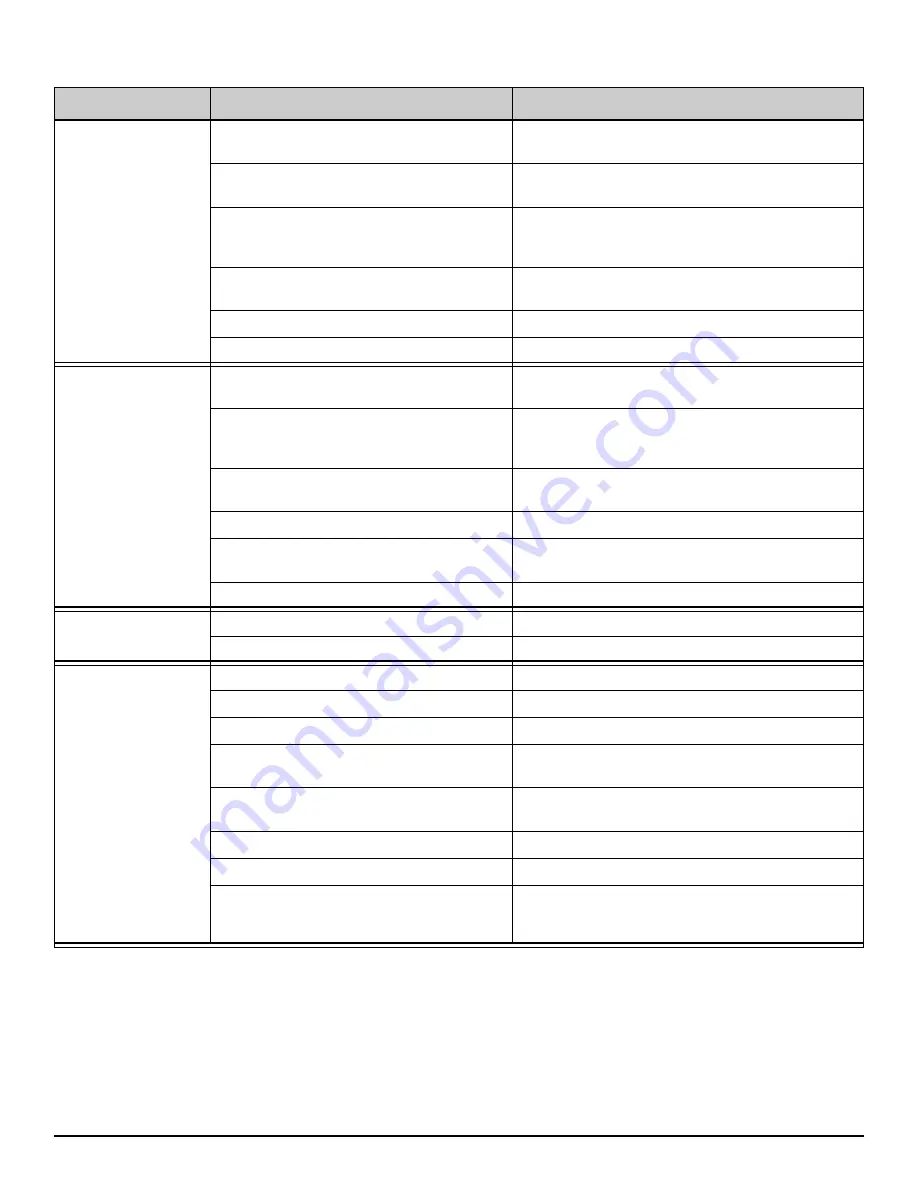
6850000C
Copyright © Liberty Pumps, Inc. 2020 All rights reserved.
11 | EN
Pump does not deliver
proper capacity.
Discharge valve(s) partially closed or clogged.
Check the discharge line for foreign material, including
ice if the discharge line passes through or into cold areas.
Check valve partially clogged.
Raise liquid level up and down to clear; remove check
valve to remove obstruction.
Incorrect motor rotation.
1-Phase: Contact factory.
3-Phase: Correct 3-phase pump rotation direction. Refer
to section
3-Phase Pump Rotation Verification
.
Total head (lift height) is beyond pump's
capability.
Route discharge piping to a lower level. If not possible, a
larger pump may be required. Consult Liberty Pumps.
Low liquid level.
Check liquid level.
Obstruction in pump or piping.
Remove obstruction.
Pump operates noisily.
Piping attachments to building are too rigid.
Replace a portion of the discharge line with rubber hose
or connector.
Incorrect motor rotation.
1-Phase: Contact factory.
3-Phase: Correct 3-phase pump rotation direction. Refer
to section
3-Phase Pump Rotation Verification
.
Pump is being run below minimum head
requirement causing cavitation.
A different sized pump or impeller may be required.
Consult Liberty Pumps.
Foreign objects in the impeller cavity.
Clean the impeller cavity.
Broken impeller.
Consult Liberty Pumps for information regarding impeller
replacement.
Worn bearings.
Return pump to an authorized repair facility.
Seal fail light is
illuminated.
Lower (outer) seal has been compromised.
Replace lower seal.
Control panel relay sensitivity is incorrect.
Adjust sensitivity dial.
Repeated tripping.
Circuit protection underrated.
Check rating and replace with proper size.
Current unbalance.
Check current draw.
Other appliance on same circuit.
Pump requires separate circuit.
Pump is connected to an extension cord or
wiring is inadequate or compromised.
Have an electrician check for proper wiring.
Improper voltage.
Have an electrician check all wiring for proper
connections and adequate voltage and capacity.
Obstruction in pump.
Remove obstruction.
Foreign matter build-up.
Clean motor housing.
Incorrect motor rotation.
1-Phase: Contact factory.
3-Phase: Correct 3-phase pump rotation direction. Refer
to section
3-Phase Pump Rotation Verification
.
Table 2. Troubleshooting Matrix (continued)
Problem
Possible Cause
Corrective Action