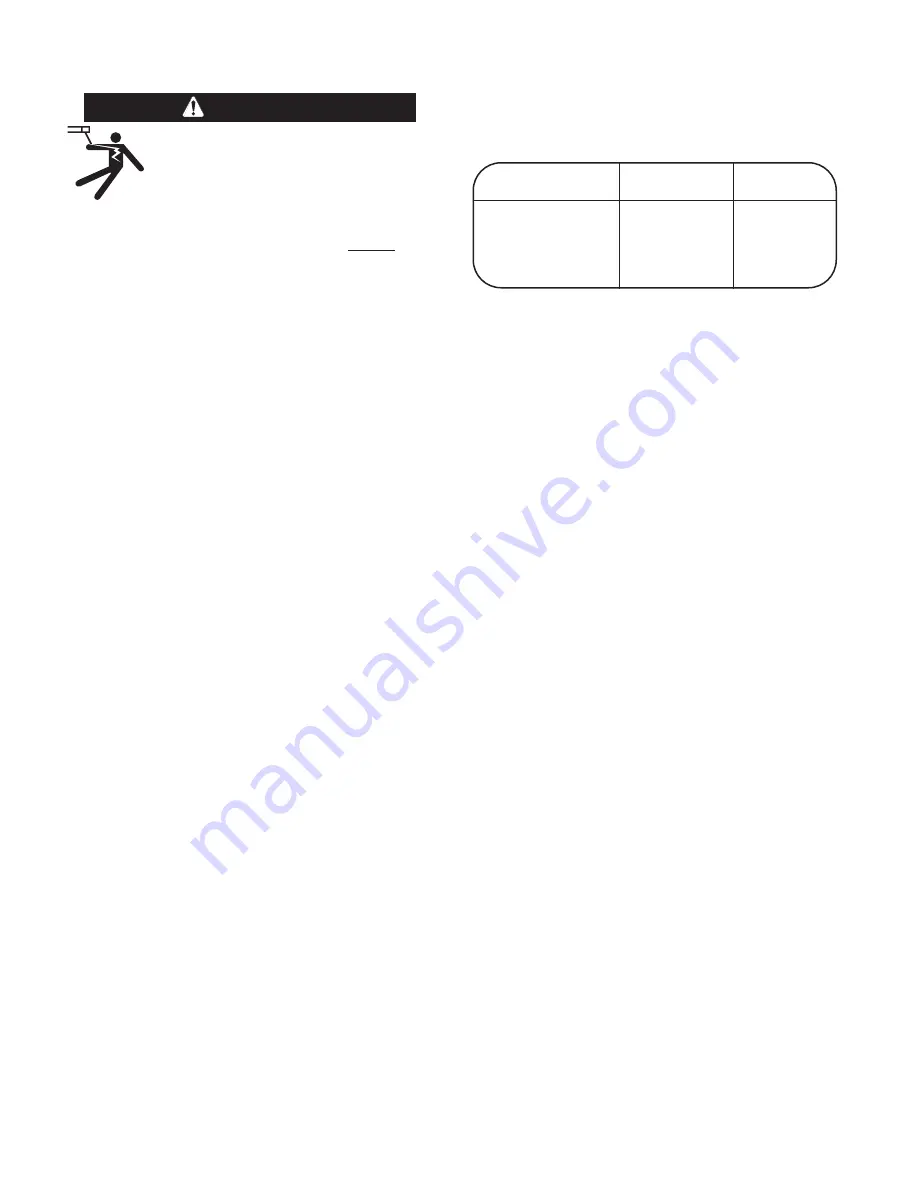
–
19
–
POWER SOURCE OPERATION
Duty Cycle and Time Period
The CV 500-I is rated at the following duty cycles:
Duty Cycle*
Amps
Volts
100%
400
36
60%
450
38
50%
500
40
* Based upon a 10 minute time period. (i.e., for 60%
duty cycle, it is 6 minutes on and 4 minutes off).
Overloading the power source may result in opening
of an internal protective thermostat as indicated by the
amber thermal protection light turning on.
STARTING THE MACHINE
The POWER toggle switch at the extreme right side of
the control panel in the “
I
“ position energizes and
closes the three phase input contactor from a 115 volt
auxiliary transformer. This in turn energizes the main
power transformer.
The machine is de-energized when the POWER
switch is in the “
0
” position.
The white light next to the POWER switch indicates
when the input contactor is energized.
CONTROL SETTINGS & DESCRIPTIONS
OUTPUT VOLTAGE CONTROL DIAL
The Output control dial at the right of the control panel
is a continuous control of the machine output voltage.
The control may be rotated between minimum and
maximum to adjust the machine output, even while
welding.
The machine is equipped with line voltage compensa-
tion as a standard feature. This will hold the output
constant except at maximum output of the machine,
through a fluctuation of ±10% input line voltage.
OPERATING INSTRUCTIONS
Safety Precautions
When using a CV 500-I power source with wire feed-
ers, there will be a small spark if the electrode con-
tacts the work or ground within several seconds after
releasing the trigger.
When used with some wire feeders with the electrical
trigger interlock in the ON position, the arc can restart
if the electrode touches the work or ground during
these several seconds.
ELECTRIC SHOCK
can kill.
• Have an electrician install and service
this equipment.
• Turn the input power off at the fuse
box before working on equipment.
• Do not touch electrically hot parts.
• This next section applies to CV 500-Iʼs without the
Capacitor Discharge Option:
---------------------------------------------------------------------
WARNING