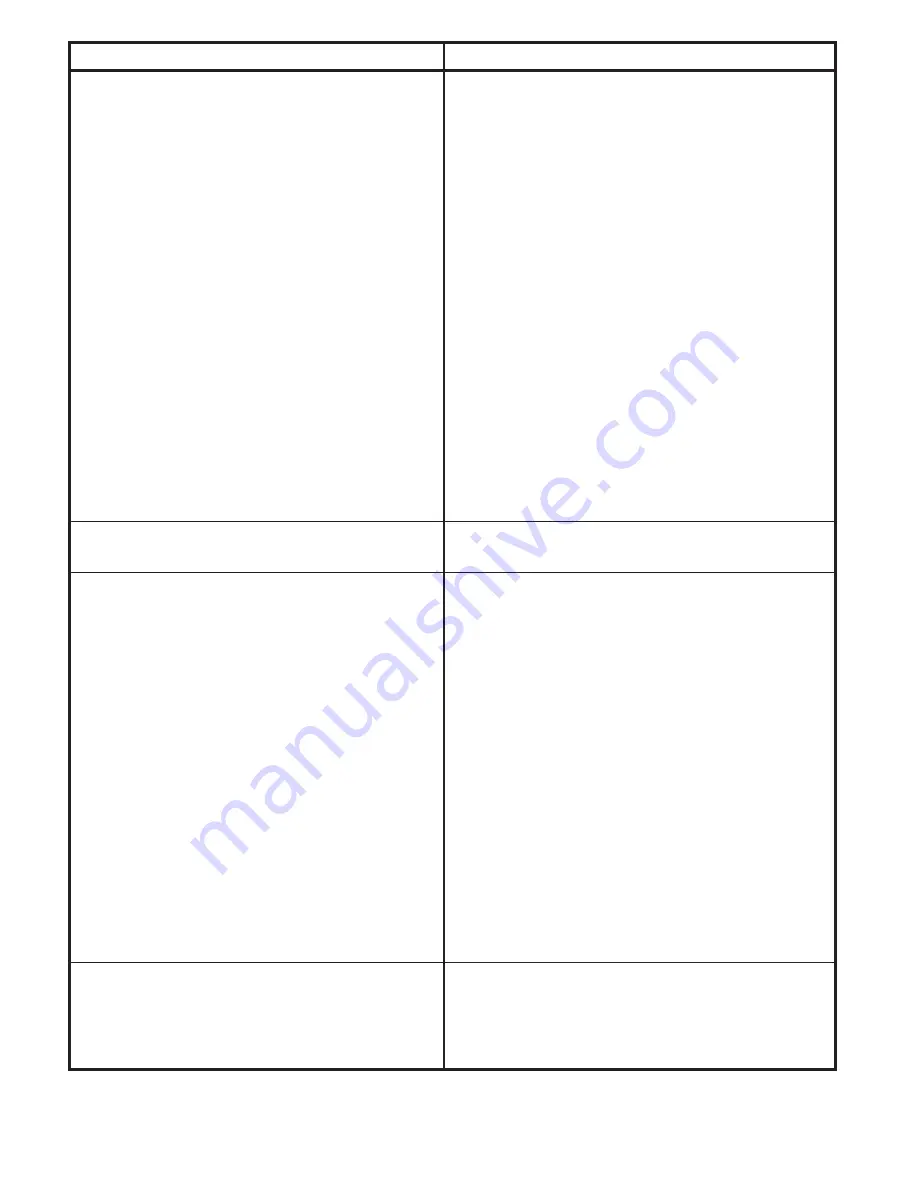
– 18 –
SYMPTOM
CHECK
The “MALFUNCTION” LED is lit.
1.
The MALFUNCTION circuit monitors the torch
to see if it is shorted as well as internal machine
failures.
2.
Check the torch consumables to see if they are
melted together or are simply touching each
other. Tighten, clean or replace. See
“Suggestion for Extra Utility from the PRO-CUT
System”.
3.
Check the torch cable to see if it is cut or
punctured. Replace.
4.
Turn off the machine and turn it back on. If the
“MALFUNCTION” LED will not stay off when you
try to cut again and there is no problem with the
torch, then something has failed in the machine
and the machine should not be left on.
A. Check electrode to pilot for short.
B. Check airflow.
C. Check the power board. During preflow,
there should be no voltage between work a
and electrode and at end of preflow open cir-
cuit voltage should be present. Replace if
bad.
5.
Replace PWM CONTROL BOARD.
6.
Replace MICRO CONTROL BOARD.
Alternating “AIR/MALFUNCTION” LED lights
1.
Replace MICRO CONTROL BOARD.
The “SAFETY” LED is lit.
1.
The machine will not operate. The machine
senses that the nozzle is not in place, or the
operators could be exposed to dangerous
voltages if the machine were allowed to operate.
2.
Check the nozzle to be sure it is tightly in place.
3.
Check the torch consumables to see if they are
melted together or are simply touching each
other. Tighten, clean or replace. See
“Suggestion for Extra Utility from the Pro-Cut
System”.
4.
Check the torch cable to see if it is cut or
punctured. Replace.
5.
Check to see that the torch is hooked to the
machine properly.
6.
Push the ‘SAFETY RESET” button, the LED
should go out.
7.
This circuit rarely trips on power up or because
of noise. If the circuit can be reset, it is OK to
continue operation.
8.
Replace PWM CONTROL BOARD, as this is a
safety problem.
The “OUTPUT ON” and “MALFUNCTION” LED’s
1.
The pilot arc duty cycle has been exceeded.
blink in alternating order.
The machine will cool down and the lights will
quit blinking in about 30 seconds. The pilot arc
is limited to 30 out of 60 seconds.