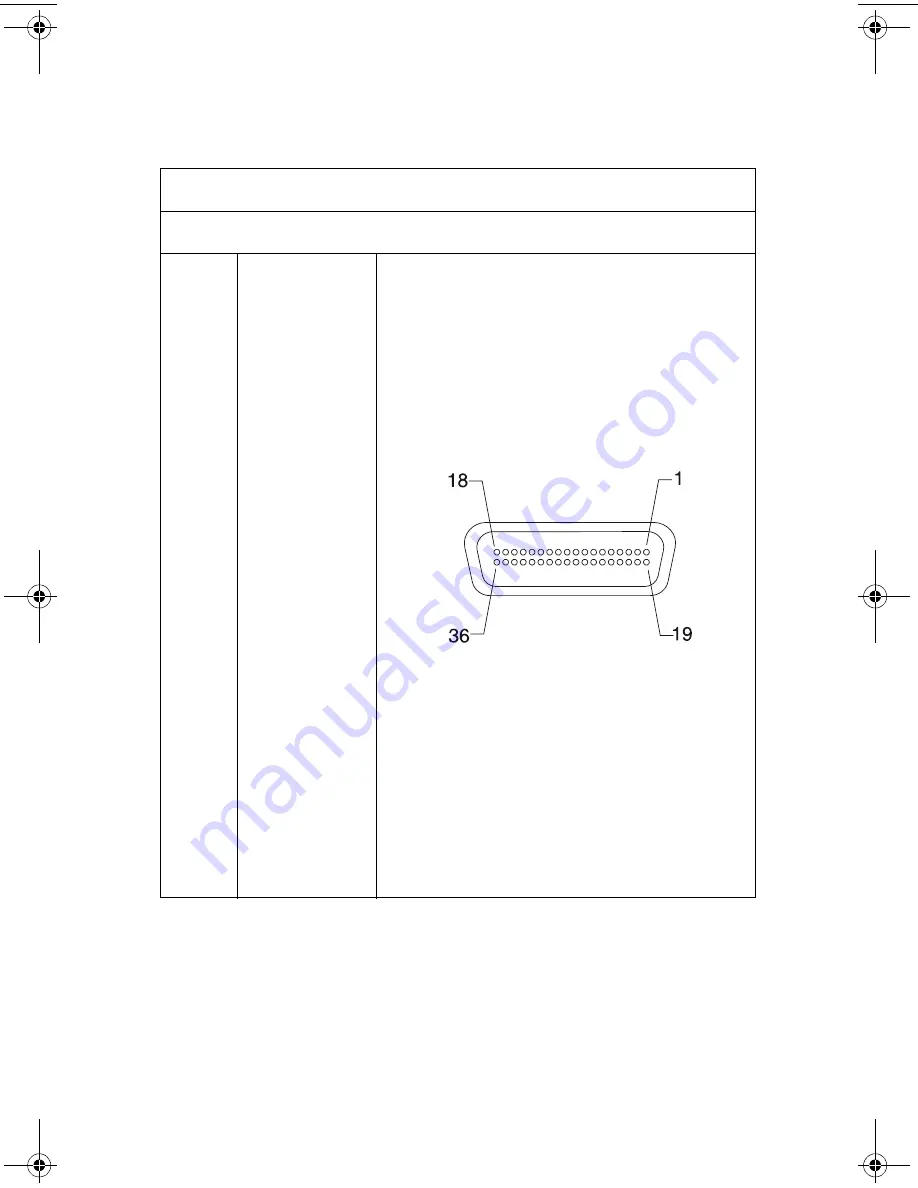
5-12
Main Logic Board <--> Parallel Interface Cable
Main Logic Board
CN1
Pin 1
Pin 2
Pin 3
Pin 4
Pin 5
Pin 6
Pin 7
Pin 8
Pin 9
Pin 10
Pin 11
Pin 12
Pin 13
Pin 14
Pin 15
Pin 16
Pin 17
Pin 18
Pin 19
Pin 20
Pin 21
Pin 22
Pin 23
Pin 24
Pin 25
Pin 26
Pin 27
Pin 28
Pin 29
Pin 30
Pin 31
Pin 32
Pin 33
Pin 34
Pin 35
Pin 36
-STROBE
DATA 0
DATA 1
DATA 2
DATA 3
DATA 4
DATA 5
DATA 6
DATA 7
-ACKNLG
BUSY
PE
SELECT
AUTO FEED
(Not Used)
SIGNAL GND
CHASSIS GND
(Not Used)
SIGNAL GND
SIGNAL GND
SIGNAL GND
SIGNAL GND
SIGNAL GND
SIGNAL GND
SIGNAL GND
SIGNAL GND
SIGNAL GND
SIGNAL GND
SIGNAL GND
SIGNAL GND
-INIT
-ERROR
SIGNAL GND
(Not Used)
(Not Used)
-SELECT IN
23xx.bk Page 12 Wednesday, March 13, 2002 10:42 AM
Summary of Contents for 2380 - Forms Printer B/W Dot-matrix
Page 10: ...xii Korean Safety Information ...
Page 12: ...xiv ...
Page 68: ...2 44 ...
Page 72: ...3 4 Print Test Sample 9 wire Print Test Sample 24 wire ...
Page 85: ...Repair Information 4 11 ...
Page 88: ...4 14 ...
Page 89: ...Repair Information 4 15 This Page Intentionally Blank ...
Page 93: ...Repair Information 4 19 ...
Page 101: ...Repair Information 4 27 This Page Intentionally Blank ...
Page 105: ...Repair Information 4 31 ...
Page 109: ...Repair Information 4 35 This Page Intentionally Blank ...
Page 111: ...Repair Information 4 37 ...
Page 115: ...Repair Information 4 41 ...
Page 119: ...Repair Information 4 45 ...
Page 129: ...Repair Information 4 55 This Page Intentionally Blank ...
Page 137: ...Repair Information 4 63 This Page Intentionally Blank ...
Page 142: ...5 2 Front View ...
Page 143: ...Connector Locations 5 3 Rear View ...
Page 145: ...Connector Locations 5 5 Wiring Diagrams Block Diagram 238X 001 ...
Page 146: ...5 6 Block Diagram 239X 001 ...
Page 147: ...Connector Locations 5 7 Block Diagram 238X 002 ...
Page 148: ...5 8 Block Diagram 239X 002 ...
Page 149: ...Connector Locations 5 9 Block Diagram 238X 003 ...
Page 150: ...5 10 Block Diagram 239X 003 ...
Page 160: ...5 20 Connector Locations Main Logic Board 23XX 001 ...
Page 161: ...Connector Locations 5 21 Main Logic Board 23XX 002 ...
Page 162: ...5 22 Main Logic Board 23XX 003 ...
Page 163: ...Connector Locations 5 23 Sub Logic Boards ...
Page 164: ...5 24 ...
Page 165: ...Connector Locations 5 25 Power Supply ...
Page 166: ...5 26 Operator Panel ...
Page 174: ...7 2 Assembly 1 Major Components ...
Page 176: ...7 4 Assembly 1 Major Components Continued ...
Page 178: ...7 6 Assembly 2 Covers ...
Page 180: ...7 8 Assembly 2 Covers Continued ...
Page 182: ...7 10 Assembly 3 Carrier ...
Page 184: ...7 12 Assembly 3 Carrier Continued ...
Page 186: ...7 14 Assembly 4 Paper Guide Platen Feed Roller ...
Page 188: ...7 16 Assembly 4 Paper Guide Platen Feed Roller Cont ...
Page 190: ...7 18 Assembly 5 Electronics ...
Page 192: ...7 20 Assembly 5 Electronics Continued ...
Page 194: ...7 22 Assembly 5 Electronics Continued ...
Page 196: ...7 24 Assembly 6 ASF Roller Support ...
Page 198: ...7 26 Assembly 7 ASF Side Frame Covers ...
Page 200: ...7 28 Assembly 8 Tractor 2 Option ...
Page 202: ...7 30 ...