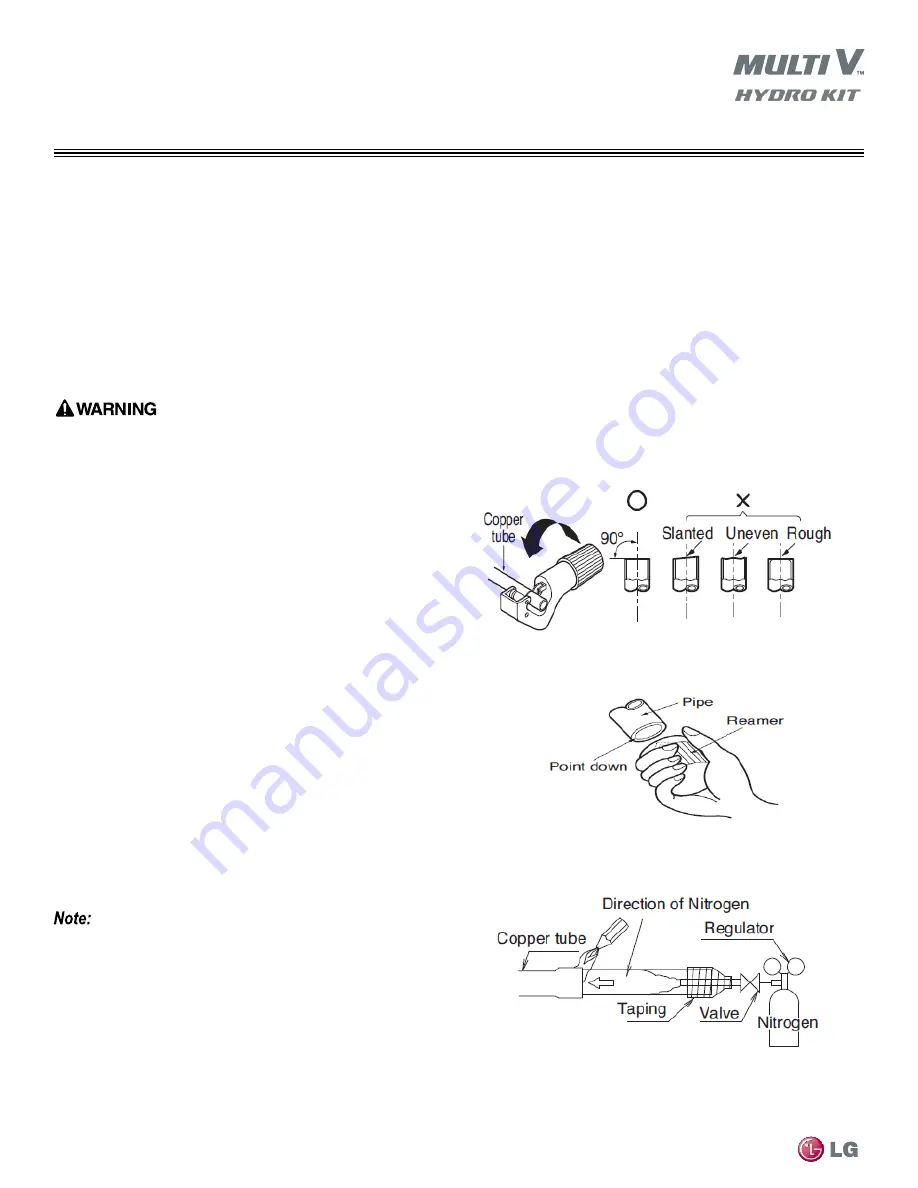
24
MUL
TI V Hydro Kit Installation Manual
Due to our policy of continuous product innovation, some specifications may change without notification.
©LG Electronics U.S.A., Inc., Englewood Cliffs, NJ. All rights reserved. “LG Life’s Good” is a registered trademark of LG Corp.
Piping
rouGHING-IN
refrigerant Piping
refrigerant Safety
ASHRAE Standards 15-2010 and 34-2010 offer guidelines that address refrigerant safety and the maximum allowable concentration of refrig-
erant in an occupied space. Refrigerant will dissipate into the atmosphere, but a certain volume of air is required for this to occur safely.
For R410A refrigerant, the maximum allowable concentration of refrigerant is twenty-six (26) lbs. per 1,000 cubic feet of an occupied space.
Buildings with twenty-four (24) hour occupancy allow half of that concentration.
1
ASHRAE Standards 15 and 34 assume that if a system develops a leak, its entire refrigerant charge will dump into the area where the leak
occurs. To meet ASHRAE Standards 15 and 34, calculate the refrigerant concentration that may occur in the smallest room volume on the
system, and compare the results to the maximum allowable concentration number.
1
Also consult state and local codes in regards to refriger-
ant safety.
Verify that the maximum refrigerant concentration level in the space where the indoor unit will be mounted meets the concentration limit for the
application.
1
Information about ASHRAE Standard 15-2010 / 34-2010 and addenda current as of the date of this publication.
cutting the Pipes
• Use the accessory piping kit or use pipes purchased locally
(Figure 10).
• Measure the distance between the indoor and outdoor units.
• Cut the pipes a little longer than the measured distance.
removal of burrs
• Completely remove all burrs from the cut cross section of pipe/tube
(Figure 11).
• Be sure the end of the copper tubing is pointed downward (toward
the floor) as you remove burrs. This will prevent the burrs from
falling back into the tubing.
Pipe brazing
Make sure to flow Nitrogen during brazing.
If brazing is done without
flowing Nitrogen, it can generate a thick oxidized coating within the pipe
which will interfere with the normal operation of valve and compressor
(Figure 12).
Figure 10: Cutting Pipes
Figure 11: Removing Burrs for Piping
Figure 12: Brazing Pipes