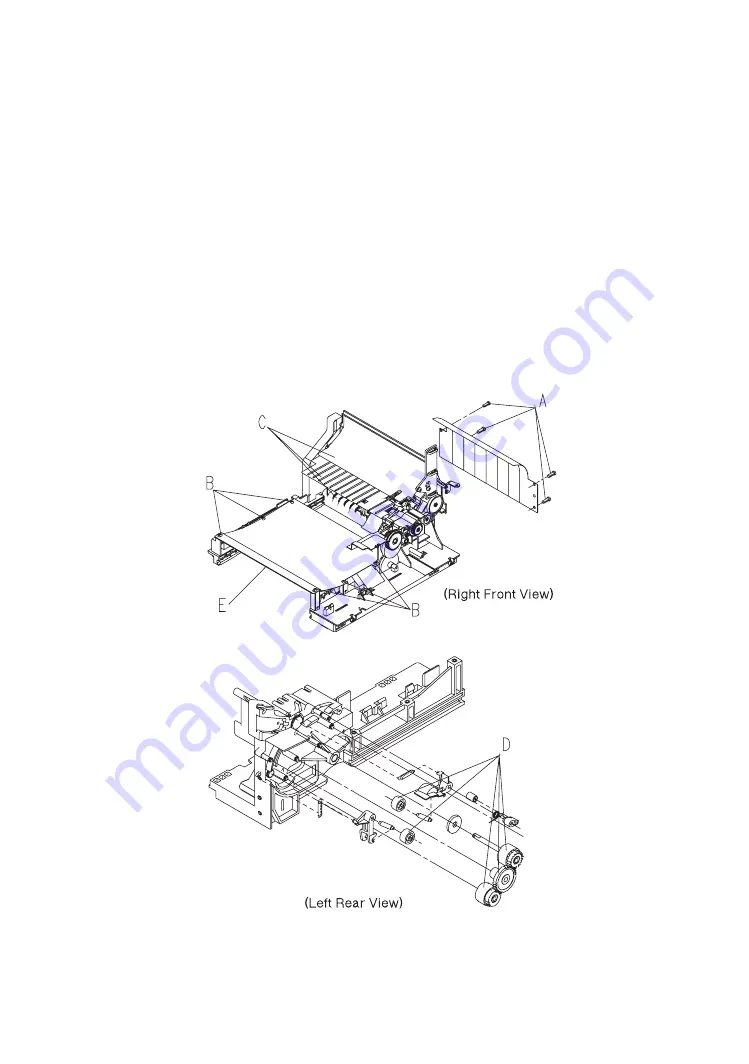
Repair Information
87
4039-1XX
Paper Feed Rollers Removal
Note: Replace all paper feed drive rollers at the same time.
1. Remove the lower frame.
2. Disconnect the system cable from the input sensor.
3. Remove the screws [A] and the outer deflector.
4. Remove the screws [B] and the toner shield [E].
5. Separate the side frames.
6. Pull the guides [C] out of the side frames.
7. Use a flat-blade tool to snap the gears and rollers [D] off the
shaft.
Summary of Contents for 4039 - B/W Laser Printer
Page 69: ...Repair Information 55 4039 1XX ...
Page 77: ...Repair Information 63 4039 1XX ...
Page 79: ...Repair Information 65 4039 1XX ...
Page 83: ...Repair Information 69 4039 1XX ...
Page 85: ...Repair Information 71 4039 1XX D B C A ...
Page 87: ...Repair Information 73 4039 1XX ...
Page 91: ...Repair Information 77 4039 1XX B A ...
Page 93: ...Repair Information 79 4039 1XX F E B F D C ...
Page 105: ...Repair Information 91 4039 1XX ...
Page 113: ...Repair Information 99 4039 1XX ...
Page 116: ...102 Service Manual 4039 1XX Gear Train ...
Page 117: ...Connector Locations 103 4039 1XX HVPS ...
Page 120: ...106 Service Manual 4039 1XX System Board Connectors 10R 12R 12L ...
Page 122: ...108 Service Manual 4039 1XX System Board Connectors 16L ...
Page 124: ...110 Service Manual 4039 1XX System Board Connectors 10P J21 J14 J11 ...
Page 132: ...118 Service Manual 4039 1XX Toner Shield to Lower Frame Load Box Shaft to Upper Frame ...
Page 139: ...Parts Catalog 125 4039 1XX Assembly 1 Covers 1 14 2 1A 12 1B 17 10 4 3 16 15 11 9 8 27 5 6 7 ...
Page 151: ...Parts Catalog 137 4039 1XX Assembly 4 Printhead System Board 9 2 7 6 4 3 1 8B 8A 8 ...
Page 157: ...Parts Catalog 143 4039 1XX Assembly 6 Paper Feed Alignment Gears ...
Page 161: ...Parts Catalog 147 4039 1XX Assembly 8 Standard Paper Tray 200 sheet 1 5 2 3 4 6 ...
Page 163: ...Parts Catalog 149 4039 1XX Assembly 9 Paper Tray 500 Sheet 5A ...
Page 165: ...Parts Catalog 151 4039 1XX Assembly 10 Base for Paper Drawer 500 Sheet 4 4 2 1 3 ...
Page 173: ...Parts Catalog 159 4039 1XX Assembly 13 Electronics 5A 7 13 6 9 11 5 4A 4 3 18 1 18 23 21 22 ...
Page 177: ...Parts Catalog 163 4039 1XX Assembly 14 Transfer Roll ...
Page 181: ...Parts Catalog 167 4039 1XX Assembly 16 Envelope and 100 Sheet Auxiliary Feeder ...