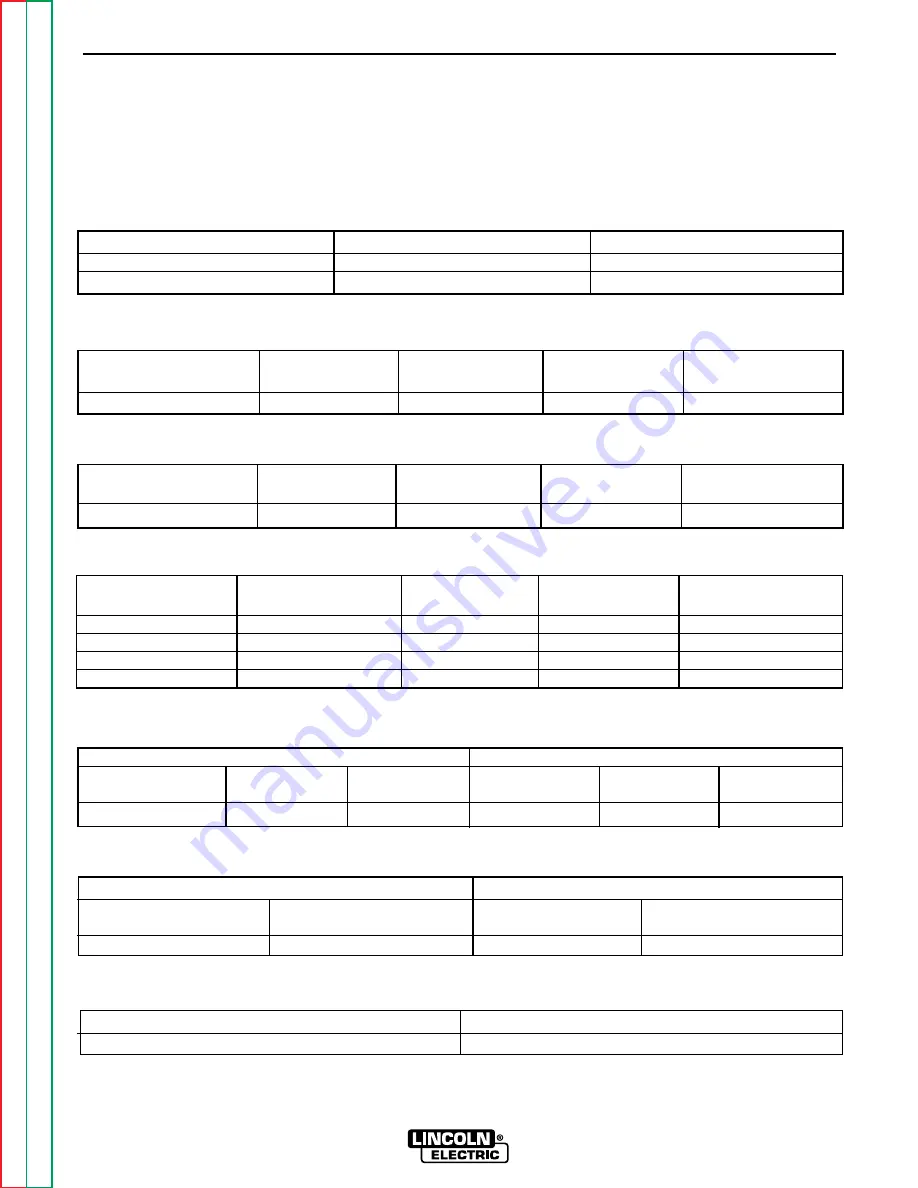
Retur
n to Section TOC
Retur
n to Section TOC
Retur
n to Section TOC
Retur
n to Section TOC
Retur
n to Master TOC
Retur
n to Master TOC
Retur
n to Master TOC
Retur
n to Master TOC
TROUBLESHOOTING & REPAIR
F-70
F-70
RANGER 10-LX
RETEST AFTER REPAIR
Retest a machine:
• If it is rejected under test for any reason that requires you to remove any mechanical part which could affect the
machine’s electrical characteristics. OR
• If you repair or replace any electrical components.
ENGINE OUTPUT
Mode
No Load RPM
Load RPM
Low Idle
2150-2250
NA
High Idle
3650-3700
3400-3650
WELDER DC OUTPUT
1
Output Control
Range Switch
Open Circuit
Load Volts
Load Amps
Volts
Maximum
Maximum
61 - 68
25 - 35
250 - 285
WELDER AC OUTPUT
1
Output Control
Range Switch
Open Circuit
Load Volts
Load Amps
Volts
Maximum
Maximum
70 - 76
25 - 35
250 - 305
WELDER CV OUTPUT
1
Output Control
Range Switch
Open Circuit
Load Volts
Load Amps
Volts
Maximum
Wire Feed CV High
59 - 62
30 - 34
250 - 280
Maximum
Wire Feed CV Med HI
42 - 45
23 - 26
220 - 240
Maximum
Wire Feed CV Med LO
33.5 - 36
19 - 21
155 - 170
Maximum
Wire Feed CV Low
25 - 27
14.5 - 16
135 - 155
AUXILIARY POWER OUTPUT
230 Volt Receptacle
115 Volt Receptacle
2
Open Circuit
Load Volts
Load Amps
Open Circuit
Load Volts
Load Amps
Voltage
Voltage
245 - 253
210 - 240
43 - 48
120 - 127
106 - 121
78 - 83
AMPHENOL AUXILIARY OUTPUT
42 Volt Auxiliary
115 Volt Receptacle
2
Open Circuit
Load Volts
Open Circuit
Load Volts
Voltage
Voltage
43 - 50
40 - 48
115 - 126
110 - 126
FIELD AMPS AND VOLTS
Slip Ring Volts
Field Amps
37 - 47 VDC
6 - 6.8 Amps DC
1
OUTPUT CONTROL switch set at MAXIMUM (position 10).
2
Output values of each receptacle can vary within the range shown but must be within 2 volts of each other.