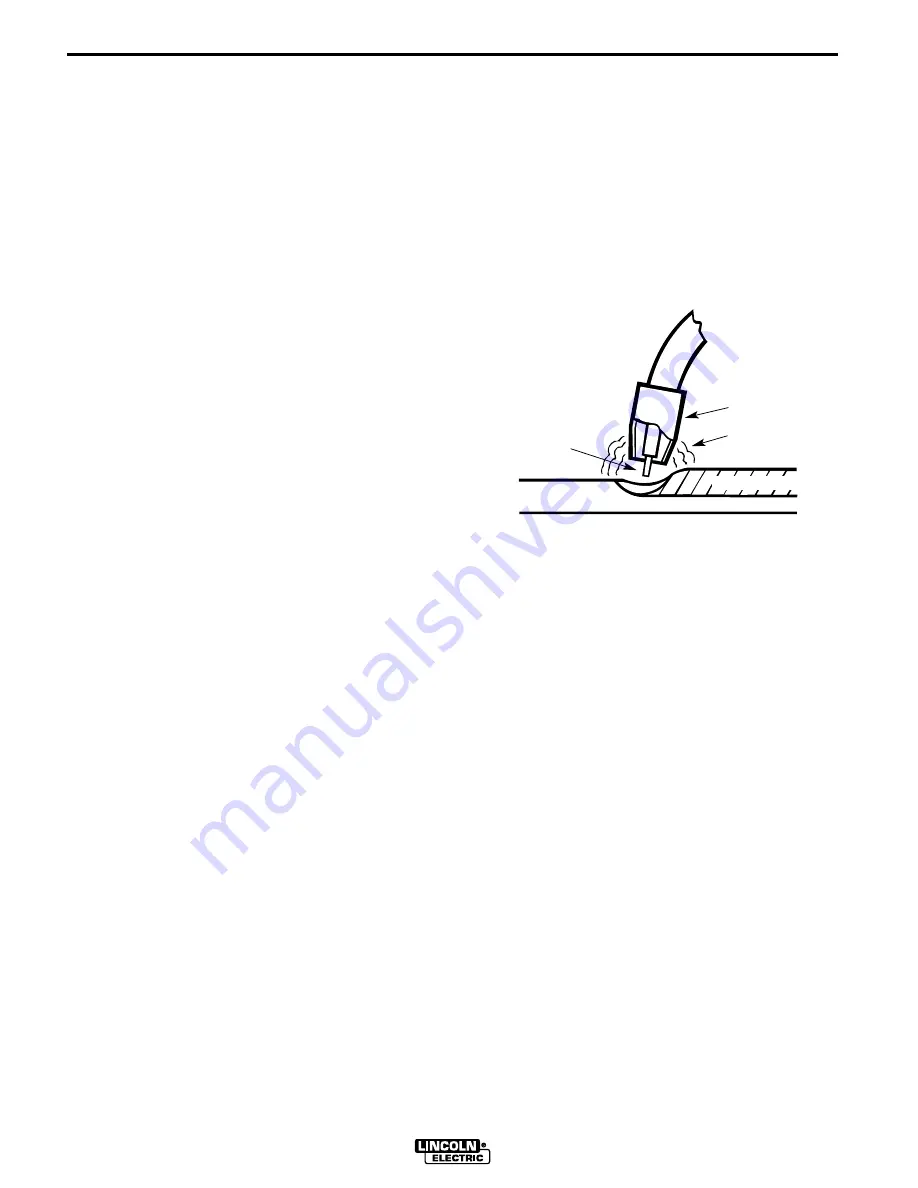
B-8
PRO 155
B-8
LEARNING TO WELD
The
“
arc stream
”
is seen in the middle of the picture.
This is the electric arc created by the electric current
flowing through the space between the end of the wire
electrode and the base metal. The temperature of this
arc is about 6000
°
F, which is more than enough to
melt metal. The arc is very bright, as well as hot, and
cannot be looked at with the naked eye without risking
painful injury. The very dark lens, specifically designed
for arc welding must be used with the hand or face
shield whenever viewing the arc.
The arc melts the base metal and actually digs into it
much as water through a nozzle on a garden hose
digs into the earth. The molten metal forms a molten
pool or crater and tends to flow away from the arc. As
it moves away from the arc, it cools and solidifies.
The function of the Innershield cored wire electrode is
much more than simply to carry current to the arc. The
wire core is composed of fluxes and/or alloying ingre-
dients around which a steel sheath has been formed.
It is simply a stick electrode turned inside out in a con-
tinuous wire form.
The cored wire melts in the arc and tiny droplets of
molten metal shoot across the arc into the molten
pool. The wire sheath provides additional filler metal
for the joint to fill the groove or gap between the two
pieces of base metal.
The core materials also melt or burn in the arc and
perform several functions. They make the arc stead-
ier, provide a shield of smoke-like gas around the arc
to keep oxygen and nitrogen in the air away from the
molten metal, and provide a flux for the molten pool.
The flux picks up impurities and forms the protective
slag on top of the weld during cooling.
After running a weld bead, the slag may be removed
with a chipping hammer and wire brush. This
improves appearance and allows for inspection of the
finished weld.
Since machine size and output characteristics limit the
size and type of wire electrode which can be used,
Lincoln 0.035
’
(0.9 mm) NR-211-MP Innershield elec-
trode is recommended for Self-Shielded Flux Cored
Arc Welding.
THE GMAW (MIG) WELDING ARC
Figure B.10 illustrates the GMAW (MIG) welding arc.
Solid wire does not contain fluxes or ingredients to
form its own shielding and no slag forms to protect the
molten weld metal. For this reason, a continuous even
flow of shielding gas is needed to protect the molten
weld metal from atmospheric contaminants such as
oxygen and nitrogen. Shielding gas is supplied
through the gun and cable assembly, through the gas
nozzle and into the welding zone.
When comparing the GMAW and FCAW processes,
you can see that the principal difference between the
two lies in the type of shielding used. GMAW uses gas
for shielding, thus we have Gas Metal Arc Welding.
FCAW uses the melting or burning of the core ingredi-
ents for shielding, and is thus termed Self-Shielded
Flux Cored Arc Welding.
The recommended wire for Gas Metal Arc Welding
(MIG) is Lincolnweld 0.025
”
L-56 electrode.
Lincolnweld
”
L-56 is capable of welding a wide range
of mild steels in all positions, however, more skill IS
required for out-of-position welding with the GMAW
process.
PROCESS SELECTION
By gaining knowledge of the differences between the
two processes, you will be able to select the best
process for the job you have at hand. In selecting a
process, you should consider:
For GMAW (MIG) Process
1. Is most of my welding performed on 16 gauge and
lighter materials?
FIGURE B.10
Gas nozzle
Shielding gas
Solid wire
electrode
Base metal
Weld metal
Summary of Contents for PRO 155
Page 31: ...B 18 PRO 155 B 18 APPLICATION CHART ...
Page 42: ...NOTES PRO 155 ...