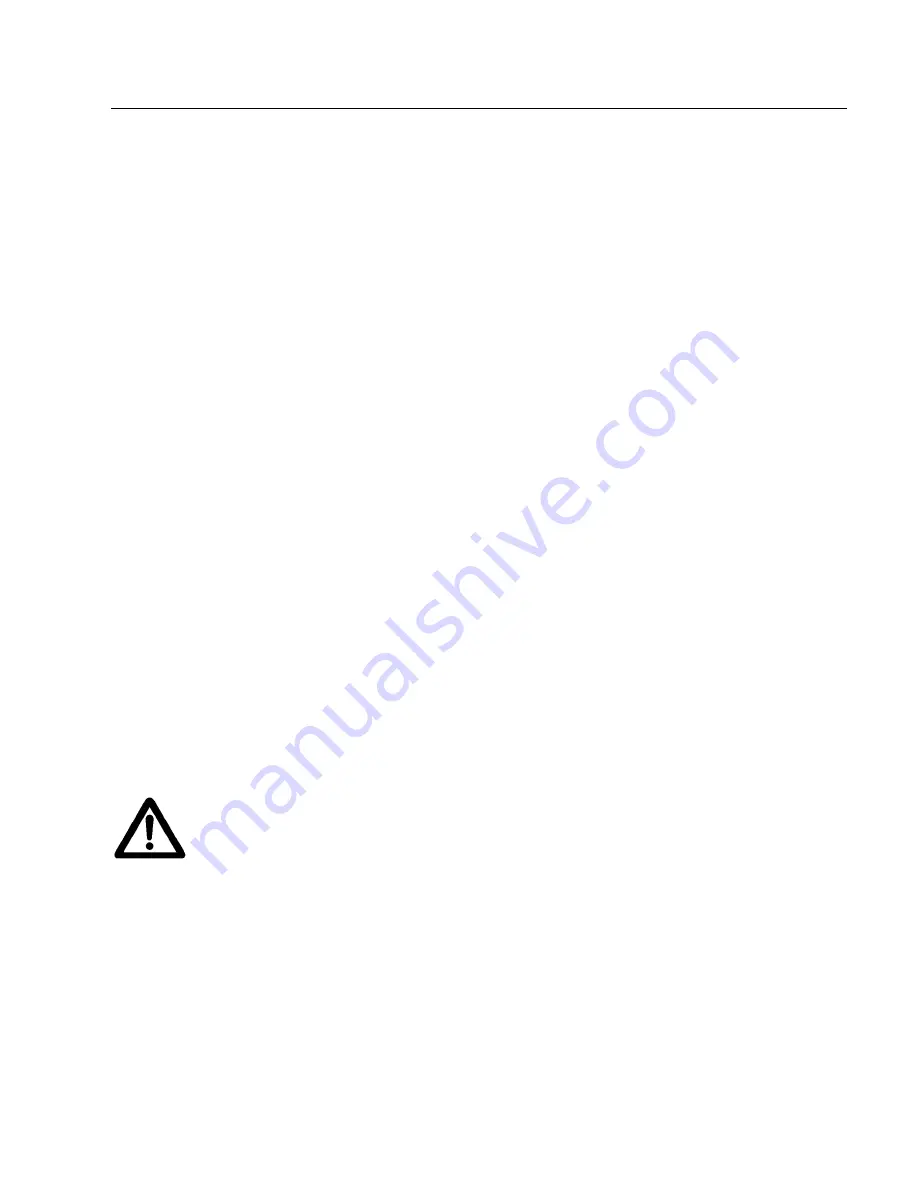
23
GA 01.600/10.02 - 07/01
Checking / Maintenance
Especially note the position of the oil
ejection hole (see arrow in Fig. 10) in the
end plate A. The hole must always lead
downward.
3.6 Full Maintenance
Clean the pump and run maintenance on it.
Clean and perform maintenance on the pump as descri-
bed in the instructions for Maintenance Kit 2.
3.7 Leybold Service
If a pump is returned to Leybold, indicate whether the
pump free of substances damaging to health or whether
it is contaminated.
If it is contaminated also indicate the nature of the
hazard. For this you must use a form which has been
prepared by us which we will provide upon request.
A copy of this form is reproduced at the end of these
Operating Instructions: „Declaration of Contamination of
Vacuum Instruments and Components“.
Please attach this form to the pump or enclose it with the
pump.
This „Declaration of Contamination“ is required to meet
the requirements of German Law and to protect our per-
sonnel.
Leybold must return any pumps without a
„Declaration of Contamination“ to the sen-
der’s address.
The pump must be packed in such a way,
that it will not be damaged during shipping
and so that any contaminants are not relea-
sed from the package.
3.8 Shelving
Before putting a pump into operation once
more it should be stored in a dry place pre-
ferably at room temperature (20
°
C). Before
the pump is shelved it must be properly dis-
connected from the vacuum system, purged
with dry nitrogen and the oil should be
changed too.
The inlets and outlets of the pump must be
sealed with suitable seals.
The gas ballast valve must be set to the „0“
position and if the pump is to be shelved for
a longer period of time it should be sealed
in a PE bag containing some desiccant (sili-
ca gel).
When a pump is put into operation after it has been shel-
ved for over one year, standard maintenance should be
run on the pump and the oil should also be exchanged
(see Section 3.2). We recommend that you contact the
Leybold Service.
Caution
Warning
Caution
Caution
Summary of Contents for D10E
Page 1: ......
Page 33: ...GA 01 600 10 02 07 01 33 ...