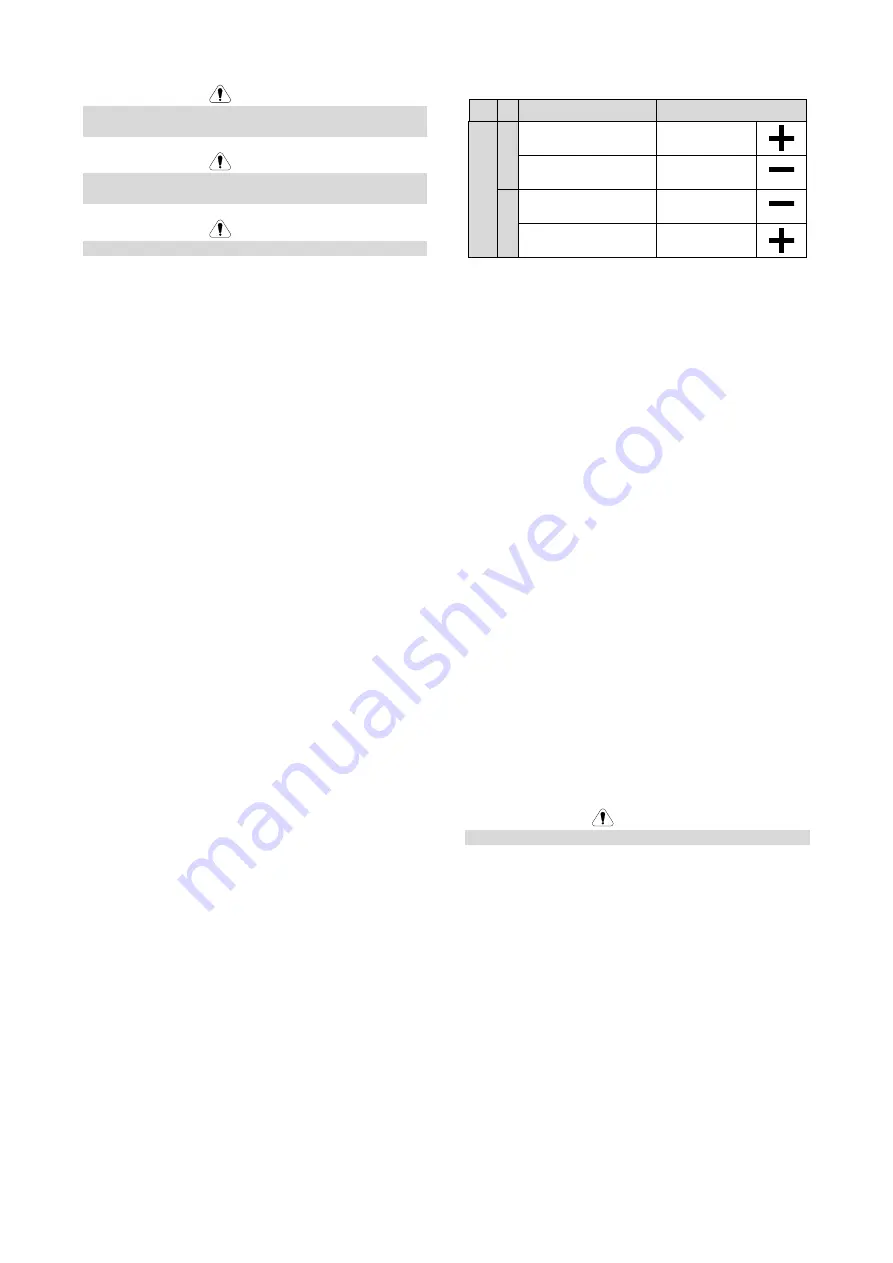
English 26 English
WARNING
The wire drive door and wire spool case have to be
completely closed during welding.
WARNING
Keep the gun cable as straight as possible when welding
or loading electrode through cable.
WARNING
Do not kink or pull cable around sharp corners.
By applying the principle of occupational health and
safety at welding, welding can be begun.
For non-synergic mode can set:
Wire Feed Speed, WFS
The
welding
voltage
Burnback
Time
Run-in
WFS
Preflow Time/ Postflow Time
Spot
Time
2-Step/4-Step
Start
Procedure
Crater
Procedure
Wave
Control:
Pinch
Welding GMAW and FCAW Process in
synergic mode CV
In synergic mode, the welding voltage is not set by user.
The correct welding voltage will set by the machine’s
software.
This value was recalled on the basis of data (input data)
had been loaded:
Wire Feed Speed, WFS.
If it is needed, the welding voltage can be adjusted by
the Right Control [36]. When the Right Control is rotated,
the display will show a positive or negative bar indicates
if the voltage is above or below the ideal voltage.
Additionally can manually set:
Burnback
Run-In
WFS
Preflow Time/ Postflow Time
Spot
Time
2-Step/4-Step
Start
Procedure
Crater
Procedure
Wave
Control:
Pinch
Welding SMAW Process
POWERTEC i380 ADVANCED
does not include the
electrode holder with lead necessary for SMAW welding,
but the one can be purchased separately.
Procedure of begin welding of SMAW process:
First turn the machine off.
Determine the electrode polarity for the electrode to
be used. Consult the electrode data for this
information.
Depending on the polarity of using electrode,
connect the work lead [13] and the electrode holder
with lead to output socket [3] or [4] and lock them.
See the Table 15.
Table 15. Polarity
Output Socket
POLARITY
DC (+)
The electrode holder
with lead to SMAW
[4]
Work lead
[3]
DC (+)
The electrode holder
with lead to SMAW
[3]
Work lead
[4]
Connect the work lead to the welding piece with the
work clamp.
Install the proper electrode in the electrode holder.
Turn the input power ON.
Set the SMAW welding program.
Set the welding parameters.
The welding machine is now ready to weld.
By applying the principle of occupational health and
safety at welding, welding can be begun.
For SMAW program can set:
Welding
current
Switch on / switch off the output voltage on the
output lead
Wave
Controls:
ARC
FORCE
HOT
START
Loading the Electrode Wire
Turn the machine off.
Open the Right panel of the machine.
Unscrew the locking nut of the sleeve.
Load the spool with the wire on the sleeve such that
the spool turns anticlockwise when the wire is fed
into the wire feeder.
Make sure that the spool locating pin goes into the
fitting hole on the spool.
Screw in the fastening cap of the sleeve.
Put on the wire roll using the correct groove
corresponding to the wire diameter.
Free the end of the wire and cut off the bent end
making sure it has no burr.
WARNING
Sharp end of the wire can hurt.
Rotate the wire spool anticlockwise and thread the
end of the wire into the wire feeder as far as the Euro
socket.
Adjust force of pressure roll of the wire feeder
properly.
Adjustments of Brake Torque of Sleeve
To avoid spontaneous unrolling of the welding wire the
sleeve is fitted with a brake.
Adjustment is carried by rotation of its Allen screw M8,
which is placed inside of the sleeve frame after
unscrewing the fastening cap of the sleeve.