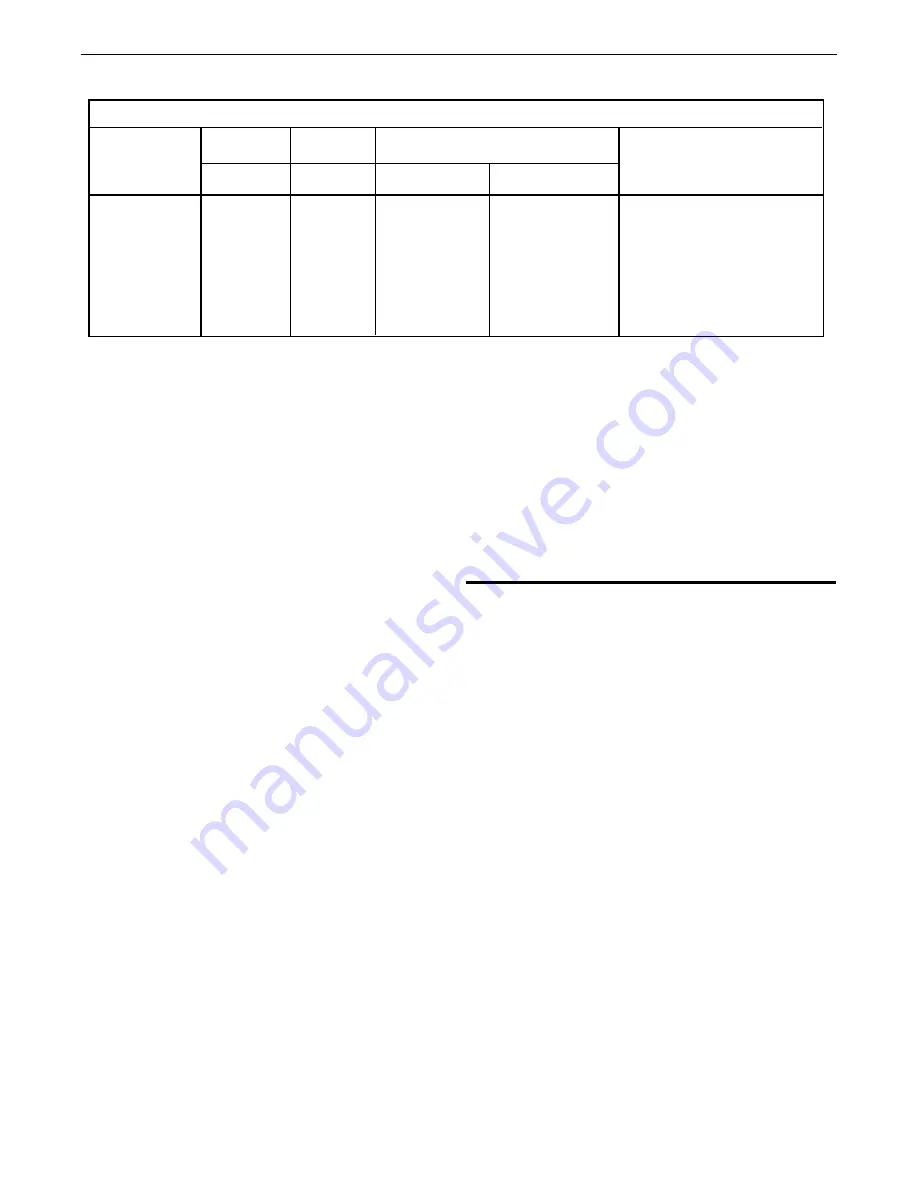
WIRE WELDING-CV
Connect a wire feeder to the Dual Maverick
®
450 according to the
instructions in INSTALLATION INSTRUCTIONS Section.
The Dual Maverick
®
450 in the CV-WIRE mode, permits it to be
used with a broad range of flux cored wire (Innershield and
Outershield) electrodes and solid wires for MIG welding (gas metal
arc welding). Welding can be finely tuned using the PINCH from
–10 (soft) to +10 (crisp) changes the arc from soft and washed-in
to crisp and narrow. It acts as an inductance/pinch control. The
proper setting depends on the procedure and operator preference.
Start with the setting at 0 (OFF).
If the engine bogs while wire welding check that the power
required for the process does not exceed the rated power of the
machine. For unusually high wire feed speeds and low voltage
combinations it may be necessary to disable the variable speed
feature(see “SET-UP” section) and set the ignition switch to high
idle.
ARC GOUGING
Dual Maverick® 450 can be used for Arc Gouging with carbons up
to 3/8”(10mm) in diameter.
Use the selector knob to adjust output current to the desired level
for the gouging electrode being used.
The ARC FORCE is not active in the ARC GOUGING Mode. The ARC
FORCE is automatically set to maximum when the ARC GOUGING
mode is selected which provides the best ARC GOUGING
performance.
PARALLELING
When paralleling machines in order to combine their outputs, all
units must be operated in the CC-STICK mode only at the same
output settings. Use the selector knob to choose stick mode from
the home screen. Operation in other modes may produce erratic
outputs, and large output imbalances between the units.
B-6
OPERATION
DUAL MAVERICK
®
450
B-6
TYPICAL CURRENT RANGES
(1)
FOR TUNGSTEN ELECTRODES
(2)
Tungsten Electrode DCEN (-) DCEP (+) Approximate Argon Gas Flow
TIG TORCH
Diameter in. (mm)
Flow Rate C.F.H. ( l /min.)
Nozzle Size (4), (5)
1%, 2% Thoriated 1%, 2% Thoriated Aluminum
Stainless Steel
Tungsten
Tungsten
.010 (.25) 2-15
(3)
3-8
(2-4)
3-8
(2-4)
#4, #5, #6
0.020
(.50) 5-20
(3)
5-10
(3-5)
5-10
(3-5)
0.040
(1.0) 15-80
(3)
5-10
(3-5)
5-10
(3-5)
1/16
(1.6) 70-150
10-20
5-10
(3-5)
9-13
(4-6)
#5, #6
3/32
(2.4) 150-250
15-30
13-17 (6-8)
11-15
(5-7)
#6, #7, #8
1/8
(3.2)
250-400
25-40
15-23 (7-11)
11-15
(5-7)
5/32
(4.0) 400-500
40-55
21-25
(10-12)
13-17
(6-8)
#8, #10
(1) When used with argon gas. The current ranges shown must be reduced when using argon/helium or pure helium shielding gases.
(2) Tungsten electrodes are classified as follows by the American Welding Society (AWS):
Pure
EWP
1% Thoriated
EWTh-1
2% Thoriated
EWTh-2
Though not yet recognized by the AWS, Ceriated Tungsten is now widely accepted as a substitute for 2% Thoriated Tungsten in AC and DC applications.
(3) DCEP is not commonly used in these sizes.
(4) TIG torch nozzle "sizes" are in multiples of 1/16ths of an inch:
# 4 = 1/4 in.
(6 mm)
# 5 = 5/16 in.
(8 mm)
# 6 = 3/8 in.
(10 mm)
# 7 = 7/16 in.
(11 mm)
# 8 = 1/2 in.
(12.5 mm)
#10 = 5/8 in.
(16 mm)
(5) TIG torch nozzles are typically made from alumina ceramic. Special applications may require lava nozzles, which are less prone to breakage, but cannot withstand high temperatures
and high duty cycles.
TABLE B.3