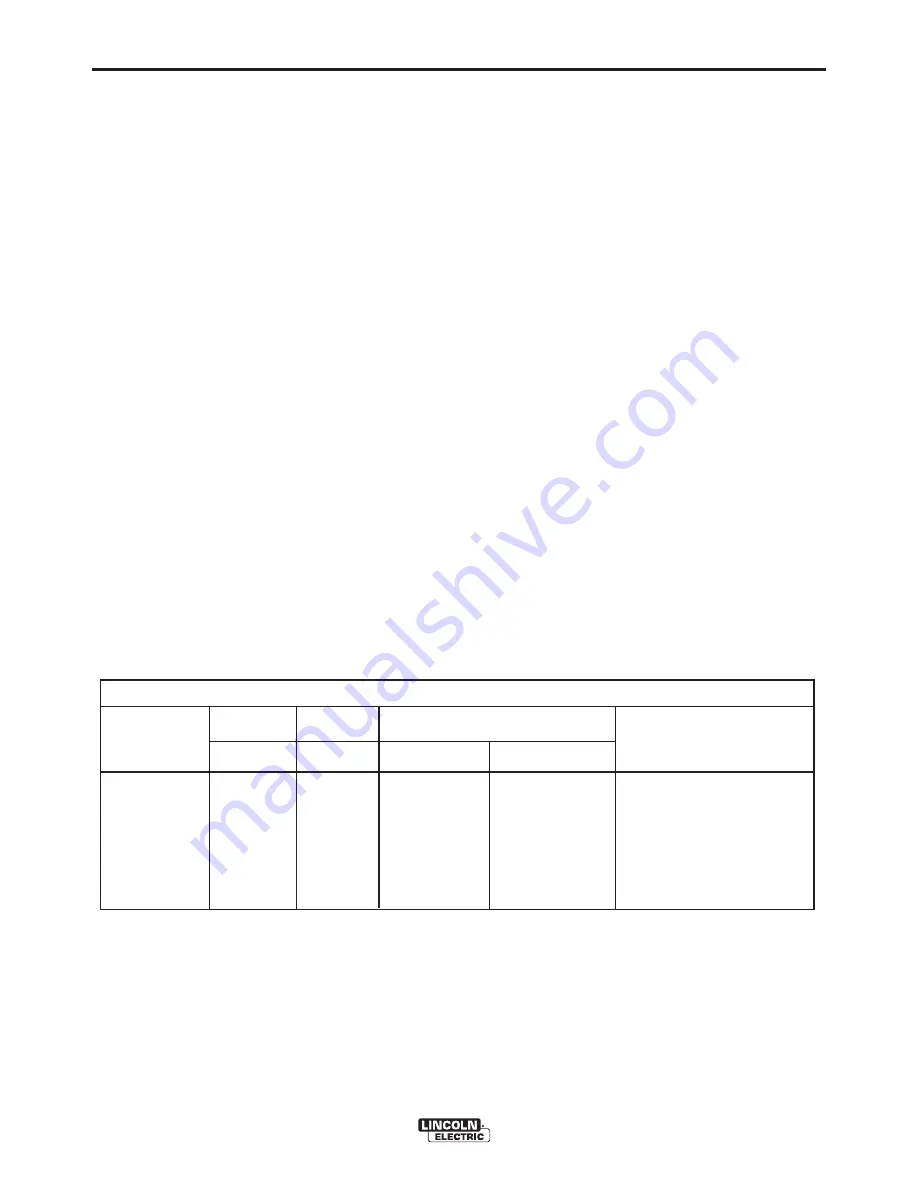
When in the TOUCH START TIG mode and when a
Amptrol is connected to the 6-Pin connector the OUT-
PUT CONTROL dial is used to set the maximum cur-
rent range of the current control of the Amptrol.
The ARC CONTROL is not active in the TIG mode. To
STOP a weld, simply pull the TIG torch away from the
work.
When the arc voltage reaches approximately 30 Volts
the arc will go out and the machine will reset the cur-
rent to the Touch Start level.
To reinitiate the arc, retouch the tungsten to the work
and lift. Alternatively, the weld can be stopped by
releasing the Amptrol or arc start switch.
The VANTAGE® 400 (AU) can be used in a wide vari-
ety of DC TIG welding applications. In general the
‘Touch Start’ feature allows contamination free start-
ing without the use of a Hi-frequency unit. If desired,
the K930-2 TIG Module can be used with the VAN-
TAGE® 400 (AU). The settings are for reference.
VANTAGE® 400 (AU) settings when using the K930-2
TIG Module with an Amptrol or Arc Start Switch:
• Set the MODE Switch to the TOUCH START TIG
setting.
• Set the "IDLER" Switch to the "AUTO" position.
• Set the "WELDING TERMINALS" switch to the
"REMOTELY CONTROLLED" position.
The OUTPUT CONTROL dial adjusts the full output
range for pipe welding.
The ARC CONTROL dial sets the short circuit current
(arc-force) during stick welding to adjust for a soft or
more forceful digging arc (crisp). Increasing the number
from -10(soft) to +10(crisp) increases the short circuit
current which results in a more forceful digging arc.
Typically a forceful digging arc is preferred for root and
hot passes. A softer arc is preferred for fill and cap pass-
es where weld puddle control and deposition (“stacking”
of iron) are key to fast travel speeds. This can also
increase spatter.
It is recommended that the ARC CONTROL be set to the
minimum number without electrode sticking. Start with
the dial set at 0.
NOte:
With the VRD switch in the “ON” position there is
no output in the DOWNHILL PIPE mode. For indicator
light operation, see table B.1.
tIG WeLDING
The TOUCH START TIG setting of the MODE switch is
for DC TIG (Tungsten Inert Gas) welding. To initiate a
weld, the OUTPUT CONTROL dial is first set to the
desired current and the tungsten is touched to the work.
During the time the tungsten is touching the work there is
very little voltage or current and, in general, no tungsten
contamination. Then, the tungsten is gently lifted off the
work in a rocking motion, which establishes the arc.
tyPICaL CURReNt RaNGes
(1)
fOR tUNGsteN eLeCtRODes
(2)
Tungsten Electrode DCEN (-) DCEP (+) Approximate Argon Gas Flow
TIG TORCH
Diameter in. (mm)
Flow Rate C.F.H. ( l /min.)
Nozzle Size (4), (5)
1%, 2% Thoriated 1%, 2% Thoriated Aluminum
Stainless Steel
Tungsten
Tungsten
.010 (.25) 2-15
(3)
3-8
(2-4)
3-8
(2-4)
#4, #5, #6
0.020
(.50) 5-20
(3)
5-10
(3-5)
5-10
(3-5)
0.040
(1.0) 15-80
(3)
5-10
(3-5)
5-10
(3-5)
1/16
(1.6) 70-150
10-20
5-10
(3-5)
9-13
(4-6)
#5, #6
3/32
(2.4) 150-250
15-30
13-17 (6-8)
11-15
(5-7)
#6, #7, #8
1/8
(3.2)
250-400
25-40
15-23 (7-11)
11-15
(5-7)
5/32
(4.0) 400-500
40-55
21-25
(10-12)
13-17
(6-8)
#8, #10
3/16
(4.8) 500-750
55-80
23-27 (11-13)
18-22
(8-10)
1/4
(6.4)
750-1000
80-125
28-32
(13-15)
23-27
(11-13)
(1) When used with argon gas. The current ranges shown must be reduced when using argon/helium or pure helium shielding gases.
(2) Tungsten electrodes are classified as follows by the American Welding Society (AWS):
Pure
EWP
1% Thoriated
EWTh-1
2% Thoriated
EWTh-2
Though not yet recognized by the AWS, Ceriated Tungsten is now widely accepted as a substitute for 2% Thoriated Tungsten in AC and DC applications.
(3) DCEP is not commonly used in these sizes.
(4) TIG torch nozzle "sizes" are in multiples of 1/16ths of an inch:
# 4 = 1/4 in.
(6 mm)
# 5 = 5/16 in.
(8 mm)
# 6 = 3/8 in.
(10 mm)
# 7 = 7/16 in.
(11 mm)
# 8 = _ in.
(12.5 mm)
#10 = 5/8 in.
(16 mm)
(5) TIG torch nozzles are typically made from alumina ceramic. Special applications may require lava nozzles, which are less prone to breakage, but cannot withstand high temperatures
and high duty cycles.
B-6
OPeRatION
B-6
taBLe B.3
VaNtaGe® 400 (aU)
Summary of Contents for VANTAGE 400 AU 11959
Page 39: ...f 1 DIaGRaMs f 1 VaNtaGe 400 aU...
Page 40: ...f 2 DIaGRaMs f 2 VaNtaGe 400 aU...
Page 41: ...f 3 DIaGRaMs f 3 VaNtaGe 400 aU...