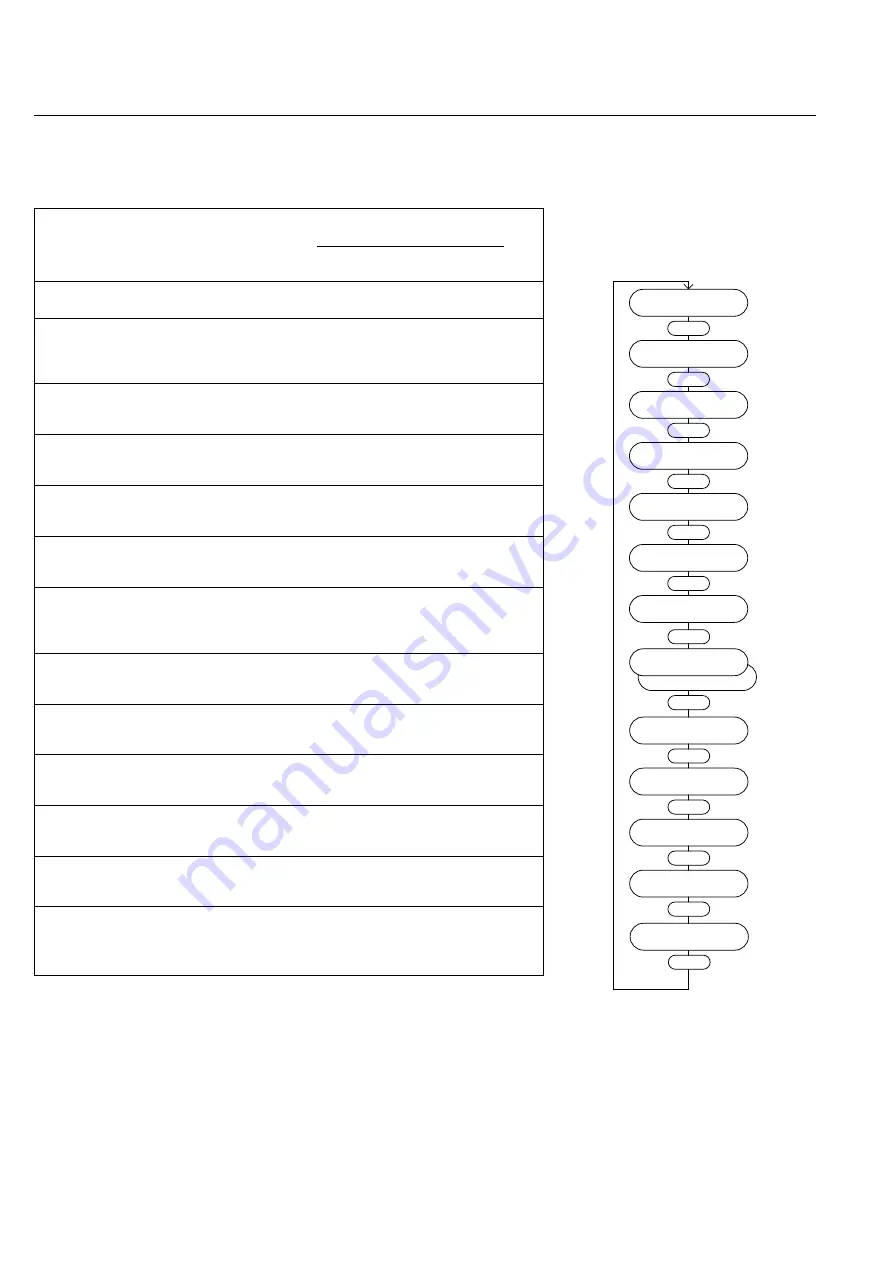
4.3.1 Basic menu
Menu item
Description
Adjustable value / option
Ac-
cess
min.
max.
stan-
Unit
value
value
dard
Ready
Operating display
-
-
-
-
-
Freq. Setpoint
Sets the speed for operation
150
480
480
Hz
r/w
!! Every change is directly written
into the pump’s data storage
and is valid immediately!!
Operation Hours Total operating hours of the pump
actual value
h
r
Motor Temp.
Motor temperature
actual value
°
C
r
Converter Temp. Temperature of the power
actual value
°
C
r
electronic
Bearing Temp.
Temperature of the magnetic
actual value
°
C
r
bearing
Actual Value TMS Temperature of the Temperature
actual value
°
C
r
Management System
Cooling Temp.
Cooling water temperature
actual value
°
C
r
Actual PVW 13
Rotor displacement in the
magnetic bearing
actual value
%
r
plane VW13
Actual PVW 24
Rotor displacement in the
magnetic bearing
actual value
%
r
plane VW24
Actual PZ 12
Rotor displacement in the
magnetic bearing
actual value
%
r
axis Z12
Power
Power consumption of the drive
actual value
W
r
Software Version
Actual software version
actual value
-
r
Plug-in control
32
GA 05.136/2.02 - 10/98
Ready
0.0 A 0 Hz
Enter
Freq. Setpoint
480 Hz
Enter
Operation Hours
0.00 h
Enter
Motor Temp.
50
°
C
Enter
Converter Temp.
40
°
C
Enter
Bearing Temp.
50
°
C
Enter
Actual PVW 13
10%
Enter
Actual PVW 24
10%
Enter
Actual PZ 12
5%
Enter
Power
400 W
Enter
Actual Value TMS
Not Active
Enter
Not Active
Cooling Temp.
20
°
C
Enter
r (read) = value can only be read
r /w (read/write) = value can be read and written
4.3 Operating menu
Software Version
104.xx
Enter