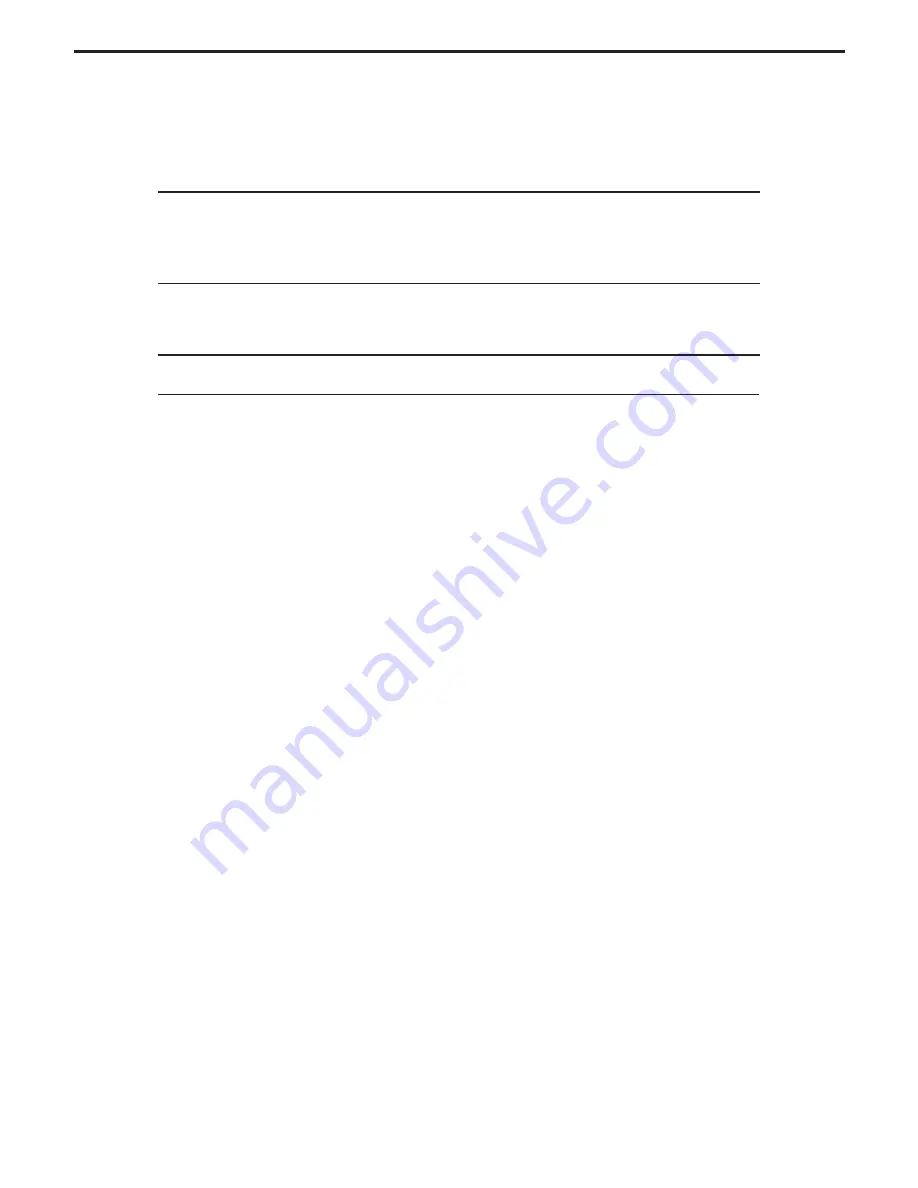
vii
TABLE OF CONTENTS
Page
Maintenance ....................................................................................................Section D
Safety Precautions ................................................................................................D-1
Input Filter Capacitor Discharge Procedure ..........................................................D-1
Routine Maintenance.............................................................................................D-2
Periodic Maintenance ............................................................................................D-2
Troubleshooting ..............................................................................................Section E
Safety Precautions.................................................................................................E-1
How to Use Troubleshooting Guide.......................................................................E-1
Troubleshooting Guide ..........................................................................................E-2
Wiring Diagrams ..............................................................................................Section F
Wiring Diagrams.......................................................................................F-1 thru F-3
Dimension Print......................................................................................................F-4
Parts List ....................................................................................P342 Series & P210-K
Summary of Contents for RED-D-ARC IM648-B
Page 4: ...PYTHON iii NOTES iii ...