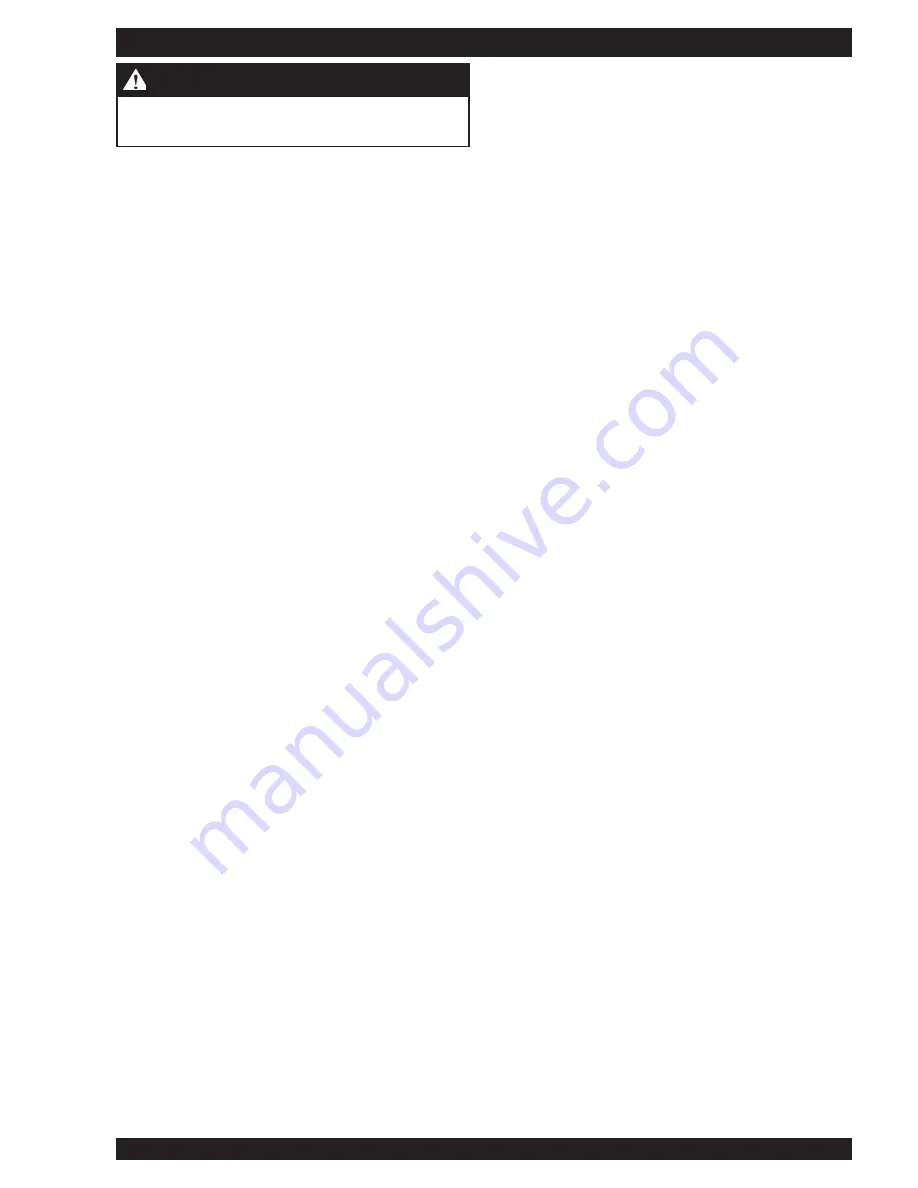
IMA 574B
CV320-I
Page 5
INSTRUCTIONS FOR ELECTROMAGNETIC COMPATIBILITY
Conformance
Products displaying the C-Tick mark are in conformity with
Australian/New Zealand requirements for the Electromagnetic
Compatibility (EMC). They are:
•
manufactured in conformity with Australian/New Zealand
Standard (Emission):- AS/NZS 3652 ‘Electromagnetic
Compatibility - Arc Welding Equipment’ (identical to and
reproduced from, British Standard EN 50199).
•
for using with other Lincoln Electric/LiquidArc equipment.
•
designed for industrial and professional use.
Introduction
All electrical equipment generates small amounts of
electromagnetic emission. Electrical emission may be transmitted
through power lines or radiated through space, similar to a radio
transmitter. When emissions are received by other equipment,
electrical interference may result. Electrical emissions may effect
many kinds of electrical equipment; other near by welding
equipment, radio and TV reception, numerical controlled
machines, telephone systems, computers, etc. Be aware that
interference may result and extra precautions may be required
when a welding power source is used in a domestic
establishment.
Installation and Use
The purchaser/user is responsible for installing and using the
welding equipment according to the manufacturer’s instructions. If
electromagnetic disturbances are detected then it shall be the
responsibility of the purchaser/user of the welding equipment to
resolve the situation with the technical assistance of the
manufacturer. In some cases this remedial action may be as
simple as earthing (grounding) the welding circuit (see note
below). In other cases it could involve constructing an
electromagnetic screen enclosing the power source and the work
complete with associated input filters. In all cases electromagnetic
disturbances must be reduced to the point where they are no
longer troublesome.
NOTE: The welding circuit may or may not be earthed for safety
reasons according to national codes. Changing the earthing
arrangements should only be authorised by a person who is
competent to assess whether the changes increase the risk of
injury, eg. by allowing parallel welding current return paths which
may damage the earth circuits of other equipment.
Assessment of Area
Before installing welding equipment the purchaser/user shall make
an assessment of potential problems in the surrounding area.
The following shall be taken into account:
a.
Other supply cables, control cables, signalling and telephone
cables; above, below and adjacent to the welding equipment;
b.
Radio and television transmitters and receivers;
c.
Computer and other control equipment;
d.
Safety critical safety equipment, eg. guarding of industrial
equipment;
e.
The health of people around, eg. the use of pacemakers and
hearing aids;;
f.
Equipment used for calibration or measurement;
g.
The immunity of other equipment in the environment. The
purchaser/user shall ensure that other equipment being used
in the environment is compatible. This may require additional
protection measures;
h.
The time of the day that welding or other activities are to be
carried out.
The size of the surrounding area to be considered will depend on the
structure of the building and other activities that are taking place. The
surrounding area may extend beyond the boundaries of the premises.
Methods of Reducing Emissions
Mains Supply
Welding equipment should be connected to the mains supply
according to the manufacturers recommendations.If interference
occurs, it may be necessary to take additional precautions such as
filtering the mains supply. Consideration should be given to
shielding the supply cable of permanently installed welding
equipment, in metallic conduit or equivalent. Shielding should be
electrically continuous throughout its length. The shielding should
be connected to the welding power source so that good electrical
contact is maintained between the conduit and the welding power
source enclosure.
Maintenance of the Welding Equipment
The welding equipment should be routinely maintained according
to the manufacturer’s recommendations. All access and service
doors and covers should be closed and properly fastened when
the welding equipment is in operation. The welding equipment
should not be modified in any way except for those changes and
adjustments covered in the manufacturers instructions. In
particular, the spark gaps of arc initiation and stabilising devices
should be adjusted and maintained according to the
manufacturer’s recommendations.
Welding Cables
The welding cables should be kept as short as possible and
should be positioned close together, running at or close to the
floor level.
Equipotential Bonding
Bonding of all metallic components in the welding installation and
adjacent to it should be considered. However, metallic
components bonded to the work piece will increase the risk that
the operator could receive a shock by touching these metallic
components and the electrode at the same time. The operator
should be insulated from all such bonded metallic components.
Earthing of the Workpiece
Where the workpiece is not bonded to earth for electrical safety,
nor connected to earth because of its size and position, eg. ship’s
hull or building steelwork, a connection bonding the workpiece to
earth may reduce emissions in some, but not all instances. Care
should be taken to prevent the earthing of work pieces increasing
the risk of injury to users, or damage to other electrical
equipment. Where necessary, the connection to the workpiece to
earth should be made by direct connection to the workpiece, but in
some countries where direct connection is not permitted, the
bonding should be achieved by suitable capacitance, selected
according to national regulations.
Screening and Shielding
Selective screening and shielding of other cables and equipment
in the surrounding area may alleviate problems of interference.
Screening of the entire welding installation may be considered for
special applications.*
*
Portions of the preceding text are contained in AS./NZS3652:
‘Electromagnetic Compatibility - Arc Welding Equipment’.
This welding machine must be used by trained operators
only. Read this manual carefully before attempting to use
the welding machine.
WARNING