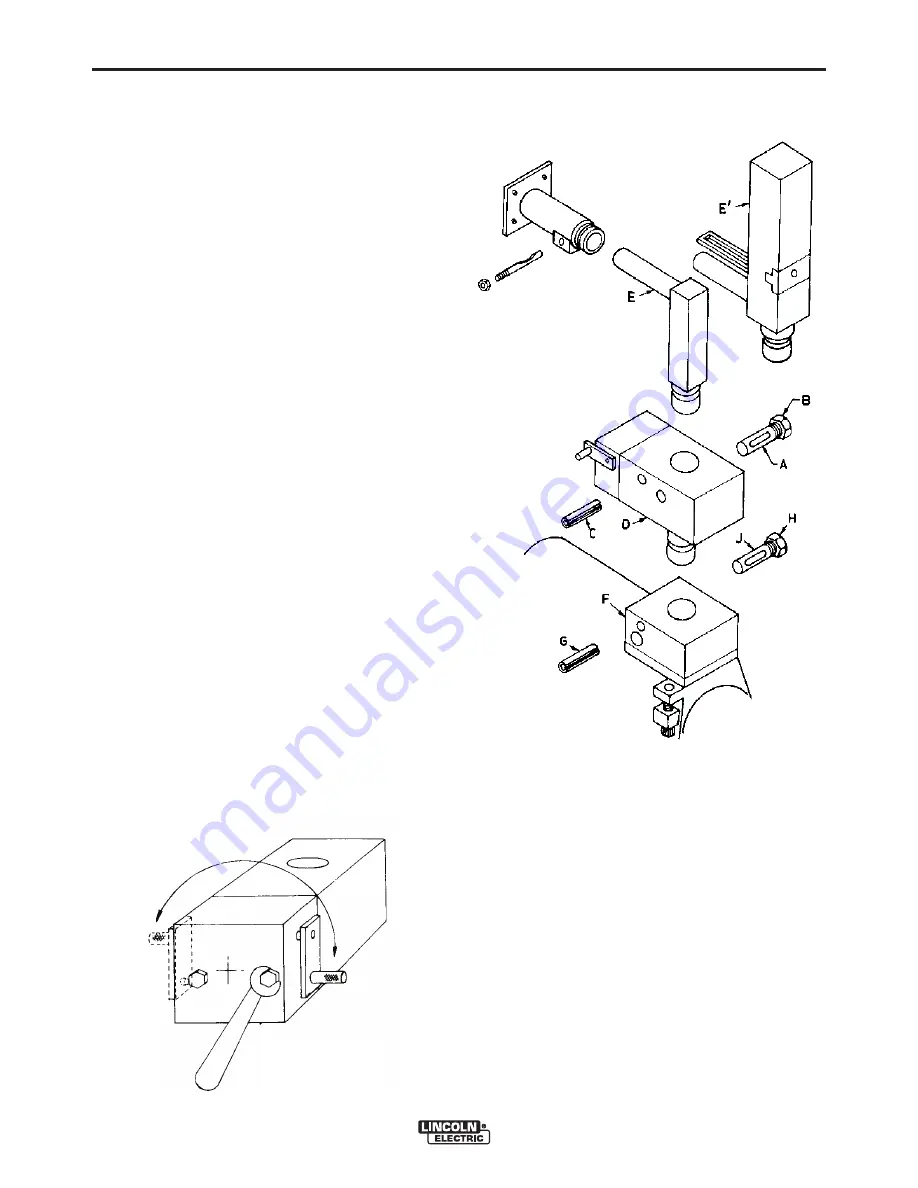
C-10
ACCESSORIES
MAXsa™ 22 & 29 WIRE DRIVES
C-10
K96 HORIZONTAL HEAD ADJUSTER
The K96 provides an easy means of moving the Feed
Head in a horizontal direction by simply turning a
crank handle. It provides 2” (51mm) of travel and can
be mounted directly to the Head Support or to a K29
Vertical Lift Adjuster.
Installation (See Figure C.14)
1. If the Feed Head is already mounted, make sure
that the Lock Nut (H) on the Feed Head Draw Bolt
(J) is tight and drive out the Roll Pin (G) with a
5/16” punch.
2. While supporting the head, loosen the Lock Nut
(H) and remove the Feed Head
NOTE:
If a K29 Vertical Head Adjuster is to be used,
install it now per the instructions provided.
3. With the Draw Bolt (A) in place, fit the K96
Horizontal Adjuster (D) over the shaft of the Head
Support (E) or the K29 (Eʼ ) if used.
4. Drive in the 1/4” Roll Pin that comes with the K96.
5. With the Draw Bolt (J) and the Lock Nut (H) in
place, raise the Feed Head in to position on the
shaft of the Horizontal Adjuster and tighten the
Lock Nut.
6. Drive the 5/16” Roll Pin (G) back in to itʼs original
position.
7. Mount the Crank Handle on whichever side is
most convenient by removing the two bolts and
rotating the housing 180° and replacing the bolts.
See Figure C.15.
FIGURE C.14 - K96
FIGURE C.15
Place Handle in
Either of Two
Positions
Remove Two Bolts
and Rotate Housing