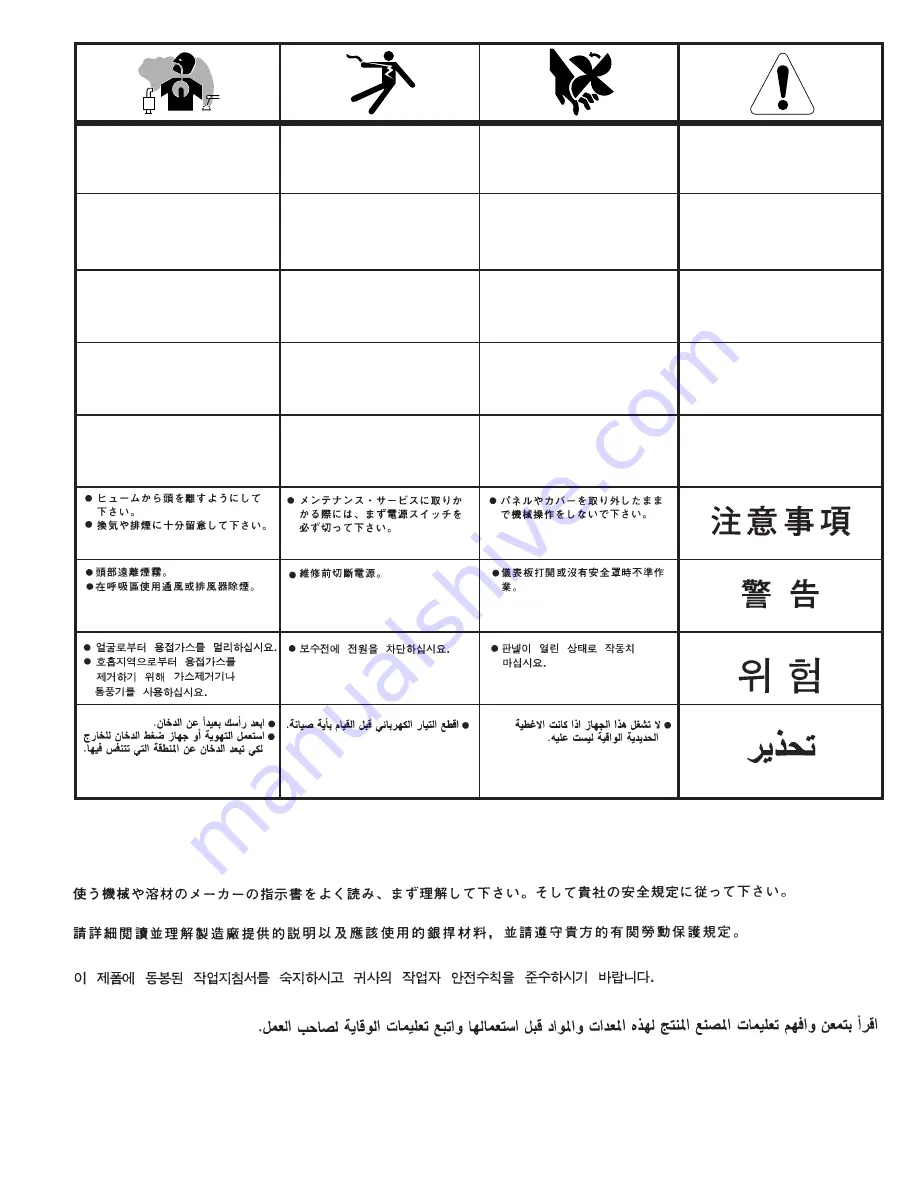
WARNING
AVISO DE
PRECAUCION
ATTENTION
WARNUNG
ATEN
ÇÃ
O
Spanish
French
German
Portuguese
Japanese
Chinese
Korean
Arabic
LEIA E COMPREENDA AS INSTRUÇÕES DO FABRICANTE PARA ESTE EQUIPAMENTO E AS PARTES DE USO, E SIGA AS
PRÁTICAS DE SEGURANÇA DO EMPREGADOR.
●
Keep your head out of fumes.
●
Use ventilation or exhaust to
remove fumes from breathing zone.
●
Los humos fuera de la zona de res-
piración.
●
Mantenga la cabeza fuera de los
humos. Utilice ventilación o
aspiración para gases.
●
Gardez la tête à l’écart des fumées.
●
Utilisez un ventilateur ou un aspira-
teur pour ôter les fumées des zones
de travail.
●
Vermeiden Sie das Einatmen von
Schweibrauch!
●
Sorgen Sie für gute Be- und
Entlüftung des Arbeitsplatzes!
●
Mantenha seu rosto da fumaça.
●
Use ventilação e exhaustão para
remover fumo da zona respiratória.
●
Turn power off before servicing.
●
Desconectar el cable de ali-
mentación de poder de la máquina
antes de iniciar cualquier servicio.
●
Débranchez le courant avant l’entre-
tien.
●
Strom vor Wartungsarbeiten
abschalten! (Netzstrom völlig öff-
nen; Maschine anhalten!)
●
Não opere com as tampas removidas.
●
Desligue a corrente antes de fazer
serviço.
●
Não toque as partes elétricas nuas.
●
Do not operate with panel open or
guards off.
●
No operar con panel abierto o
guardas quitadas.
●
N’opérez pas avec les panneaux
ouverts ou avec les dispositifs de
protection enlevés.
●
Anlage nie ohne Schutzgehäuse
oder Innenschutzverkleidung in
Betrieb setzen!
●
Mantenha-se afastado das partes
moventes.
●
Não opere com os paineis abertos
ou guardas removidas.