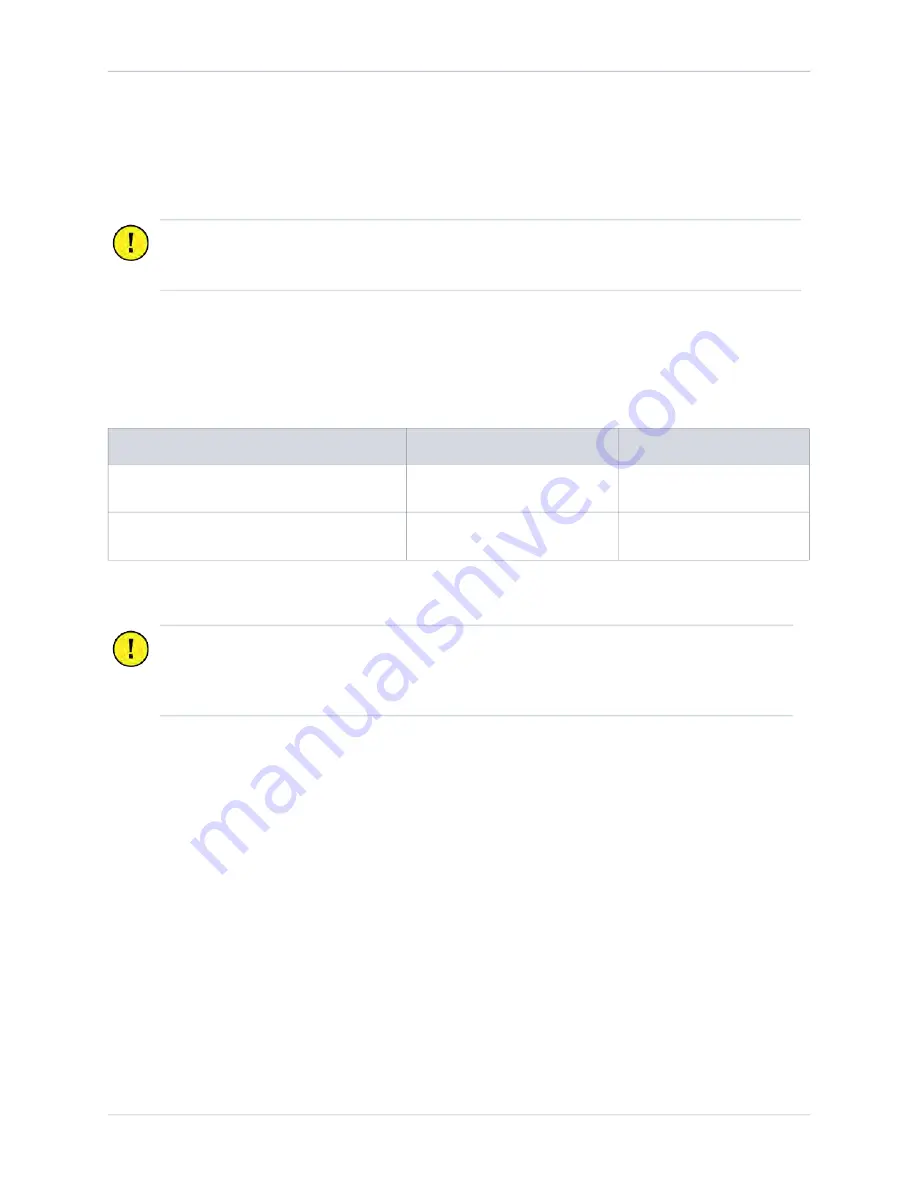
Prepare for Installation
5
•
Paired only:
Outdoor rated Ethernet Cat5e or Cat6 cable, without terminations, is pulled
between the two stations with 3050 mm (10 ft) of service loop at each end.
For any questions about site specifications, refer to the
Express 250 Data Sheet
and
Express 250 Site
Design Guide
.
Check Express 250 Shipping Crates
Each Express 250 ships in at least two crates. Ensure you have all crates at the installation site.
Important:
The Express 250 charging station is tested to IEC 61000-4-5, Level 5
(6 kV @ 3000 A) standards. In geographic areas that experience frequent thunderstorms,
supplemental surge protection must be installed at the service panel.
Contents
Max. Shipped Dimensions
Max. Shipped Weight*
Express 250 Charging Station
1270 x 1104.9 x 2438.4 mm
(50 x 43.5 x 96 in)
494 kg
(1089 lb)
Power Module crate: holds 1 Power Module
901.7 x 571.5 x 368.3 mm
(35.5 x 22.5 x 14.5 in)
49.9 kg
(110 lbs)
*Includes the weight of the crate - for the weight of the component, see the Express 250 Data Sheet
Important:
Always transport and store the Express 250 in its original packaging. Use
appropriate lifting equipment (forklift, crane and lifting straps, etc). Ensure the load rating
of all lifting equipment is adequate for the weight of the crated Express 250 as shown
above.
250_IGcombo.pdf 11
11/18/2019 3:37:40 PM