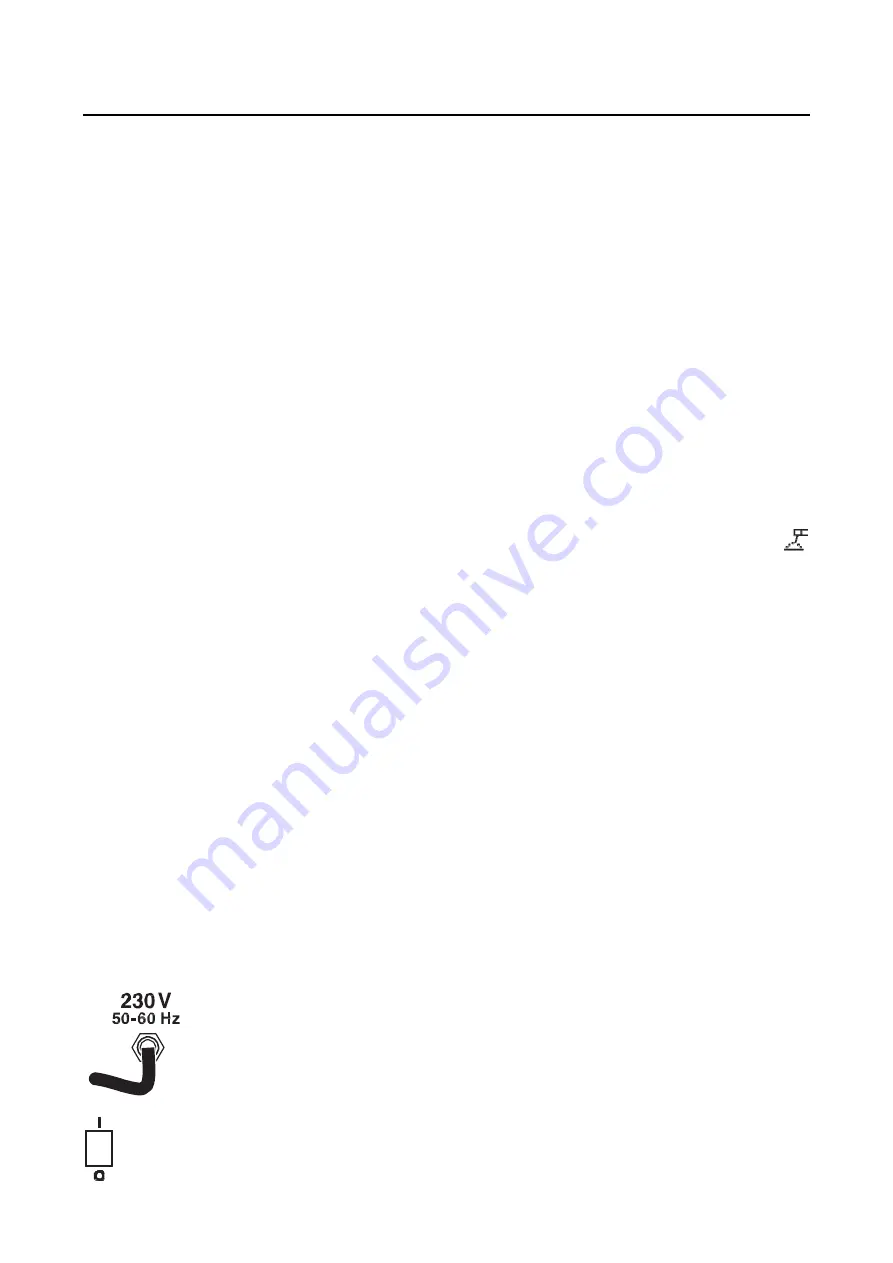
English 5 English
Installation and Operator Instructions
Technical description
Description
The system consists of a modern direct current
generator for the welding of metals, developed via
application of the inverter. This special technology allows
for the construction of compact light weight generators
with high performance. It’s adjust ability, efficiency and
energy consumption make it an excellent work tool
suitable for coated electrode and GTAW (TIG) welding).
Technical data
The machine can be connected to a motor generator of
power meeting the data plate specifications and having
the following characteristics:
Output voltage between 185 and 275 Vac.
Frequency between 50 and 60 Hz.
IMPORTANT: MAKE SURE THE POWER SOURCE
MEETS THE ABOVE REQUISITES. EXCEEDING THE
SPECIFIED VOLTAGE CAN DAMAGE THE WELDING
MACHINE AND INVALIDATE THE WARRANTY.
Duty cycle and overheating
Duty cycle is the percentage of 10 minutes at 40°C
ambient temperature that the unit can weld at its rated
output without overheating. If the unit overheats, the
output stops and the over temperature light comes On.
To correct the situation, wait fifteen minutes for unit to
cool. Reduce amperage, voltage or duty cycle before
starting to weld again (See page III).
Volt - ampere curves
Volt-ampere curves show the maximum voltage and
amperage output capabilities of the welding power
source. Curves of other settings fall under curves shown
(See page III).
Installation
Important: before connecting, preparing or using
equipment, read safety precautions.
Connecting the power source to the mains
electricity supply
SERIOUS DAMAGE TO THE EQUIPMENT MAY
RESULT IF THE POWER SOURCE IS SWITCHED OFF
DURING WELDING OPERATIONS.
Check that the power socket is equipped with the fuse
indicated in the features label on the power source. All
power source models are designed to compensate
power supply variations. For variations of + 15% a
welding current variation of +- 0,2% is created.
BEFORE INSERTING THE MAINS
PLUG, IN ORDER TO AVOID THE
FAIL OF POWER SOURCE, CHECK
IF THE MAINS CORRESPONDS TO
THE WISHED MAIN SUPPLY.
On - off switch
: This switch has two positions:
ON = I and OFF = O.
THIS CLASS A EQUIPMENT IS NOT INTENDED FOR
USE IN RESIDENTIAL LOCATIONS WHERE THE
ELECTRICAL POWER IS PROVIDED BY THE PUBLIC
LOW-VOLTAGE SUPPLY SYSTEM. THERE MAY BE
POTENTIAL DIFFICULTIES IN ENSURING
ELECTROMAGNETIC COMPATIBILITY IN THOSE
LOCATIONS, DUE TO CONDUCTED AS WELL AS
RADIATED DISTURBANCES.
Connection and preparation of equipment for
stick welding
TURN OFF WELDER BEFORE MAKING
CONNECTIONS.
Connect all welding accessories securely to prevent
power loss. Carefully follow safety precautions
described.
Fit the selected electrode to the electrode clamp.
Connect the ground cable quick connection to the
negative (-) receptacle and locate the clamp near the
welding zone.
Connect the electrode cable quick connection to the
positive (+) receptacle.
Use the above connection for straight polarity
welding; for reverse polarity turn the connection.
On the unit preset for coated electrode welding
(Ref.1 - Picture 1 Page 6.).
Adjust welding current with ampere selector (Ref. 3 -
Picture 1 Page 6.).
Turn on the power source.
Connection and preparation of equipment for
gas tungsten arc welding TIG
TURN OFF WELDER BEFORE MAKING
CONNECTIONS.
Connect all welding accessories securely to prevent
power loss. Carefully follow safety precautions
described.
Position the welder in TIG LIFT and TIG HF mode.
Fit the required electrode and nozzle to the electrode
holder (Check the protrusion and state of the
electrode tip).
Connect the ground cable quick connection to the
positive (+) receptacle and the clamp near the
welding zone.
Connect the torch power cable connector to the
negative receptacle (-).
Connect the gas hose to the regulator located on the
gas cylinder.
Regulate the welding mode and the desired
parameters (Section 5.0).
Open the gas valve on the torch.
Connection of relay command.
When relay command is required connect the relay
to the socket on the front panel. In this position
regulation can be fractioned through the power
gauge.
Turn on the power source.