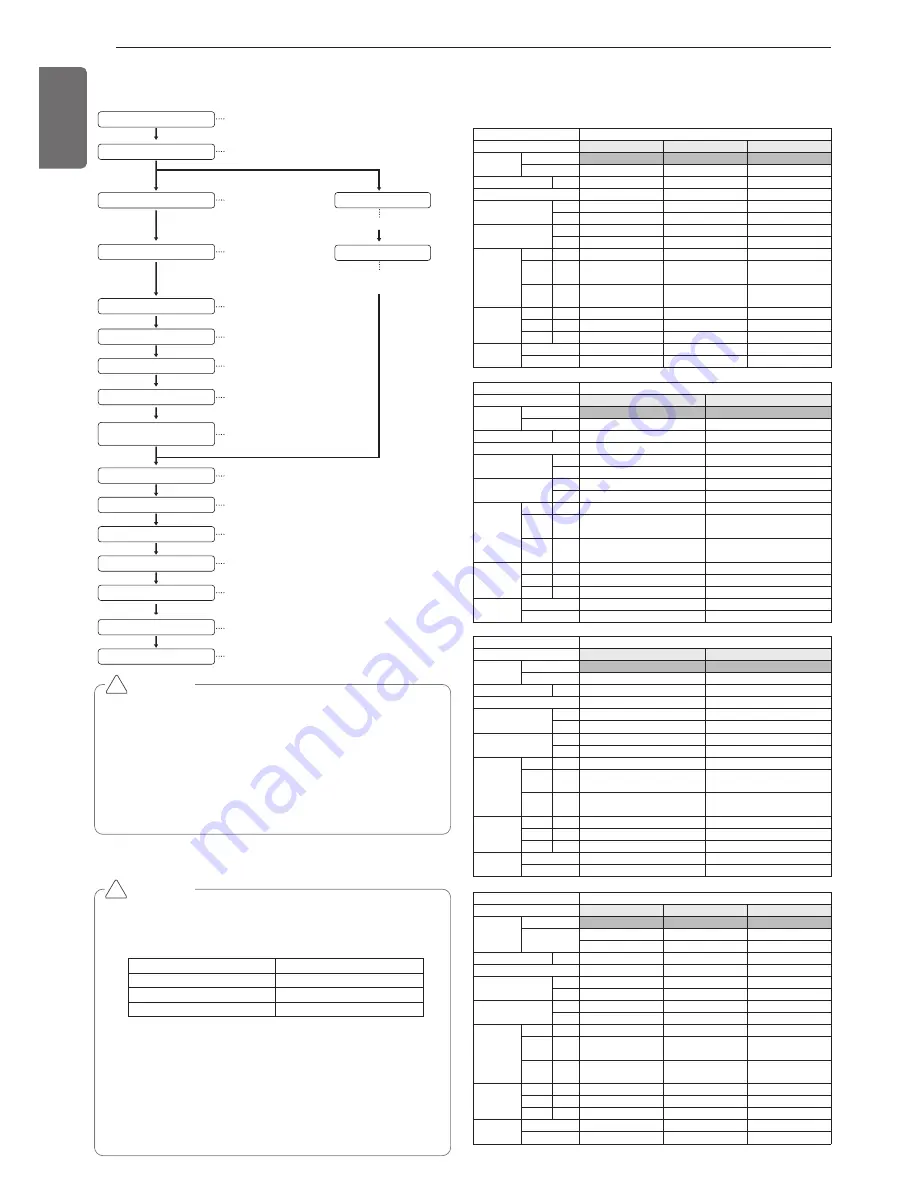
4
ENGLISH
The foundation must be level even
Outside unit foundation work
Avoid short circuits and ensure
sufficient space is allowed for service
Installation of outside unit
Refer to automatic addressing flowchart
Automatic addressing of indoor unit
In the final check for 24hours at 3.8 MPa(38.7 kgf/cm
2
) there
must be no drop in pressure.
Airtight test
Multiple core cable must not be used.
(suitable cable should be selected)
Electrical work
(connection circuits and drive circuits)
Make sure no gaps are left where
the insulating materials are joined
Heat insulation work
Make sure airflow is sufficient
Duct work
Adjust to downward gradient
Drain pipe work
Special attention to dryness,
cleanness and tightness
Refrigerant piping work
Check model name to
make sure the fitting
is made correctly
Installation of indoor unit
Take account of gradient
of drain piping
Sleeve and insert work
Make connection clearly between outside, indoor,
remote controller and option.
Preparation of contract drawings
Indicate clearly who will be responsible for switch setting.
Determination of division work
The vacuum pump used must have a capacity of reaching at least
5 torr, more than 1 hour
Vacuum drying
Recharge correctly as calculated in this manual. and record the
amount of added refrigerant
Additional charge of refrigerant
Make sure there are no gaps left between the facing materials
used on the ceiling
Fit facing panels
Run each indoor unit in turn to make sure the pipe work
has been fitted correctly
Test run adjustment
Explain the use of the system as clearly as possible to your customer and
make sure all relevant documentation is in order
Transfer to customer with explanation
Preheat the crank case with the electrical heater for more than 6 hours.
CAUTION
• The above list indicates the order in which the individual work
operations are normally carried out but this order may be varied
where local conditions warrants such change.
• The thickness of the piping should comply with the relevant
local and national regulations for the designed pressure 3.8MPa.
• Since R410A is a mixed refrigerant, the required additional
refrigerant must be charged in its liquid state.(If the refrigerant
is charged in its gaseous state, its composition changes and the
system will not work properly.)
!
CAUTION
Notes: * We can guarantee the operation only within 130% Combina-
tion. If you want to connect more than 130% combination,
please contact us and discuss the requirement like below.
• If the operation of indoor unit is more than 130%, low airflow
operation is recommended in all the indoor units.
• If the operation of indoor unit is more than 130%, additional re-
frigerant is needed according to the Aheadquarter guidance.
• Over 130%, capacity is same as capacity of 130%, Same re-
mark is valid for power input.
• Ratio of the running Indoor Units to the Outside: Within 10 ~ 100%
• A combination operation over 100% cause to reduce each indoor unit capacity.
Combination Ratio(50~200%)
Outside Unit Number
Connection Ratio
Single outside unit s
200%
Double outside unit s
160%
More than Triple outside unit s
130%
!
OUTSIDE UNITS INFORMATION
Power Supply : 3Ø, 380V, 60Hz or 3Ø, 380 - 415V, 50Hz
Model Name : ARWB***LAS4
Unit
1 Unit
System Capacity (HP)
8
10
12
Model
Combination Unit
ARWB080LAS4
ARWB100LAS4
ARWB120LAS4
Independent Unit
ARWB080LAS4
ARWB100LAS4
ARWB120LAS4
Refrigerant Precharged Amount
kg
5.8
5.8
5.8
Maximum Connectable Number of Indoor Units
13
16
20
Net Weight
kg
127 x 1
127 x 1
127 x 1
lbs
280 x 1
280 x 1
280 x 1
Dimensions(WxHxD)
mm
755 × 997 × 500
755 × 997 × 500
755 × 997 × 500
inch (29-23/32 x 39-1/4 x 19-11/16) x 1 (29-23/32 x 39-1/4 x 19-11/16) x 1 (29-23/32 x 39-1/4 x 19-11/16) x 1
Refrigerant
Connecting Pipes
Liquid Pipes mm(inch)
9.52(3/8)
9.52(3/8)
12.7(1/2)
Low Pressure
Gas Pipes
mm(inch)
22.7(7/8)
22.7(7/8)
25.4(1)
High Pressure
Gas Pipes
mm(inch)
19.05(3/4)
19.05(3/4)
19.05(3/4)
Water Connect-
ing Pipes
Inlet
mm PT40(Internal thread)
PT40(Internal thread)
PT40(Internal thread)
Outlet
mm PT40(Internal thread)
PT40(Internal thread)
PT40(Internal thread)
Drain Outlet
mm PT20(External thread) PT20(External thread) PT20(External thread)
Temp. range of
Circulation water
Cooling
10°C ~ 45°C(50°F ~ 113°F)
10°C ~ 45°C(50°F ~ 113°F)
10°C ~ 45°C(50°F ~ 113°F)
Heating
-5°C ~ 45°C(23°F ~ 113°F)
-5°C ~ 45°C(23°F ~ 113°F)
-5°C ~ 45°C(23°F ~ 113°F)
Unit
2 Unit
System Capacity (HP)
Model
Combination Unit
Independent Unit
Refrigerant Precharged Amount
kg
Maximum Connectable Number of Indoor Units
Net Weight
kg
lbs
Dimensions(WxHxD)
mm
inch
Refrigerant
Connecting Pipes
Liquid Pipes mm(inch)
Low Pressure
Gas Pipes
mm(inch)
High Pressure
Gas Pipes
mm(inch)
Water Connect-
ing Pipes
Inlet
mm
Outlet
mm
Drain Outlet
mm
Temp. range of
Circulation water
Cooling
Heating
Unit
1 Unit
System Capacity (HP)
Model
Combination Unit
Independent Unit
Refrigerant Precharged Amount
kg
Maximum Connectable Number of Indoor Units
Net Weight
kg
lbs
Dimensions(WxHxD)
mm
inch
Refrigerant
Connecting Pipes
Liquid Pipes mm(inch)
Low Pressure
Gas Pipes
mm(inch)
High Pressure
Gas Pipes
mm(inch)
Water Connect-
ing Pipes
Inlet
mm
Outlet
mm
Drain Outlet
mm
Temp. range of
Circulation water
Cooling
Heating
18
20
ARWB180LAS4
ARWB200LAS4
ARWB180LAS4
ARWB200LAS4
3
3
29
32
140 x 1
140 x 1
309 x 1
309 x 1
755 × 997 × 500
755 × 997 × 500
(29-23/32 x 39-1/4 x 19-11/16) x 1 (29-23/32 x 39-1/4 x 19-11/16) x 1
12.7(1/2)
12.7(1/2)
28.58(1-1/8)
28.58(1-1/8)
19.05(3/4)
19.05(3/4)
PT40(Internal thread)
PT40(Internal thread)
PT40(Internal thread)
PT40(Internal thread)
PT20(External thread)
PT20(External thread)
10°C ~ 45°C(50°F ~ 113°F)
10°C ~ 45°C(50°F ~ 113°F)
-5°C ~ 45°C(23°F ~ 113°F)
-5°C ~ 45°C(23°F ~ 113°F)
Unit
1 Unit
System Capacity (HP)
Model
Combination Unit
Independent Unit
Refrigerant Precharged Amount
kg
Maximum Connectable Number of Indoor Units
Net Weight
kg
lbs
Dimensions(WxHxD)
mm
inch
Refrigerant
Connecting Pipes
Liquid Pipes mm(inch)
Low Pressure
Gas Pipes
mm(inch)
High Pressure
Gas Pipes
mm(inch)
Water Connect-
ing Pipes
Inlet
mm
Outlet
mm
Drain Outlet
mm
Temp. range of
Circulation water
Cooling
Heating
14
16
ARWB140LAS4
ARWB160LAS4
ARWB140LAS4
ARWB160LAS4
5.8
3
23
26
127 x 1
140 x 1
280 x 1
309 x 1
755 × 997 × 500
755 × 997 × 500
(29-23/32 x 39-1/4 x 19-11/16) x 1 (29-23/32 x 39-1/4 x 19-11/16) x 1
12.7(1/2)
12.7(1/2)
25.4(1)
28.58(1-1/8)
19.05(3/4)
19.05(3/4)
PT40(Internal thread)
PT40(Internal thread)
PT40(Internal thread)
PT40(Internal thread)
PT20(External thread)
PT20(External thread)
10°C ~ 45°C(50°F ~ 113°F)
10°C ~ 45°C(50°F ~ 113°F)
-5°C ~ 45°C(23°F ~ 113°F)
-5°C ~ 45°C(23°F ~ 113°F)
22
24
26
ARWB220LAS4
ARWB240LAS4
ARWB260LAS4
ARWB120LAS4
ARWB120LAS4
ARWB140LAS4
ARWB100LAS4
ARWB120LAS4
ARWB120LAS4
5.8 + 5.8
5.8 + 5.8
5.8 + 5.8
35
39
42
127 x 2
127 x 2
127 x 2
280 x 2
280 x 2
280 x 2
(755 × 997 × 500) x 2
(755 × 997 × 500) x 2
(755 × 997 × 500) x 2
(29-23/32 x 39-1/4 x 19-11/16) x 2 (29-23/32 x 39-1/4 x 19-11/16) x 2 (29-23/32 x 39-1/4 x 19-11/16) x 2
19.05(3/4)
19.05(3/4)
19.05(3/4)
34.9(1-3/8)
34.9(1-3/8)
34.9(1-3/8)
28.58(1-1/8)
28.58(1-1/8)
28.58(1-1/8)
PT40(Internal thread)
PT40(Internal thread)
PT40(Internal thread)
PT40(Internal thread)
PT40(Internal thread)
PT40(Internal thread)
PT20(External thread) PT20(External thread) PT20(External thread)
10°C ~ 45°C(50°F ~ 113°F) 10°C ~ 45°C(50°F ~ 113°F) 10°C ~ 45°C(50°F ~ 113°F)
-5°C ~ 45°C(23°F ~ 113°F) -5°C ~ 45°C(23°F ~ 113°F) -5°C ~ 45°C(23°F ~ 113°F)
INSTALLATION PROCESS
Summary of Contents for ARWB080LAS4
Page 44: ......