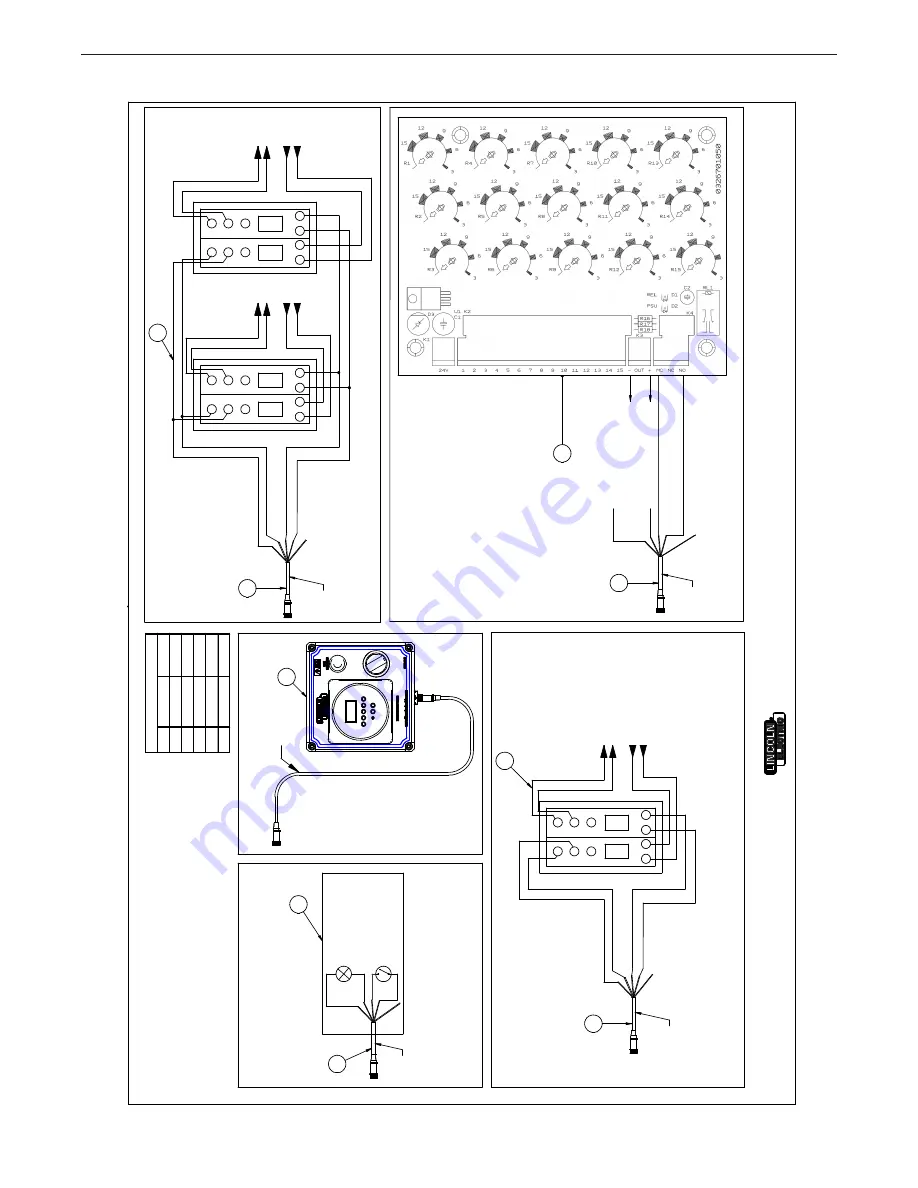
F-9
DIAGRAMS
L17587-5, L17587-6, L17587-7, L17587-8, L17587-9, L17587-11, L17587-29,
L17587-30, L17587-31, L17587-32, L17587-33 & L17587-34 SCHEMATIC
PRISM
®
Sales
and
Service
through
Su
bsidiaries
an
d
Distribu
tors
Worldwide
Cleveland,
Ohio
44
117-11
99
U.S.A.
THE
LI
NC
OLN
ELECTR
IC
COMP
ANY
World's
Le
ader
in
Welding
and
Cutting
Prod
ucts
S327
15-12
7PRINT
A.14
BK
BL
BR
WH
GR
N.E.
18
N.B.
WHITE
BROWN
CONTR
OL OPTION
5
CONTROL
OP
TION
2
CONTROL
OPTION 3
CONTROL
OP
TION
1
16
24
V
DC
LAMP
IN
DICATOR
ROBOT ON/OFF
SWITCH
BK
BL
BR
WH
GR
N.E.
18
N.B.
-
+
17
19
20
X2-01
An-Com
TO
VFD
X2-02
An-In
MOTOR
SPEED
CONTROL
OPTIONS
:
CON
NECT
DUC
T
PRESSU
RE
TRANS
M
ITTER
TO
VFD
SPEED
CONTROL
AS
SHOWN
IN
DETAIL
B
CON
NECT
IF-15
ANALO
G
OUT
TO
VFD
SPEED
CONTROL
AS
SHOWN
BELOW
*ITEM
19
QUANTITY
IS
1
FOR
THIS
OPTION
CONTROL
OPTION 4
GR
N.E.
18
N.B.
*ITEM
19
QUANTITY
IS
2
FOR
THIS
OPTION
19
N/C
N/C
N/C
N/C
N/C
GR
N.E.
18
N.B.
ROBOT
1
CONTROL
LER
FAN
START/STOP
FE
EDBACK
INDICATION
OUTPUT
INPUT
IN
DICATION
SOLID
ON
=
RUNN
ING
BLINKING=
FAULT
OR
FILTER
CH
ANGE
TU
RN
ON
CONTIN
UOUSLY
TO
RUN
FAN
BLACK
BLUE
BROWN
WHITE
FAN
STA
RT/STOP
FEED
BACK
INDICATION
ROBOT
1
N/C
ITEM
18
CON
NECTS
TO
ITEM
4
IN
PAGE
1
N.H.
ROBOT
1
CONTROL
LER
FAN
START/STOP
FE
EDBACK
INDICATION
OUTPUT
INPUT
IN
DICATION
SOLID
ON
=
RUNN
ING
BLINKING=
FAULT
OR
FILTER
CH
ANGE
TU
RN
ON
CONTIN
UOUSLY
TO
RUN
FAN
BLACK
BLUE
BROWN
WHITE
FAN
STA
RT/STOP
FEED
BACK
INDICATION
ROBOT
1
ROBOT
2
CONTROL
LER
OUTPUT
INPUT
IN
DICATION
SOLID
ON
=
RUNN
ING
BLINKING=
FAULT
OR
FILTER
CH
ANGE
TU
RN
ON
CONTIN
UOUSLY
TO
RUN
FAN
ROBOT
2
+
-
FB
CR
2
3
4
2
+
-
1(A1)
5(A2)
RU
N
CR
1
3
4
2
1(A1)
5(A2)
NO
(14)
COM
(1
1)
NC
(12)
+
-
FB
CR
2
3
4
2
+
-
1(A1)
5(A2)
RU
N
CR
1
3
4
2
1(A1)
5(A2)
NO
(14)
COM
(1
1)
NC
(12)
+
-
FB
CR
2
3
4
2
+
-
1(A1)
5(A2)
RU
N
CR
1
3
4
2
1(A1)
5(A2)
NO
(14)
COM
(1
1)
NC
(12)
NO
(14)
COM
(1
1)
NC
(12)
NO
(14)
COM
(1
1)
NC
(12)
NO
(14)
COM
(1
1)
NC
(12)
Summary of Contents for Prism 4
Page 31: ...A 23 INSTALLATION d Reclasp filter handles FIGURE A 15 PRISM ...
Page 77: ......