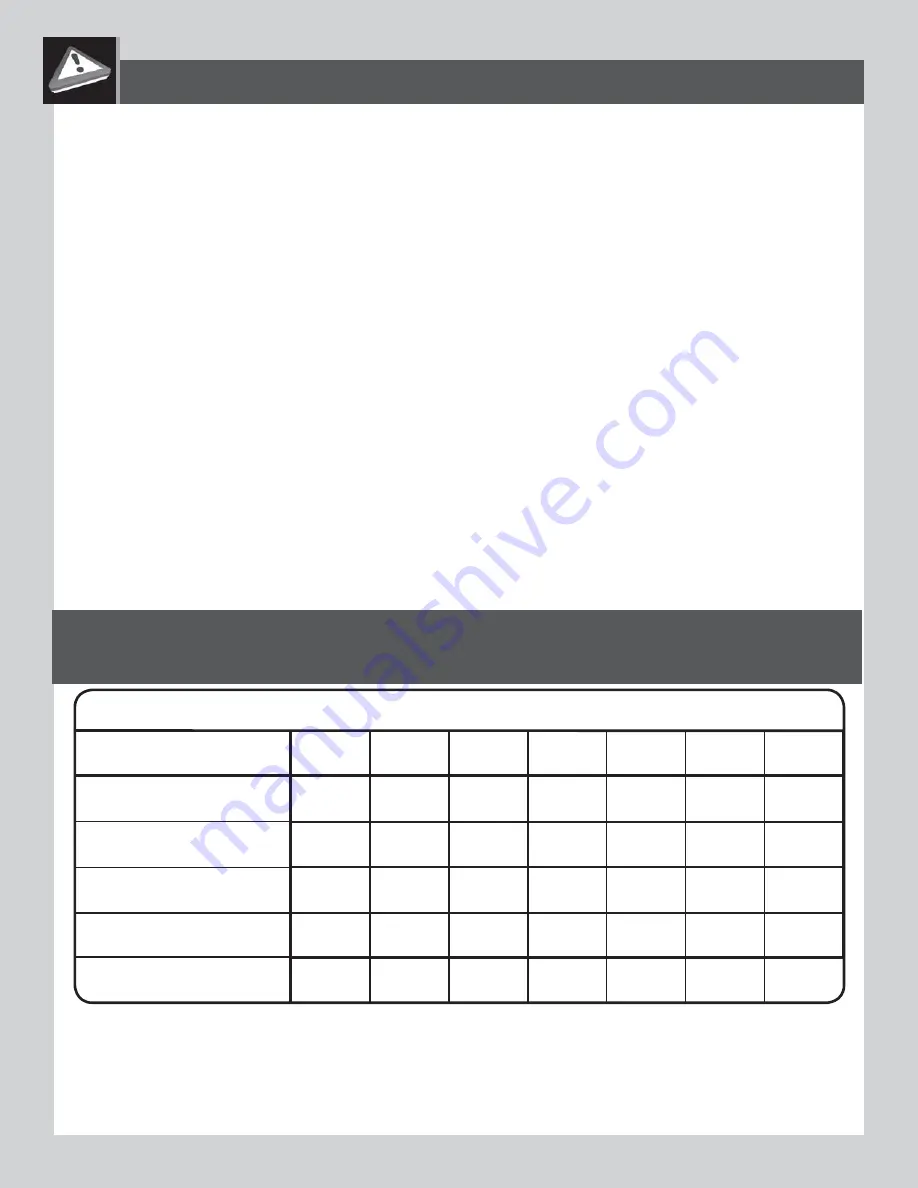
7
CONSUMER INFORMATION SHEET FOR PLAYGROUND SURFACING MATERIALS*
**The maximum fall height for this product is 37 in (94 cm).
We recommend using 6 in (15 cm) of Double Shredded Bark Mulch.**
5 ft
6 ft
7 ft
9 ft
10 ft
11 ft
12 ft
--
6 in
--
--
9 in
12 in
--
--
6 in
9 in
--
--
--
12 in
6 in
--
9 in
12 in
--
--
--
--
6 in
9 in
--
12 in
--
--
--
--
--
--
6 in
--
--
TABLE 1 — Depth of Surfacing Material Required Based on Fall Heights
Material / Fall Height
Double Shredded Bark
Mulch
Wood Chips
Fine Sand
Fine Gravel
Shredded Tires***
(152 cm)
(183 cm)
(213 cm)
(274 cm)
(305 cm)
(335 cm)
(366 cm)
(15 cm)
(23 cm)
(30 cm)
(15 cm)
(23 cm)
(30 cm)
(30 cm)
(23 cm)
(15 cm)
(15 cm)
(23 cm)
(30 cm)
(15 cm)
Select Protective Surfacing—One of the most important things you can
do to reduce the likelihood of serious head injuries is to install shock-
absorbing protective surfacing under and around your play equipment.
The protective surfacing should be applied to a depth that is suitable for
the equipment height in accordance with ASTM Specifi cation F1292.
There are different types of surfacing to choose from; whichever product
you select, follow these guidelines:
Loose-Fill Materials—Maintain a minimum depth of 9 inches of loosefi ll
materials such as wood mulch/chips, engineered wood fi ber (EWF), or
shredded/recycled rubber mulch for equipment up to 8 feet high; and
9 inches of sand or pea gravel for equipment up to 5 feet high. NOTE:
An initial fi ll level of 12 inches will compress to about a 9-inch depth
of surfacing over time. The surfacing will also compact, displace, and
settle, and should be periodically refi lled to maintain at least a 9-inch
depth.
Use a minimum of 6 inches of protective surfacing for play equipment
less than 4 feet in height. If maintained properly, this should be
adequate. (At depths less than 6 inches, the protective material is too
easily displaced or compacted.)
NOTE: Do not install home playground equipment over
concrete, asphalt, or any other hard surface. A fall onto a hard surface
can result in serious injury to the equipment user. Grass and dirt are not
considered protective surfacing because wear and environmental factors
can reduce their shock absorbing effectiveness. Carpeting and thin mats
are generally not adequate protective surfacing. Ground level equipment
– such as a sandbox, activity wall, playhouse or other equipment that has
no elevated play surface – does not need any protective surfacing.
Use containment, such as digging out around the perimeter and/or lining
the perimeter with landscape edging. Don’t forget to account for water
drainage.
Check and maintain the depth of the loose-fi ll surfacing material. To
maintain the right amount of loose-fi ll materials, mark the correct level
on play equipment support posts. That way you can easily see when to
replenish and/or redistribute the surfacing.
Do not install loose fi ll surfacing over hard surfaces such as concrete or
asphalt.
Poured-In-Place Surfaces or Pre-Manufactured
Rubber Tiles—You may be interested in using surfacing other than loose-
fi ll materials – like rubber tiles or poured-in-place surfaces.
Installations of these surfaces generally require a professional and are
not “do-it-yourself” projects.
Review surface specifi cations before purchasing this type of surfacing.
Ask the installer/manufacturer for a report showing that the product has
been tested to the following safety standard: ASTM F1292 Standard
Specifi cation for Impact Attenuation of Surfacing Materials within the
Use Zone of Playground Equipment. This report should show the specifi c
height for which the surface is intended to protect against serious head
injury. This height should be equal to or greater than the fall height –
vertical distance between a designated play surface (elevated surface
for standing, sitting, or climbing) and the protective surfacing below – of
your play equipment.
Check the protective surfacing frequently for wear.
Placements—Proper placement and maintenance of protective surfacing
is essential. Be sure to:
Extend surfacing at least 6.6 feet (2 m) from the equipment in all
directions.
For to-fro swings, extend protective surfacing in front of and behind the
swing to a distance equal to twice the height of the top bar from which
the swing is suspended.
For tire swings, extend surfacing in a circle whose radius is equal to
the height of the suspending chain or rope, plus 6.6 feet (2 m) in all
directions.
*This information has been extracted from the CPSC publications “PlaygroundSurfacing—Technical Information Guide” and “Hand-
book for Public Playground Safety.”
***This data is from tests conducted by independent testing laboratories on a 6-inch depth of uncompressed shredded tire samples
produced by four manufacturers. It is recommended that persons seeking to install shredded tires as a protective surface request test
data from the supplier showing the critical height of the material when it was tested in accordance with ASTM F1292.