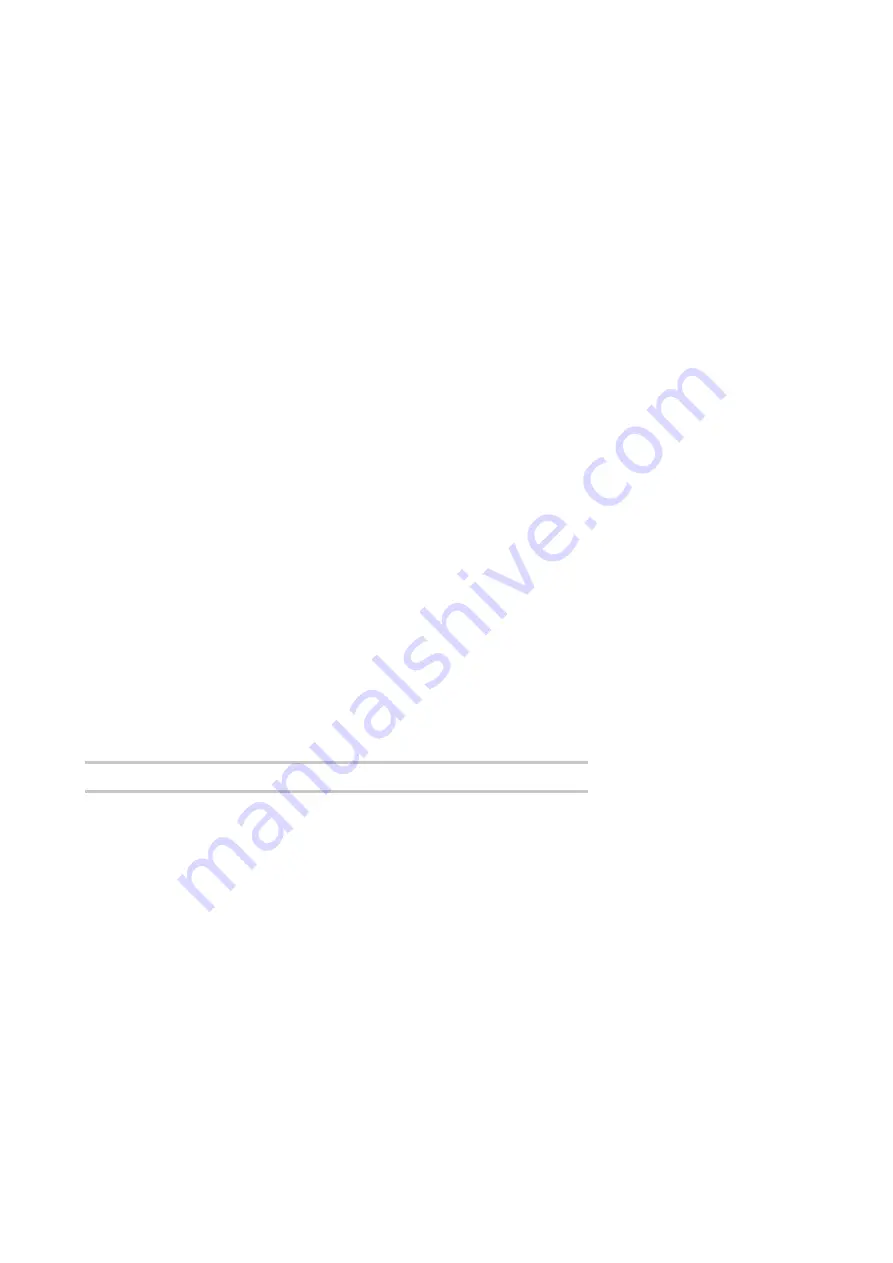
37
GA01208_002_C0 - 11/2016 - © Leybold
Maintenance
Required tools:
Screwdriver 1.0 x 5.5 mm (for junction box), open-jaw wrenches 7 mm and
19 mm (for junction box), Allan keys 3 mm, 5 mm, 6 mm, possibly a puller for
the coupling.
Disconnect the pump from the mains.
Unscrew the four
non-recessed
hex. socket screws (11/3).
Remove the intermediate flange (11/5) together with the electric motor (11/4).
Remove the handle (11/2).
Loosen the threaded pin (11/8) and pull the coupling (11/7) with the fan blade
off the motor shaft.
Remove the gasket (11/1).
Unscrew the hex. socket screws (11/6).
Remove the electric motor (11/4).
Clean all parts and check that they are in perfect condition; if not, replace
them with new parts.
Reassemble in the reverse order.
5.8 Replacing the Shaft Seal
Required tools:
Allen keys size 3, 5 and 8, flat-nose pliers, plastic hammer, shaft seal driver,
possibly a puller for the coupling.
Required spare parts:
Shaft seal (12/8)
For material No., see spare parts list
Bushing (12/6)
For material No., see spare parts list
The TRIVAC-B-DOT has one shaft seal. Oil marks under the coupling hou-
sing are signs of a damaged shaft seal.
The shaft seal (12/8) can be replaced without removing or disassembling the
pump module.
Shutdown the pump.
Drain the oil (see Chapter 5.4).
Support the motor.
Unscrew the four
non-recessed
hex. socket screws (11/3) and remove the
motor (11/4) with the intermediate flange.
Remove the gasket (11/1).
Remove the coupling element (12/1).
Unscrew the hexagon socket screw (12/2) and remove the spring washer
(12/3).
Pull off the coupling half (12/4).
Remove the key (12/5).