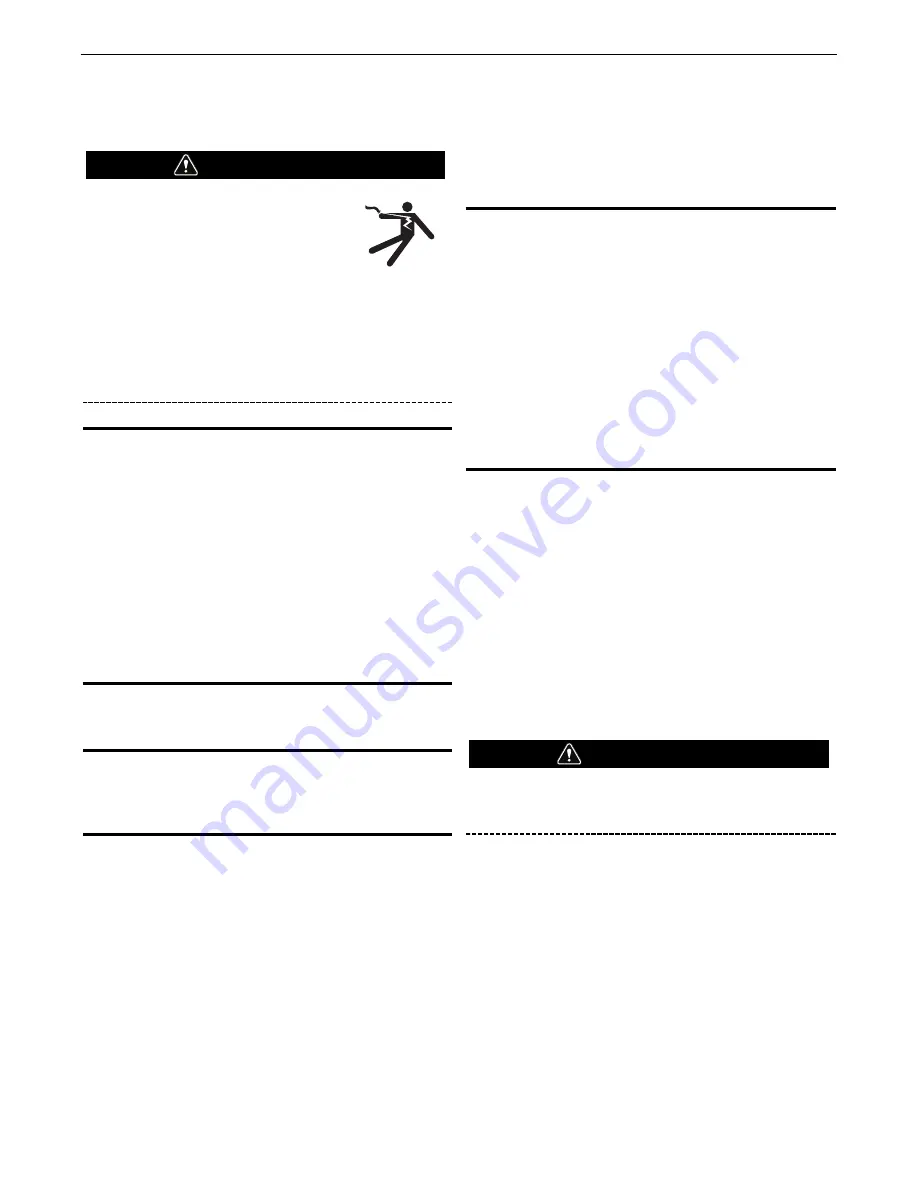
A-3
INSTALLATION
TOMAHAWK
®
1000
SAFETY PRECAUTIONS
Read entire Installation Section before installing the Tomahawk
®
1000 .
ELECTRIC SHOCK CAN KILL.
•
Only qualified personnel should install
this machine.
•
Turn the input power OFF at the
disconnect switch or fuse box and
discharge input capacitors before working inside the
equipment.
•
Do not touch electrically hot parts.
•
Turn the Tomahawk
®
1000 Power Switch OFF when
connecting power cord to input power.
SELECT PROPER LOCATION
Place the Tomahawk
®
1000 where clean cool air can freely
circulate in and out of the louvers. Dirt, dust or any foreign
material that can be drawn into the machine should be kept at a
minimum. Failure to observe these precautions can result in
excessive operating temperatures and nuisance shutdown of the
machine.
A source of clean, dry air or nitrogen must be supplied to the
Tomahawk
®
1000. Oil in the air is a severe problem and must be
avoided. The supply pressure must be between 80 and 110 psi.
The flow rate is approximately 4.0 cfm (113 l/min.). Failure to
observe these precautions could result in excessive operating
temperatures or damage to the torch.
STACkING
The Tomahawk
®
1000 cannot be stacked.
TILTING
The Tomahawk
®
1000 must be placed on a stable, level surface
so it will not topple over.
HIGH FREQUENCY INTERFERENCE PROTECTION
The Tomahawk
®
1000 employs a touch start mechanism for arc
initiation which eliminates high frequency emissions from the
machine as compared with spark gap and solid state type high
frequency generators. Keep in mind, though, that these machines
may be used in an environment where other high frequency
generating machines are operating. By taking the following steps,
high frequency interference into the Tomahawk
®
1000 can be
minimized
(1) Make sure the power supply chassis is connected to a good
earth ground. The work terminal ground does NOT ground
the machine frame.
(2) Keep the work clamp isolated from other work clamps that
have high frequency.
(3) If the work clamp cannot be isolated, then keep the clamp as
far as possible from other work clamp connections.
(4) When the machine is enclosed in a metal building, several
good earth driven electrical grounds around the periphery of
the building are recommended.
Failure to observe these recommended installation procedures
may cause improper function of the Tomahawk
®
1000 or possibly
even damage to the control system or power supply components.
INPUT ELECTRICAL CONNECTIONS
The Tomahawk
®
1000 is rated for 208VAC through 575VAC input
voltages. Before installing the machine, check that input supply
voltage, phase, and frequency are the same as the machine's
voltage, phase, and frequency as specified on the machine's
rating plate.
•
Automatically senses and adjusts to input power for a range
of 200 up to 600 volts, single or three phase, 50 to 60 hertz.
Cutting output remains constant throughout the entire input
voltage range.
•
The Tomahawk
®
1000 should be connected only by a
qualified electrician. Installation should be made in
accordance with local codes.
INPUT PLUG INSTALLATION
POWER CORD CONNECTION
A power cord is provided and wired into the machine. Follow the
power cord connection instructions.
Single Phase Input
Connect green lead to ground per National Electrical Code.
Connect black and red leads to power.
Wrap white lead with tape to provide 600V insulation.
Three Phase Input
Connect green lead to ground per National Electric Code.
Connect black, red and white leads to power.
Failure to wire as instructed may cause personal injury or
damage to equipment. To be installed or checked by an
electrician or qualified person only.
In all cases, the green or green/yellow grounding wire must be
connected to the grounding pin of the plug, usually identified by a
green screw.
Attachment plugs must comply with the Standard for Attachment
Plugs and Receptacles, UL498.
The product is considered acceptable for use only when an
attachment plug as specified is properly attached to the supply
cord.
WARNING
WARNING
Summary of Contents for Tomahawk 1000
Page 7: ...3 SAFETY...
Page 33: ......