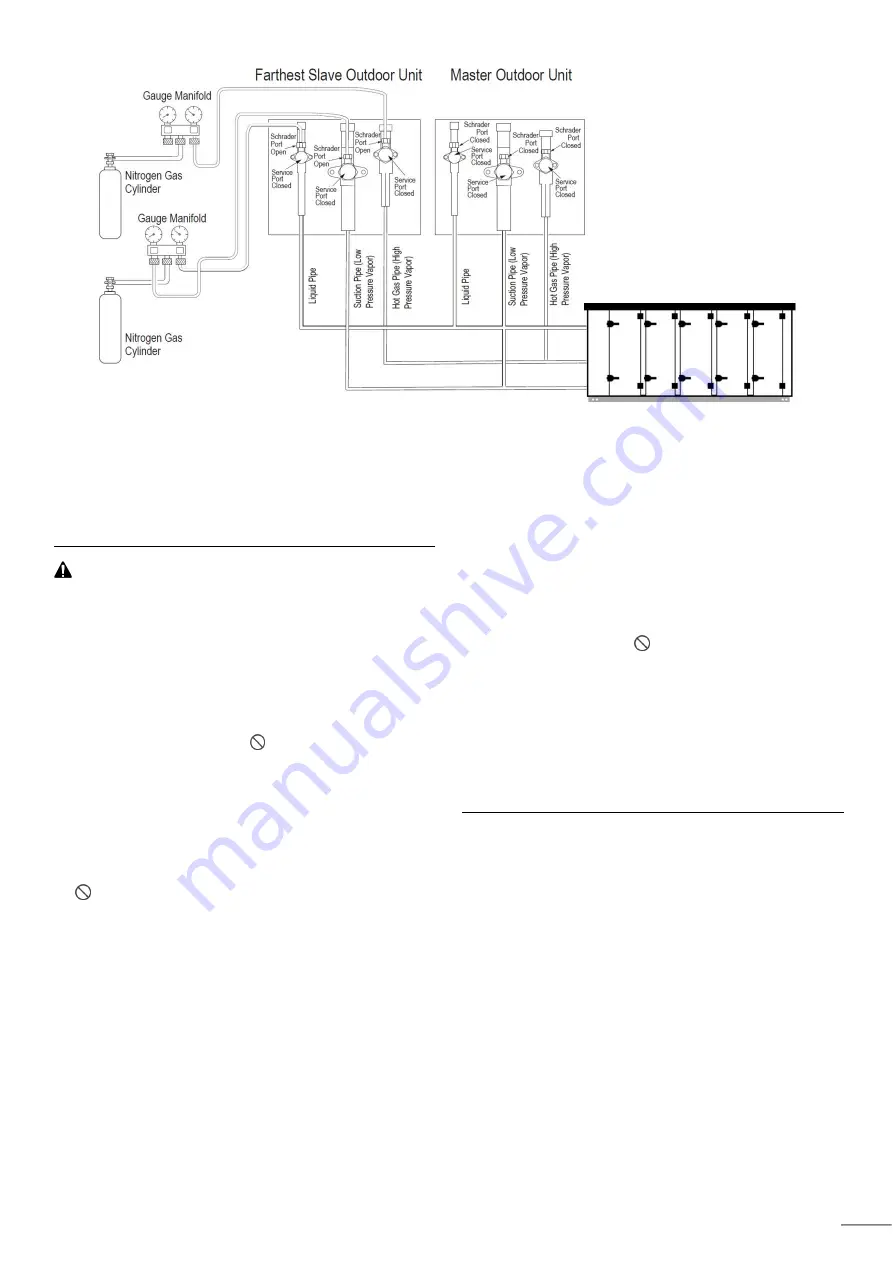
Due to our policy of continuous product innovation, some specifications may change without notification.
©LG Electronics U.S.A., Inc., Englewood Cliffs, NJ. All rights reserved. “LG” is a registered trademark of LG Corp.
34
Figure 17: Leak / Pressure Test for system designed for DOAS
Evacuation
After the leak / pressure check is complete, perform a
Triple Evacuation with the entire system. Evacuation
must be performed through the Schrader ports on the
outdoor unit service ports.
WARNING
•
For faster evacuation, the Schrader core can be removed,
and an auxiliary service port can used. Make sure to re-
install the original Schrader core before operating the
system.
•
For Heat Recovery systems, evacuate through all three (3)
hot gas line (high pressure vapor), liquid line, and suction
(low pressure vapor) refrigerant lines.
•
The outdoor unit service valves must remain closed and the
stem head access caps tight. Do not open the outdoor
unit service valves and release the factory refrigerant
charge until the LG trained commissioner authorizes to do
so. The system must be left in vacuum until the LG trained
commissioner verifies the quality of the evacuation.
•
Any field-installed ball valves in the refrigerant system (if
used) must be open to ensure all piping is free and clear for
evacuation on all piping and connected DOAS units
•
Do not apply power to the units before performing a
system leak test. There is a possibility that the EEV valves
will close and isolate sections of the piping system, making
the leak test inconclusive. Contact your LG Applied Rep or
service technician for the procedure to reopen the EEV
valves before the leak test ONLY if the power has been
applied
•
For multi-frame outdoor units, connect the vacuum pump /
manifold to the service port Schrader ports (or core) to only
one outdoor unit, preferably the slave outdoor unit that is
installed farthest away from the refrigerant piping system
and connected DOAS units
•
Use only a vacuum pump that can reach 500 microns,
vacuum rated hoses or copper tubing, and a leak-free
gauge manifold set
•
Use only new vacuum pump oil from a properly sealed
(unopened) container, and change oil in pump before
EVERY
use.
•
Subsequent oil changes will be necessary after several
hours of continuous operation; have extra oil on hand.
•
Use a quality micron gauge in good operating order and
install as far away from pump as possible
•
Connect the vacuum pump to the gauge manifold and
hoses. Once the vacuum pump is first operated, if hoses,
manifold, and vacuum valves are leak free (and oil is no
moisture laden), the gauge must read <100 microns within
on (1) minute.
•
Use a vacuum pump or Inert (nitrogen) gas when doing
leakage test or air purge. Do not compress air or Oxygen
and do not use Flammable gases. Otherwise, it may cause
fire or explosion. There is the risk of death, injury, fire or
explosion
.
•
If the outdoor unit is moved to and installed in another site,
only charge with new refrigerant after successful leak test
and triple evacuation procedures have been performed. If
different refrigerant or air is mixed with the original
refrigerant, the refrigerant cycle will malfunction and the unit
will be damaged.