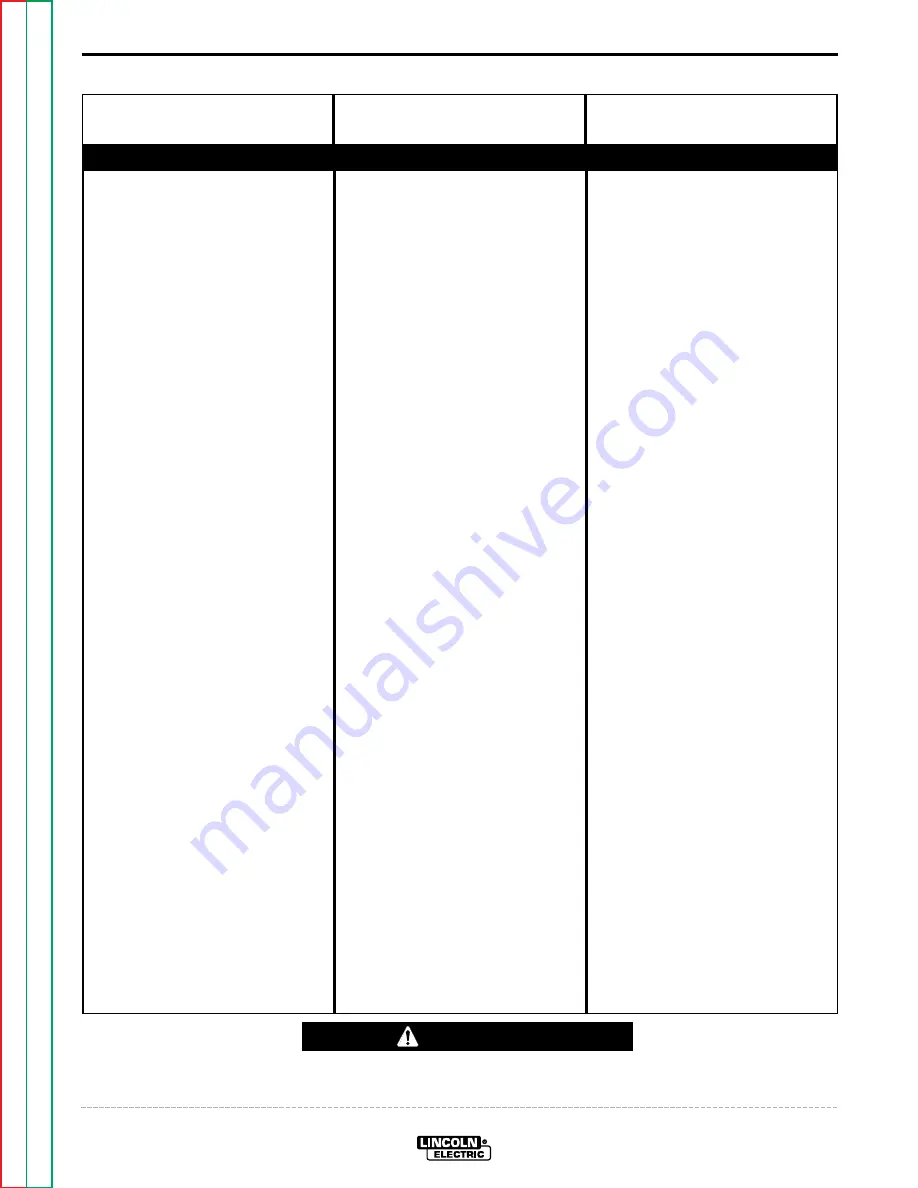
F-21
TROUBLESHOOTING & REPAIR
F-21
NA-5
Observe all Safety Guidelines detailed throughout this manual
If for any reason you do not understand the test procedures or are unable to perform the tests/repairs safely, contact the Lincoln Electric
Service Department for technical troubleshooting assistance before you proceed. Call 216-383-2531 or 1-800-833-9353.
CAUTION
FUNCTION PROBLEMS
PROBLEMS
(SYMPTOMS)
POSSIBLE AREAS OF
MISADJUSTMENTS(S)
RECOMMENDED
COURSE OF ACTION
The start button initiates the wire
feed, but does not activiate the
power source output.
1. Make sure that lead #690 is con-
nected to the proper pin on the
logic board. On newer logic
boards the dip switches must be
in the proper position. See wiring
diagram.
2. Make sure the power source is
capable of producing welding
output voltage. Jumper #2 and
#4 at the power source’s terminal
strip. This should produce open
circuit voltage at the output termi-
nals. If open circuit voltage is not
present the power source may be
faulty.
3. Check or replace the control
cable between the NA-5 and the
power source.
4. With the start button pressed
check light 7K on the logic board
and the “Electrode Hot” light.
Both lights should be on. If the
lights are OFF unplug the burn-
back timer. If the problem is
resolved the burnback timer may
be faulty. Replace.
5. The logic board may be faulty.
1. The CR3 relay may be faulty.
Check or replace.
2. Check the #2 and #4 leads
between the CR3 relay and the
control cable receptacle. See
wiring diagram.
Return to Section TOC
Return to Section TOC
Return to Section TOC
Return to Section TOC
Return to Master TOC
Return to Master TOC
Return to Master TOC
Return to Master TOC