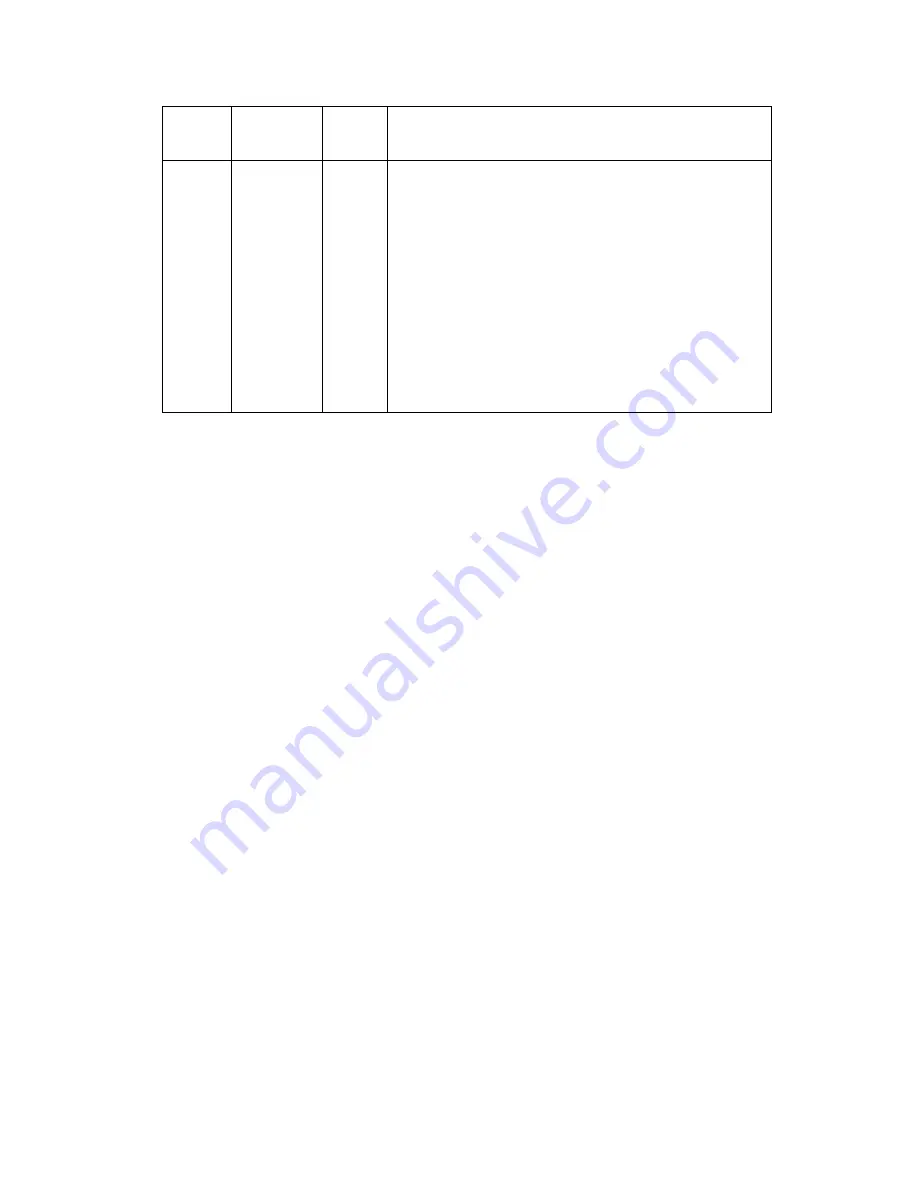
Parts Catalog 6-3
Ref
Part
Number
Units
Description
1-1
11A4200
1
Cover Assembly, Top
-2
11A4202
1
Door, Top Cover
-3
11A4203
1
Hinge, Door, Outer Left
-4
11A4204
2
Hinge, Door, Inner
-5
11A4205
1
Hinge, Door, Outer Right
-6
3
Screw, PP 12A4039
-7
11A4208
1
Control Panel with English Overlay
-7
11A4209
1
Control Panel Overlay, W.T. Kit
-8
11A4210
1
Cable, Operator Panel
-9
11A4211
1
Cable, Print Density
Summary of Contents for Optra K 4046
Page 15: ...Notices and Safety Information xv Chinese Laser Notice Korean Laser Notice ...
Page 19: ...Notices and Safety Information xix ...
Page 20: ...xx Service Manual ...
Page 26: ...1 6 is transmitted to the paper feed roller ...
Page 30: ...1 10 ...
Page 60: ...2 30 ...
Page 97: ...Repair Information 4 21 ...
Page 109: ...Locations 5 1 5 Locations Front and Right Side of Printer ...
Page 110: ...5 2 Rear and Left Side of Printer ...
Page 111: ...Locations 5 3 Interior of Printer with Upper Door Open ...
Page 112: ...Locations 5 4 Optional Multi Function Feeder and Paper Feeder ...
Page 113: ...Locations 5 5 Sensors ...
Page 114: ...5 6 EP Diagram ...
Page 115: ...Locations 5 7 Engine Board ...
Page 116: ...Locations 5 8 Control Board ...
Page 117: ...Locations 5 9 Power Supply Board ...
Page 118: ...5 10 Interconnect Board ...
Page 120: ...6 2 Assembly 1 Upper Cover ...
Page 122: ...6 4 Assembly 2 Covers ...
Page 124: ...6 6 Assembly 3 Electronics ...
Page 126: ...6 8 Assembly 3 Electronics cont ...
Page 128: ...6 10 Assembly 4 Frame Left Side ...
Page 130: ...6 12 Assembly 5 Frame Right Side ...
Page 132: ...6 14 Assembly 6 Input Paper Feed ...
Page 134: ...6 16 Assembly 7 Printhead and Paper Feed Redrive ...
Page 136: ...6 18 Assembly 8 Exit Paper Feed Frame ...
Page 138: ...6 20 Assembly 9 Fuser ...
Page 140: ...6 22 Assembly 10 Paper Tray 250 Sheet ...
Page 142: ...6 24 Assembly 11 Optional 450 Sheet Second Paper Tray ...
Page 144: ...6 26 Assembly 12 Optional 450 Sheet Second Paper Drawer 2 ...
Page 146: ...6 28 Assembly 13 Optional 450 Sheet Second Paper Drawer 2 ...
Page 148: ...6 30 Assembly 14 Optional Multi Function Feeder ...
Page 149: ...Parts Catalog 6 31 Ref Part Number Units Description 14 1 12A4024 1 Feeder Multi Function ...
Page 152: ...6 34 ...