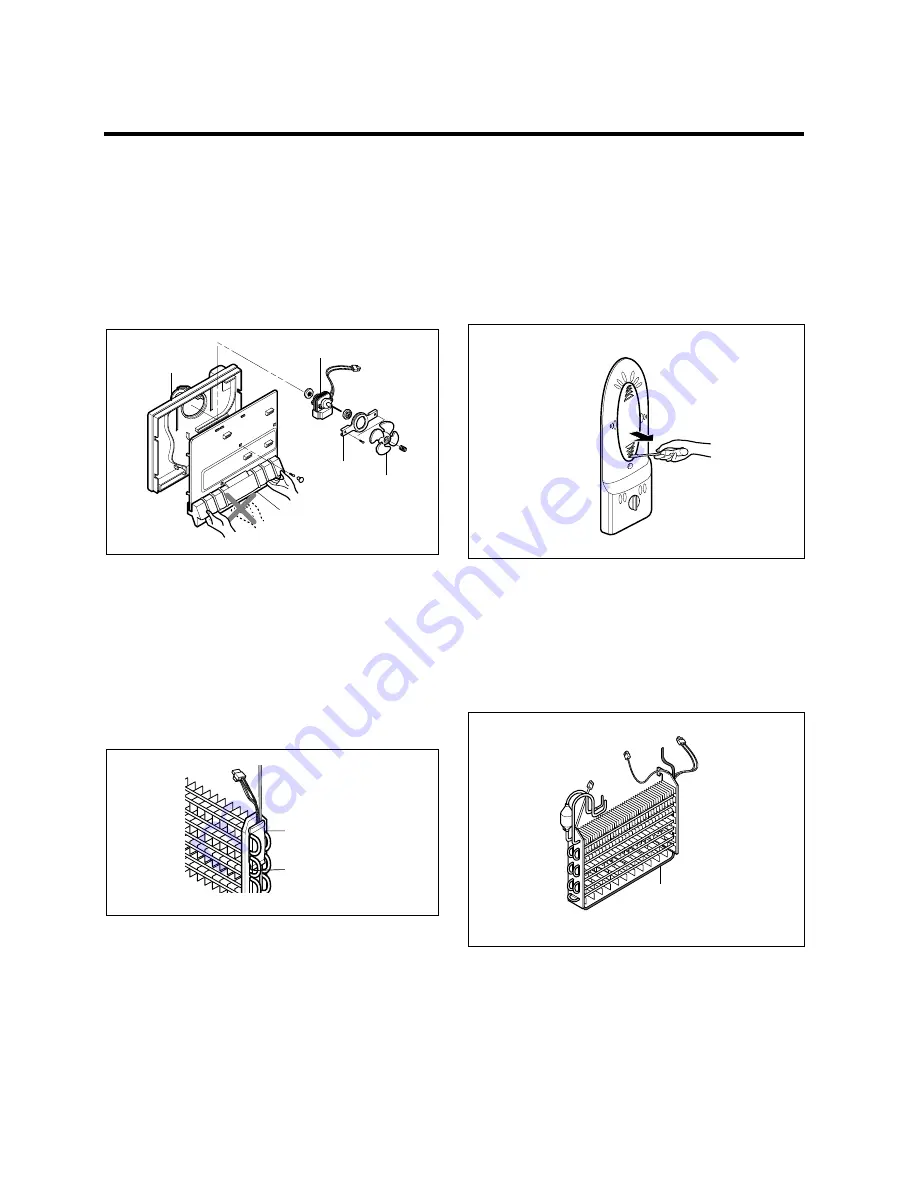
4 FAN AND FAN MOTOR
1) Remove freezer drawers.
2) Remove two cap screws and loosen two screws in Grille Fan.
3) Pull out the Grille Fan and Shroud.
4) Disconnect the housing of lead wire.
5) Separate the Fan Assembly.
6) Losse 2 screw fixed to the Bracket.
7) Pull out Shroud to remove the Fan Motor Assembly.
8) Separate the Motor Bracket and Rubber.
5 DEFROST CONTROL ASSEMBLY
Defrost Control Assembly consists of Thermistor and Melting
Fuse. Thermistor functions to defrost automatically and it is
attached to metal side of the Evaporator and senses temperature.
Melting Fuse is a kind of safety device for preventing overheating
of the Heater when defrosting.
At the temperature of 72°C, it stops the emission of heat from the
Heater.
1) Pull out the Shroud after removing the Grille.
2) Separate the connector connected with the Defrost Control
Assembly and replace new one.
6 DAMPER CONTROL
1) Remove the Cover Lamp and loosen 2 screw.
2) Pull the Control Box and separate the lead wire housing.
3) Remove the Cover Lamp.
4) Separate the Insulation Multi Duct and Control Box.
5) Disassemble the Knob.
6) Separate the Damper Control and Control Box.
7) Separate the Damper Control and Resistor.
8) Disconnect the lead wire.
7 HEATER, SHEATH
In this refrigerator, Heater, Sheath is used for defrosting
heater. During heating, the temperature of heater rises
about 300~500°C. Therefore, be careful not to burn
yourself while servicing.
1) After removing the Grille and Shroud, separate the
Heater Sheath by disconnecting the connectors.
2) Exchanged Heater Sheath and connect the housing.
REFRIGERATOR ROOM LAMP
Heater Sheath
GUIDE FAN
FAN
SHROUD
FAN MOTOR
GRILLE
Melting Fuse
Thermistor
Figure 13
Figure 14
Figure 11
Figure 12
- 8 -