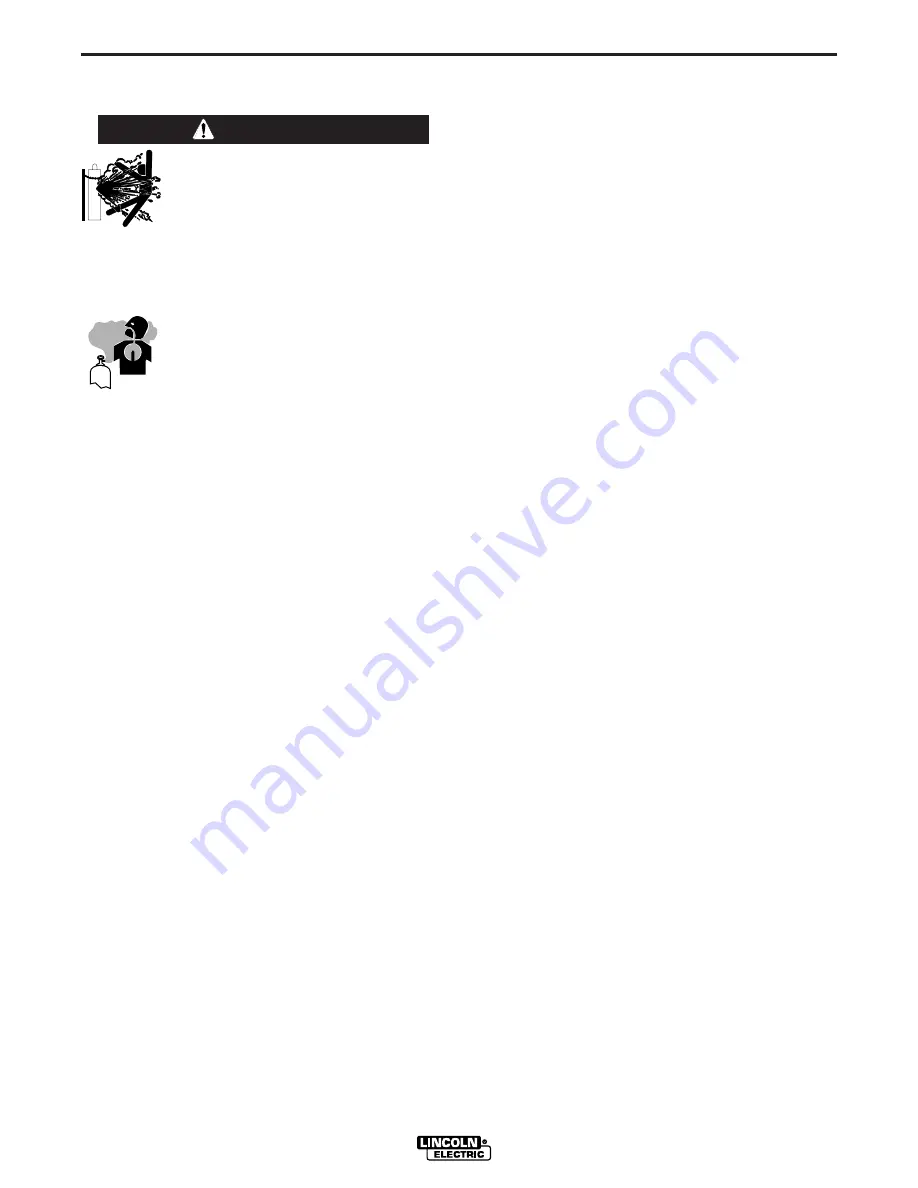
A-13
INSTALLATION
POWER FEED 10
A-13
The upper location must be used for 50-60 lb. Readi-
Reels, Spools and Coils.
For smaller coils (44lb, 30lb, 10lb, etc.), the spindle
can be placed in either the upper or lower location.
The goal is to make the wire path from the coil to the
wire drive an entry into the incoming guide tube that is
as straight as possible. This will optimize wire feeding
performance.
WATER CONNECTIONS (FOR
WATER COOLED GUNS)
If a water cooled gun is to be installed for use with the
Power Drive 10, a K590-5 Water connection kit can be
installed. Contained in the kit are the water lines and
quick connect water line fittings that install in the wire
feed head. Follow the installation instructions includ-
ed in the kit. Water cooled guns can be damaged very
quickly if they are used even momentarily without
water flowing. To protect the gun, we recommended
that a water flow sense kit be installed. This will pre-
vent wire feeding if no water flow is present.
WIRE FEED SHUT DOWN CIRCUIT
(OPTIONAL)
This circuit is intended to be used as a means of stop-
ping wire feeding in the event that the water cooler
(for a water cooled gun) is not turned on. Water
cooled guns can be damaged very quickly if they are
used even momentarily without water flowing. A
Lincoln K1536-1 flow sensor kit is available for this
purpose.
The K1536-1 has two control leads coming from the
unit that become electrically common when water is
flowing. The .25 inch tab terminals of leads 570 and
572, inside the feed head case, are disconnected from
each other. Then the flow sensor control wires are
connected to leads 570 and 572. Refer to the instruc-
tions that come with flow sensor kit for detailed instal-
lation instructions.
GMAW SHIELDING GAS
Customer must provide a cylinder of shielding gas, a
pressure regulator, a flow control valve, and a hose
from the flow valve to the gas inlet fitting of the wire
drive unit.
Connect a supply hose from the gas cylinder flow
valve outlet to the 5/8-18 female inert gas fitting on the
back panel of the wire drive or, if used, on the inlet of
the Gas Guard regulator. (See Below).
Gas Guard Regulator -
The Gas Guard Regulator is
an optional accessory (K659-1) on these models.
Install the 5/8-18 male outlet of the regulator to the
5/8-18 female gas inlet on the back panel of the wire
drive. Secure fitting with flow adjuster key at top.
Attach gas supply to 5/8-18 female inlet of regulator
per instructions above.
WIRE SPINDLE PLACEMENT
The reel stand provides two mounting locations for the
2 inch diameter wire reel spindle to accommodate var-
ious reel sizes. Each mounting location consists of a
tube in the center of the reel stand, and locating slots
on the outside of the reel stand. The bolt, used with a
plain washer and lock washer, slides through the tube
from the side of the reel stand. The bolt should be
threaded into the wire spindle such that the tabs on
the brake mechanism align with the locating slots,
then tighten.
CYLINDER may explode if damaged.
• Keep cylinder upright and chained to
support.
• Keep cylinder away from areas where
it may be damaged.
• Never lift welder with cylinder attached.
• Never allow welding electrode to touch cylinder.
• Keep cylinder away from welding or other live elec-
trical circuits.
BUILDUP OF SHIELDING GAS may
harm health or kill.
•
Shut off shielding gas supply when not
in use.
SEE AMERICAN NATIONAL STANDARD Z-49.1,
“SAFETY IN WELDING AND CUTTING” PUBLISHED
BY THE AMERICAN WELDING SOCIETY.
------------------------------------------------------------------------
WARNING
Summary of Contents for POWER FEED IM584-D
Page 63: ...NOTES POWER FEED 10...
Page 64: ...NOTES POWER FEED 10...
Page 65: ...NOTES POWER FEED 10...