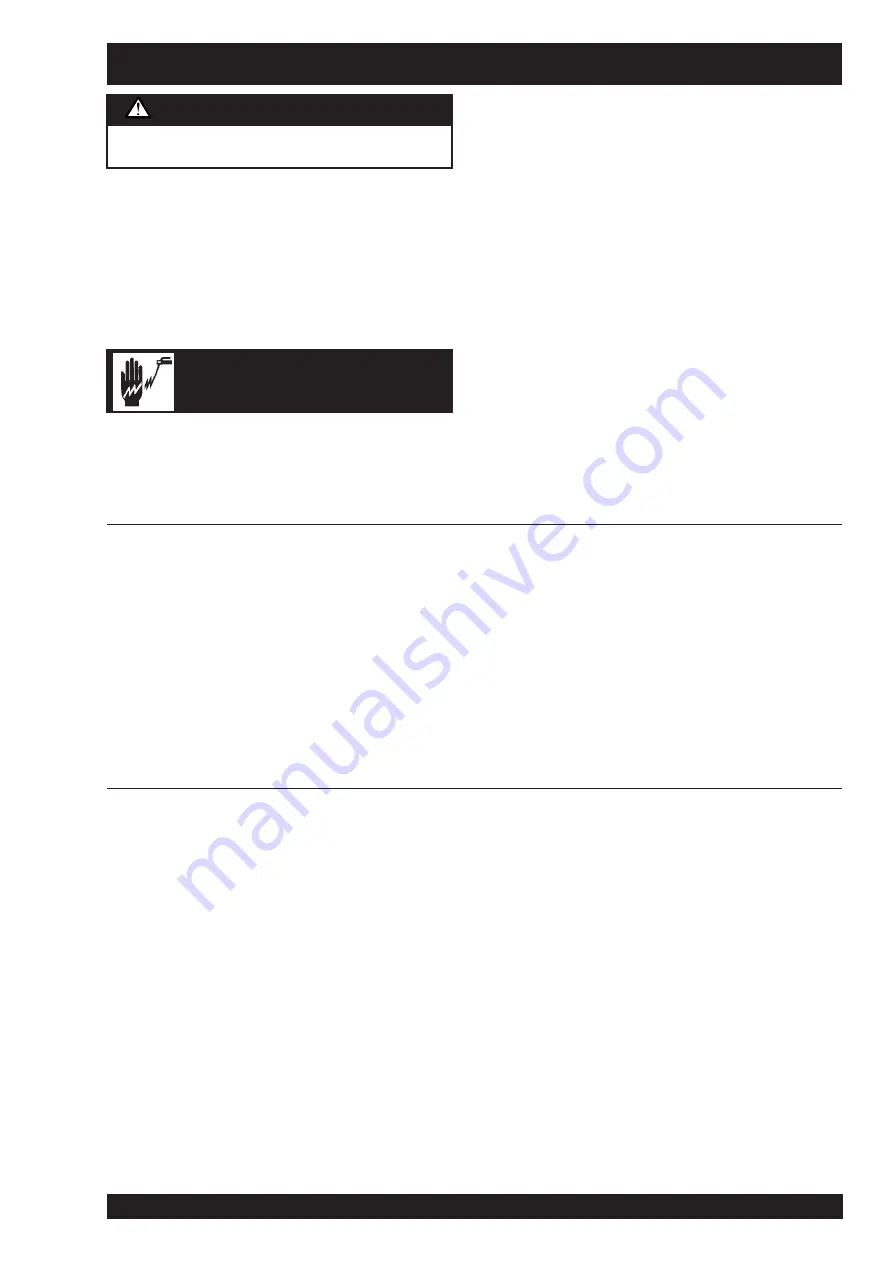
IMA 566BLA
Maxmig 330R
Page 11
GROUND TEST PROCEDURE
Note: This procedure is for ‘machines as built’ many modifications
could have taken place over the life of a particular machine, so
details of this procedure may need to be ‘adjusted’ to suit these
modifications.
For prompt service contact your local authorised LiquidArc Field
Service Shop.
The insulation resistance values listed below are from Australian
Standard AS1966.1
If any problems are encountered refer to your nearest authorised
LiquidArc Field Service Shop.
1.
Disconnect input cable from power supply.
2.
Disconnect gun assembly and work cable.
3.
Remove RHS side panel from power source and LHS from
traveller (if applicable).
4.
Jumper the three (3) AC terminals and the (+)ve and (-)ve
terminal of the bridge rectifier, (a total of five (5) places).
5.
Disconnect the PCB plug and insert a 20 way shorting plug
into the harness.
6.
Switch the ‘fine’ control rotary switch to position ‘one’ (1)
and switch the ‘coarse’ control toggle switch to position
one(1).
7.
Primary Test: Connect one lead of the mega tester to the
frame of the machine and the other lead to the Active
terminal of the input plug. Apply the test (Min. resistance
1M
Ω
)
8.
Welding Circuit Test: Connect one lead of the mega tester
to the frame of the machine and the other lead to the (+)ve
output plug. Apply the test. (Min. resistance 1M
Ω
)
9.
Welding Circuit to Primary Test: Connect one lead of the
mega tester to the (+)ve output stud and the other lead to
the Active terminal of the input lug. Apply the test. (Min.
resistance 10M
Ω
)
10.
Transformer Thermostat Test: Connect one lead of the
mega to the frame of the machine and the other lead to
lead No. 42 (transformer thermostat). Apply the test. (Min.
resistance 1M
Ω
)
11.
Remove all jumpers and reconnect all leads and plugs.
12.
Refit all the panel work previously removed.
Procedure for Replacing PC Boards
Before replacing a PC board suspected of being defective,
visually inspect the PC board in question for any visible damage
to any of its components and conductors on the back of the board.
1.
If there is no visible damage to the PC board, install a new
one and see if this remedies the problem. If the problem is
remedied, reinstall the original PC board to see if the
problem still exists. If the problem no longer exists with the
old PC board:
a. Check the PC board harness connector pins for
corrosion, contamination, or looseness.
b. Check leads in the plug harness for loose or intermittent
connection.
2.
If PC board is visibly damaged, before possibly subjecting
the new PC board to the same cause of failure, check for
possible shorts, opens or grounds caused by:
a. Damaged lead insulation.
b. Poor lead termination, such as a poor contact or a short
to adjacent connection or surface.
c. Shorted or open motor leads, or other external leads.
d. Foreign matter or interference behind the PC board.
3.
If PC board is visibly damaged, inspect for cause, then
remedy before installing a replacement PC board.
ELECTRIC SHOCK CAN KILL
This procedure is only suitable for applications using DC
mega testers up to 500V.
WARNING
Changing Settings for Wire Burnback and
Motor Acceleration
If Electrode Wire Burnback or Motor Acceleration need to be
altered from factory settings, because of the welding procedure
being used, locate the PCB in the power source or in the traveller.
On the PCB there is a trimmer labelled ‘R.T.S.’, this trimmer
controls the wire burnback time. It adjusts a time period from
when the drive motor stops until the power source and gas
solenoid are switched off. [Approximately 0.1 seconds (when fully
counter-clockwise) to approximately 1.1 seconds (when fully
clockwise)]. Factory setting is mid-position.
Another trimmer on the PCB is labelled ‘Rampa’, this trimmer
controls the acceleration rate of the drive motor from stationary to
the set wire feed speed. Maximum acceleration when fully
counter-clockwise to minimum acceleration when fully clockwise.
This is particularly important when welding aluminium wire. The
factory setting is fully clockwise.