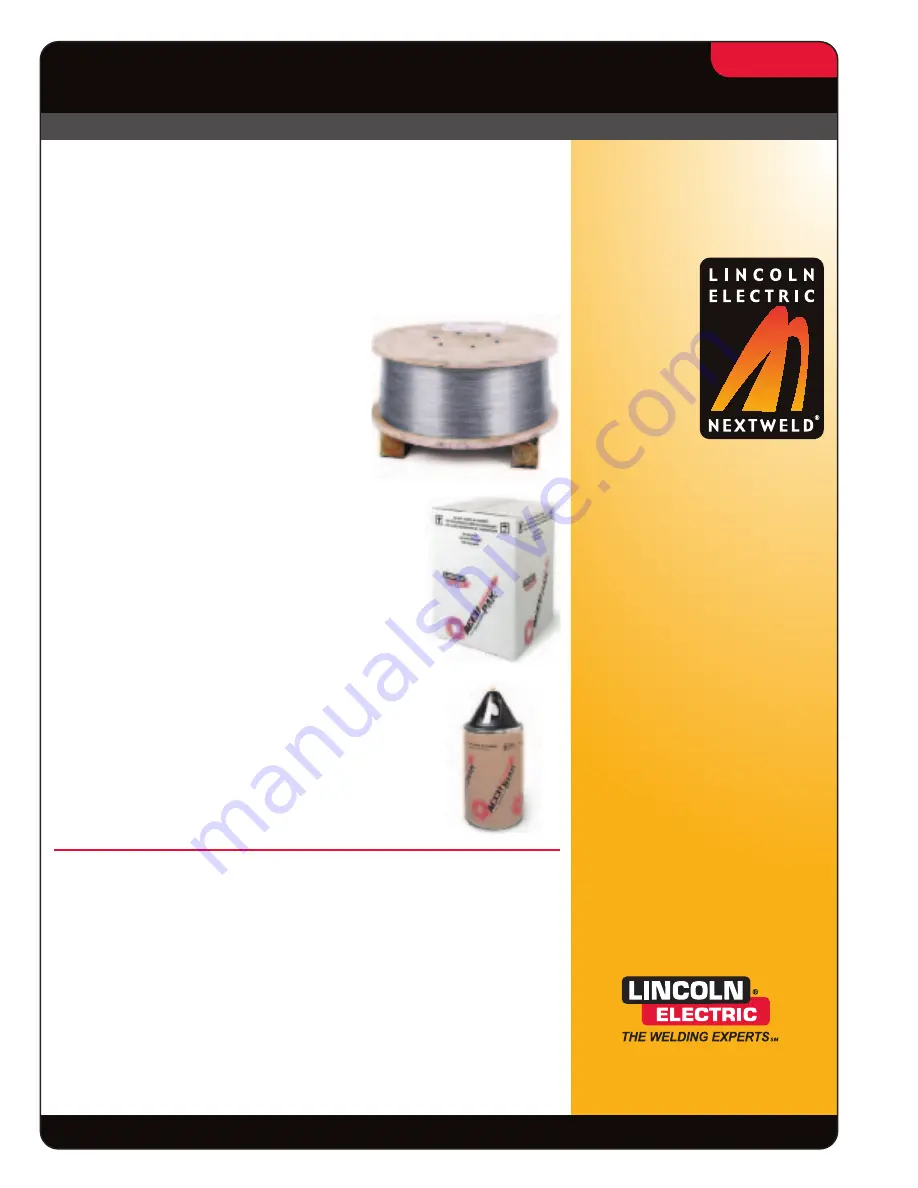
Tandem MIG
T
h
e
f
u
t
u
r
e
o
f
w
e
l
d
i
n
g
i
s
h
e
r
e
.
®
THE LINCOLN ELECTRIC COMPANY
www.lincolnelectric.com
1.216.481.8100
Customer Assistance Policy
The business of The Lincoln Electric Company is manufacturing and selling high quality welding equipment,
consumables, and cutting equipment. Our challenge is to meet the needs of our customer and to exceed
their expectations. On occasion, purchasers may ask Lincoln Electric for advice or information about their
use of our products. We respond to our customers based on the best information in our possession at that
time. Lincoln Electric is not in a position to warrant or guarantee such advice, and assumes no liability, with
respect to such information or advice. We expressly disclaim any warranty of any kind, including any
warranty of fitness for any customer’s particular purpose, with respect to such information or advice. As a
matter of practical consideration, we also cannot assume any responsibility for updating or correcting any
such information or advice once it has been given, nor does the provision of information or advice create,
expand or alter any warranty with respect to the sale of our products.
Lincoln Electric is a responsive manufacturer, but the selection and use of specific products sold by
Lincoln Electric is solely within the control of, and remains the sole responsibility of the customer. Many
variables beyond the control of Lincoln Electric affect the results obtained in applying these types of
fabrication methods and service requirement.
Subject to change
- This information is accurate to the best of our knowledge at the time of printing.
Please refer to
www.lincolnelectric.com
for any updated information.
WHAT IS NEXTWELD?
The challenges facing industrial
fabricators today are increasingly
difficult. Rising labor, material, and
energy costs, intense domestic and
global competition,
a dwindling pool of
skilled workers,
more stringent and
specific quality
demands.
Through our
commitment to
extensive research
and investments in
product
development,
Lincoln Electric has
established an industry benchmark for
applying technology to improve the
quality, lower the cost and enhance the
performance of arc welding processes.
Advancements in power electronics,
digital communications and Waveform
Control Technology™ are the foundation
for many of the improvements.
NEXTWELD brings you a series of
Process, Technology, Application and
Success Story documents like this one.
NEXTWELD explains how technologies,
products, processes and applications are
linked together to answer the important
questions that all businesses face:
• How can we work faster, smarter,
more efficiently?
• How can we get equipment and
people to perform in ways they’ve
never had to before?
• How do we stay competitive?
NEXTWELD is the future of welding but
its benefits are available to you today.
Ask your Lincoln Electric representative
how to improve the flexibility, efficiency
and quality of your welding operations to
reduce your cost of fabrication.
APPLICATION
16/16
High-Speed and High-Deposition Welding
W A V E F O R M C O N T R O L T E C H N O L O G Y
T M
Lincoln Consumables used with Tandem MIG
SuperArc
®
/SuperGlide
®
Lincoln’s SuperArc, our premium copper-coated MIG wire, and
SuperGlide, our premium bare wire, are the choice of welders
and welding decision-makers everywhere because of their
exceptional consistency, feedability, and arc action.
A better arc means less spatter, less clean-up, and improved
productivity – and premium SuperArc and SuperGlide deliver
the best arc in MIG welding.
Our MicroGuard™ Ultra surface treatment,
with proprietary arc enhancement agents,
facilitates excellent weld puddle control, very
good wetting action, straight bead edges, and
a wider operating range.
The exceptional feeding characteristics of
SuperGlide, made possible by MicroGuard Ultra
surface treatment, translate to reduced
down-time and high operator appeal.
Accu-Pak
®
100% Recyclable Patented Package — when the
wire is consumed, just remove the components,
collapse the box and throw into the recycle bin.
Lifting Strap for ease of movement from one location
to the next. Patented Ring Design.
Accu-Trak
®
This Accu-Trak Drum Payoff Kit is made of a
durable plastic for superior strength and integrity.
It also features two viewing windows 180° apart
from one another for easy viewing of the wire as
it is paying off.
A Payoff Kit must be used with Accu-Trak Drums
to ensure precise feeding. The fitting on top of the
Payoff Kit has a 1/2-14 NPT internal pipe thread
to facilitate the connection of the conduit to 500 lb.
Accu-Trak drums.