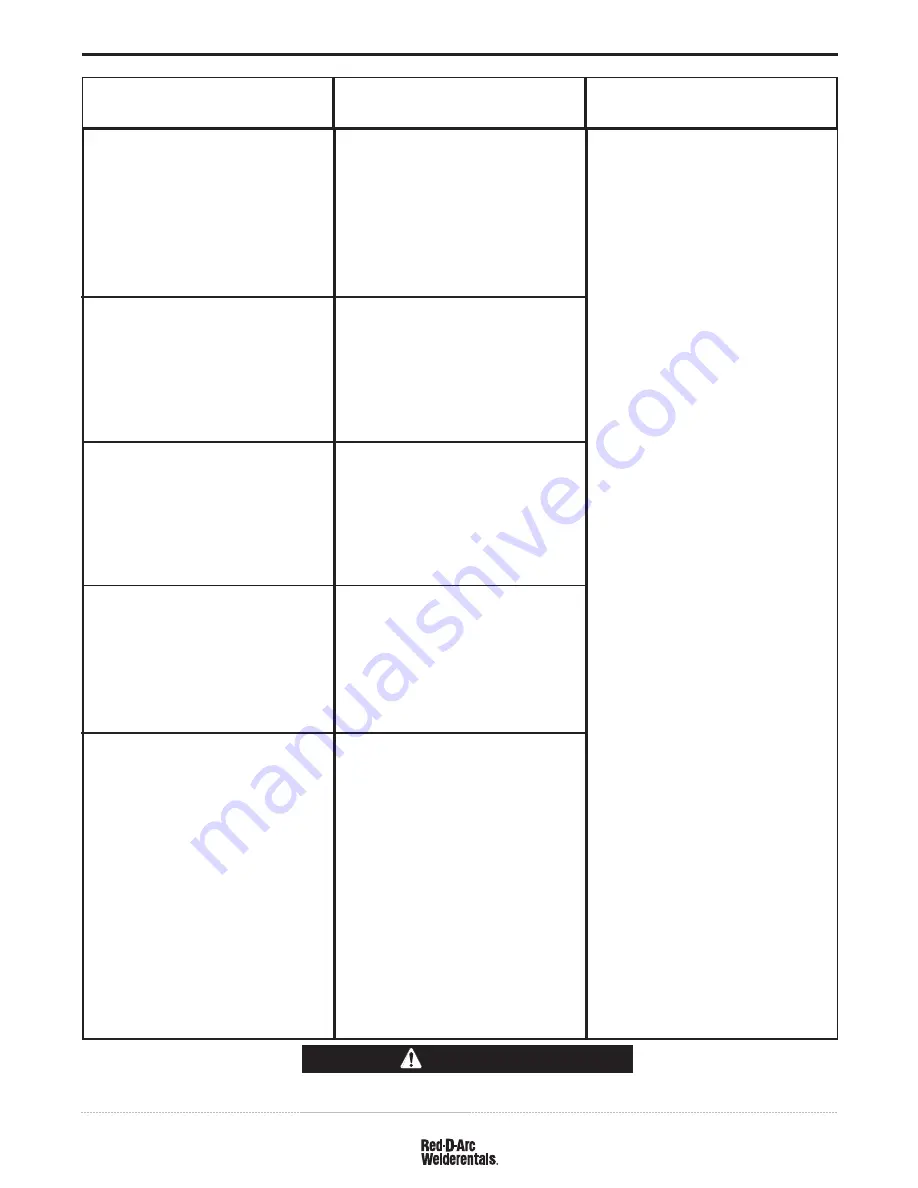
E-3
TROUBLESHOOTING
E-3
Observe all Safety Guidelines detailed throughout this manual
If for any reason you do not understand the test procedures or are unable to perform the tests/repairs safely, contact your
Local Authorized Field Service Facility
for technical troubleshooting assistance before you proceed.
CAUTION
PROBLEMS
(SYMPTOMS)
POSSIBLE
CAUSE
RECOMMENDED
COURSE OF ACTION
Engine shuts down while under a
load.
Engine runs rough.
Battery does not stay charged.
Engine alternator trouble light is on
while machine is running.
Engine will not idle down to low
speed.
Engine will not go to high idle when
attempting to weld.
1. High radiator coolant tempera-
ture. Reduce load if it is exceed-
ing machine rating. Add coolant
to system if low. Clean fins on
radiator if dirty. Tighten fan belt if
loose. Remove objects blocking
or close to intake openings on
both sides of base and exhaust
end (case back).
1. Dirty fuel or air filters. Inspect and
clean/replace filters as needed.
Inspect and clean/replace filters
as needed.
2. Water in fuel. If water found in
tank. Empty fuel tank and refill
then purge fuel lines.
1. Faulty battery. Replace.
2. Loose connections at battery or
alternator. Clean and tighten con-
nections.
3. Faulty engine alternator or charg-
er module. Consult authorized
Engine Service Shop.
1. Idler switch in High idle position.
Set switch to Auto.
2. External load on welder or auxil-
iary power. Remove all external
loads.
3. Faulty Engine Control Unit or
Control P.C. board.
1. Poor work lead connection to
work. Make sure work clamp is
tightly connected to clean base
metal.
2. "Contactor" switch is in wrong
position. Set to "Welding On" when
welding without a control cable.
Refer to Operations chapter for prop-
er use of this switch.
3. Faulty Engine Control Unit or
Control P.C. board.
If all recommended possible areas of
misadjustment have been checked
and the problem persists,
Contact
your local Authorized Field
Service Facility.
DX450 (RED-D-ARC)
Summary of Contents for RED-D-ARC DX450
Page 38: ...F 1 DIAGRAMS F 1 DX450 RED D ARC ...
Page 39: ...F 2 DIAGRAMS F 2 DX450 RED D ARC ...
Page 40: ...F 3 DIAGRAMS F 3 DX450 RED D ARC ...
Page 41: ...F 4 DIAGRAMS F 4 DX450 RED D ARC ...
Page 42: ...F 5 DIAGRAMS F 5 DX450 RED D ARC 2 9 03 ...
Page 43: ...F 6 DIAGRAMS F 6 DX450 RED D ARC ...
Page 46: ...NOTES DX450 RED D ARC ...
Page 47: ...NOTES DX450 RED D ARC ...