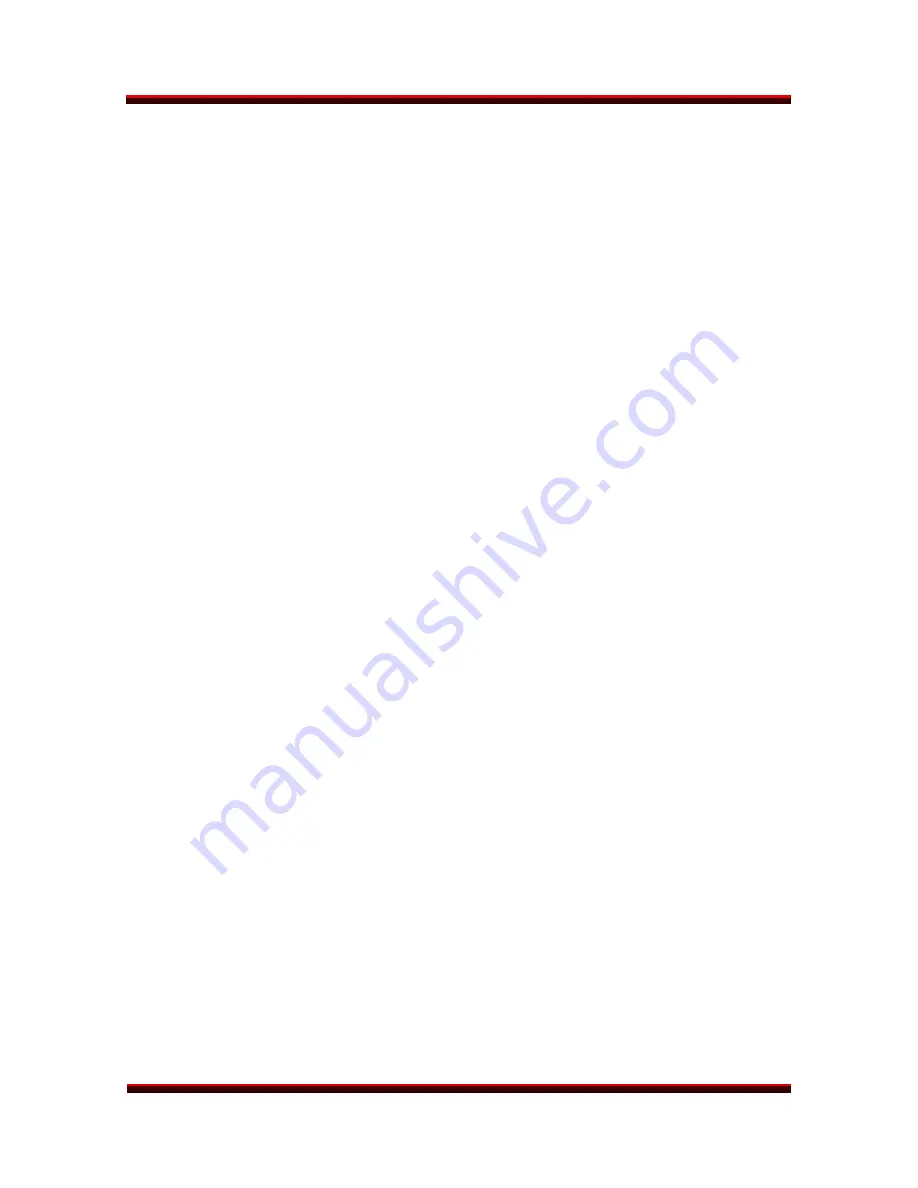
DRYER 9577/9588
DLE9577/DLG9588
Page 57 of 58
TRAINING MANUAL
Loc
No.
DLE9577 DLG9588
Description
M110
5221EL2002A
Valve Assembly, Gas
M140
4974EL1001A
Guide, Burner
M141
4810EL3002A
Bracket, Base
M150
5201EL3001A
Pipe Assembly
M160
5318EL3001A Igniter
M170
4948EL4001B
Orifice, Natural Gas
M171
4948EL4002B Orifice
Kit, Propane Conversion
M180
4932EL4001A
Connector, Pipe
M181
4036EL3002A Gasket
M190
5201EL2001A
Pipe Assembly
M210
3016EL1001A Funnel
M220
6931EL3004B
Thermostat Assembly
M230
6931EL3003C Thermostat
M240
6501EL3001A
Sensor Assembly
M250
4980EL3001A Supporter, Holder
Summary of Contents for DLE9577
Page 1: ...Digital Appliance DLE9577 DLG9588 Dryer Training Spring 2007 Service TRAINING MANUAL ...
Page 4: ...DRYER 9577 9588 DLE9577 DLG9588 Page 4 of 58 TRAINING MANUAL SPECIFICATIONS ...
Page 22: ...DRYER 9577 9588 DLE9577 DLG9588 Page 22 of 58 TRAINING MANUAL TEST 1 AC Electrical Supply ...
Page 26: ...DRYER 9577 9588 DLE9577 DLG9588 Page 26 of 58 TRAINING MANUAL TEST 3 Motor ...
Page 27: ...DRYER 9577 9588 DLE9577 DLG9588 Page 27 of 58 TRAINING MANUAL TEST 4 Moisture Sensor ...
Page 28: ...DRYER 9577 9588 DLE9577 DLG9588 Page 28 of 58 TRAINING MANUAL TEST 5 Door Switch ...
Page 29: ...DRYER 9577 9588 DLE9577 DLG9588 Page 29 of 58 TRAINING MANUAL TEST 6 Heater Electric ...
Page 30: ...DRYER 9577 9588 DLE9577 DLG9588 Page 30 of 58 TRAINING MANUAL TEST 7 Valve Gas ...
Page 31: ...DRYER 9577 9588 DLE9577 DLG9588 Page 31 of 58 TRAINING MANUAL COMPONENT TEST PROCEDURE ...
Page 32: ...DRYER 9577 9588 DLE9577 DLG9588 Page 32 of 58 TRAINING MANUAL COMPONENT TEST PROCEDURE ...
Page 33: ...DRYER 9577 9588 DLE9577 DLG9588 Page 33 of 58 TRAINING MANUAL COMPONENT TEST PROCEDURE ...
Page 50: ...DRYER 9577 9588 DLE9577 DLG9588 Page 50 of 58 TRAINING MANUAL MAIN BOARD ...
Page 51: ...DRYER 9577 9588 DLE9577 DLG9588 Page 51 of 58 TRAINING MANUAL EXPLODED VIEW ...
Page 52: ...DRYER 9577 9588 DLE9577 DLG9588 Page 52 of 58 TRAINING MANUAL EXPLODED VIEW ALL ...
Page 53: ...DRYER 9577 9588 DLE9577 DLG9588 Page 53 of 58 TRAINING MANUAL EXPLODED VIEW ELECTRIC ...
Page 54: ...DRYER 9577 9588 DLE9577 DLG9588 Page 54 of 58 TRAINING MANUAL EXPLODED VIEW GAS ...
Page 58: ...DRYER 9577 9588 DLE9577 DLG9588 Page 58 of 58 TRAINING MANUAL NOTES ...
Page 59: ......
Page 60: ... Copyright 2007 LG Electronics Inc Printed in the USA ...