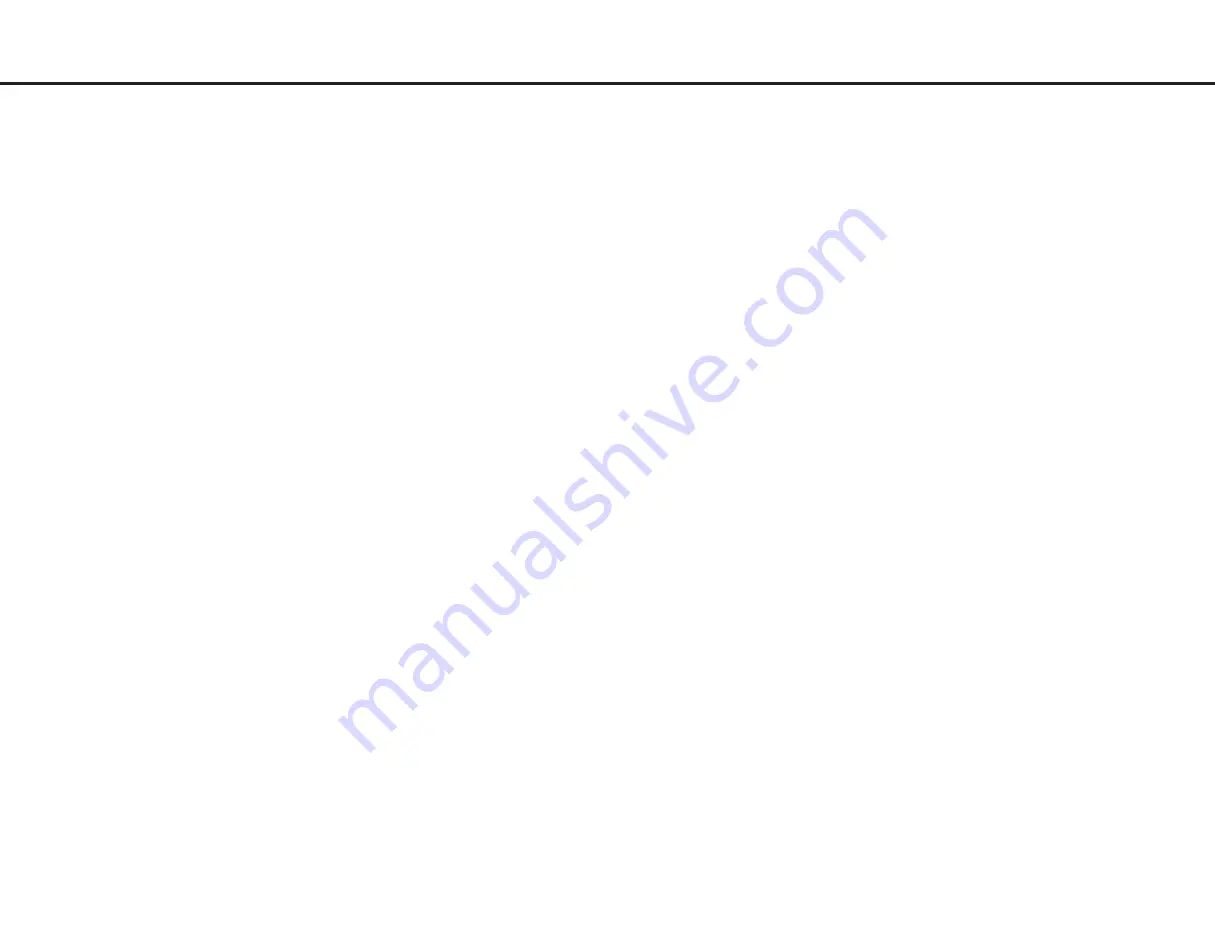
To make spot plug welds, punch 3/16" (5 mm)
holes in the top sheet. Set the Spot Time control to
approximately 1.2 seconds and set the procedure
for the metal thickness to be welded. Install spot
weld nozzle (if available) on gun and press it
against the top sheet so the top and bottom sheets
are tight together. Close trigger and hold it closed
until the arc goes out. If a spot weld nozzle is not
used, smoother welds will result by moving the
welding wire in a small circle during the weld.
D. Burnback
Time
control
provides
manual
adjustment
of
the
burnback
time
(0-250
milliseconds) for any selected welding mode. this
control should be set as low as possible without
the wire "sticking" in the puddle after each weld.
Too long of a burnback time may form a "ball" on
the end of the wire, or may "flash back" to the gun
tip.
E. Run-In Mode is used to adjust the starting wire
feed speed. Starting conditions for certain welding
applications can be improved with adjustment to
the Run-In speed. The control allows for initial
starting speeds from 50 - 150 IPM. After the arc is
started, the set point on the wire feed speed
control will dominate. Note that the Run-in is not
functional with the spool gun. Also note that if Run-
in is set fully counter clockwise to "OFF", Run-in
speed will equal the preset WFS on the machine.
OPERATION