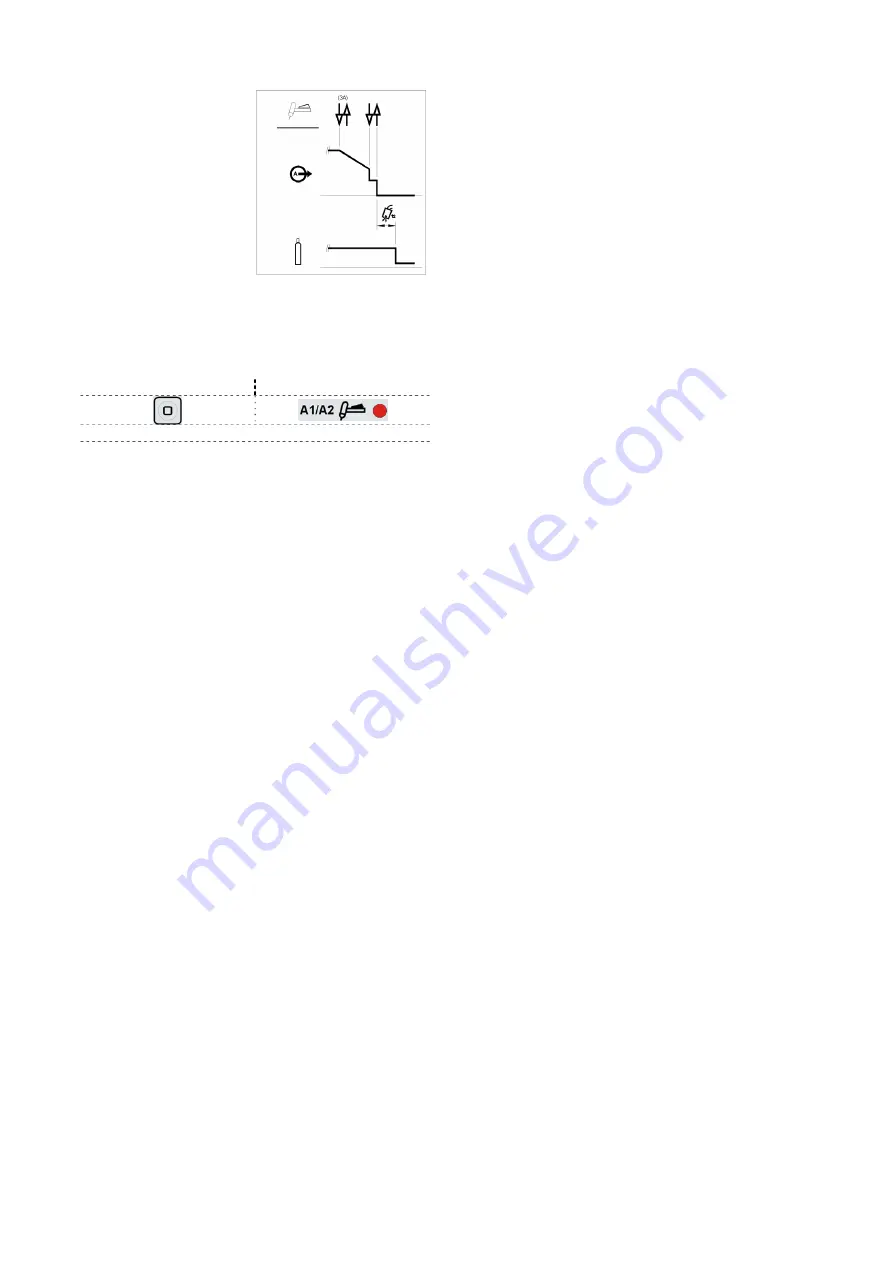
English
English
16
As shown here, again after
the TIG torch trigger is
quickly pressed and
released from step 3A, it is
possible to quickly press
and release the TIG torch
trigger a second time to
end the downslope time
and stop welding.
Bi-Level (A1/A2) Trigger sequence
The Bi-Level feature is selectable only if the “option 20”
is previously enabled in the Setup Menu.
To select Bi-Level sequence:
Action
Visualization
Press several times until the LED above lights up
With this sequence the arc is started as in the 4S
sequence, this means that steps 1 and 2 are the same.
3. Quickly press and release the TIG torch trigger.
The machine will switch the current level from A1 to
A2 (background current). Each time this trigger
action is repeated the current level will switch
between the two levels.
3A. Press and hold the TIG torch trigger when
the main part of the weld is complete. The
machine will now decrease the output current at
a controlled rate, or downslope time, until the
Crater current is reached. This Crater current
can be maintained as long as necessary.
NOTE: The Restart option and the Pulse function are not
available for Bi-Level Trigger sequence.
Torch control functions
Valid only for 220TPX
The torch control functions are available if up/down
module on the torch is assembled on torch and “Option
50” is enabled in the Setup Menu. There are two
functions available:
Option 50 “Cur” change set current value
:
Three operating modes, corresponding to different states
of the machine, are identified:
Before welding: pressing the UP or DOWN key
causes a change of value of the Set current
While welding: pressing the UP or DOWN key
causes a change of value of the Set current during
all phases of welding process except during the start
functions, where the UP/DOWN function is masked.
Pre/post Flow: pressing the UP or DOWN key
causes a change of value of the Set current.
The change will be realized in two ways depending on
pressed button time:
Step
function
Pressing the UP/DOWN button for a minimum time
of 200ms and releasing it, causes the set current
raises/falls of 1A.
Ramp
function
Pressing the UP/DOWN button for a time greaterthan
1 sec., the set current start to increase/decrease with
a (5A/s) ramp. If press for more then 5 ses
increase/decrease with a ramp of (10A/s).
The current ramp will end when the UP/DOWN button
previously pressed is released.
When a remote (pedal or RC-pot) device is present,
depending on welding process selected, the UP/DOWN
behavior is different.
SMAW
:
In SMAW welding mode, the remote device set the
amperage setting in the whole range, bypassing the
main control knob in front User interface. In that case the
signals coming from UP/DOWN
are ignored
.
GTAW
:
In GTAW mode of welding, the remote device set the
percentage of the main set delivered by the machine.
Regulating the main amperage, the UP/DOWN with
remote device will work as described above.
Option 50 “Job” Change memory
:
By pressing torch buttons user will be allowed to change
over settings stored in memory locations from 1 to 9.
The feature is not available during welding.