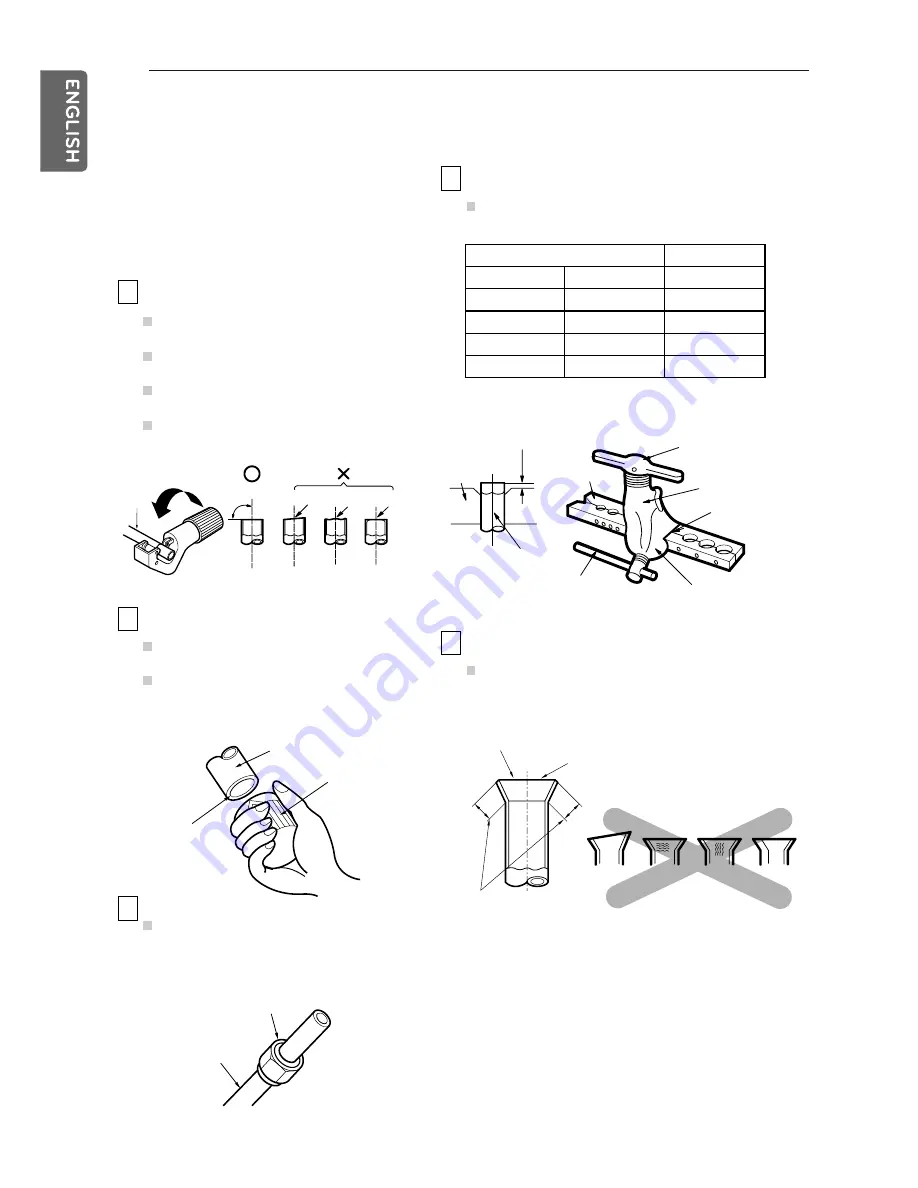
FLARING WORK AND CONNECTION OF PIPING
A
Use the piping kit accessory or the pipes
purchased locally.
Measure the distance between the indoor
and the outdoor unit.
Cut the pipes a little longer than measured
distance.
Cut the cable 1.5m longer than the pipe
length.
D
Carry out flaring work using flaring tool as shown
below.
Outside diameter
mm
ø6.35
ø9.52
ø12.7
ø15.88
inch
1/4
3/8
1/2
5/8
mm
0~0.5
0~0.5
0~0.5
0~1.0
A
Firmly hold copper pipe in a die in the
dimension shown in the table above.
B
Completely remove all burrs from the cut
cross section of pipe/tube.
Put the end of the copper tube/pipe in a
downward direction as you remove burrs in
order to avoid dropping burrs into the tubing.
E
Compare the flared work with figure below.
If flare is noted to be defective, cut off the flared
section and do flaring work again.
C
Remove flare nuts attached to indoor and
outdoor unit, then put them on pipe/tube
having completed burr removal.
(not possible to put them on after flaring
work)
Copper
pipe
90°
Slanted Uneven Rough
Pipe
Reamer
Point down
Flare nut
Copper tube
Bar
Copper pipe
Clamp handle
Red arrow mark
Cone
Yoke
Handle
Bar
"A
"
Inclined
Inside is shiny without scratches.
Smooth all round
Even length
all round
Surface
damaged
Cracked Uneven
thickness
= Improper flaring =
Main cause for gas leakage is due to defect
in flaring work. Carry out correct flaring work
in the following procedure.
Flaring work
Flaring work
Burrs removal
Check
Cut the pipes and the cable
Putting nut on
INSTALLATION
10
Summary of Contents for MFL39754838
Page 2: ... Recommended 24 C is suitable for human body Refer page no 21 and 22 owner s manual ...
Page 3: ......
Page 4: ......