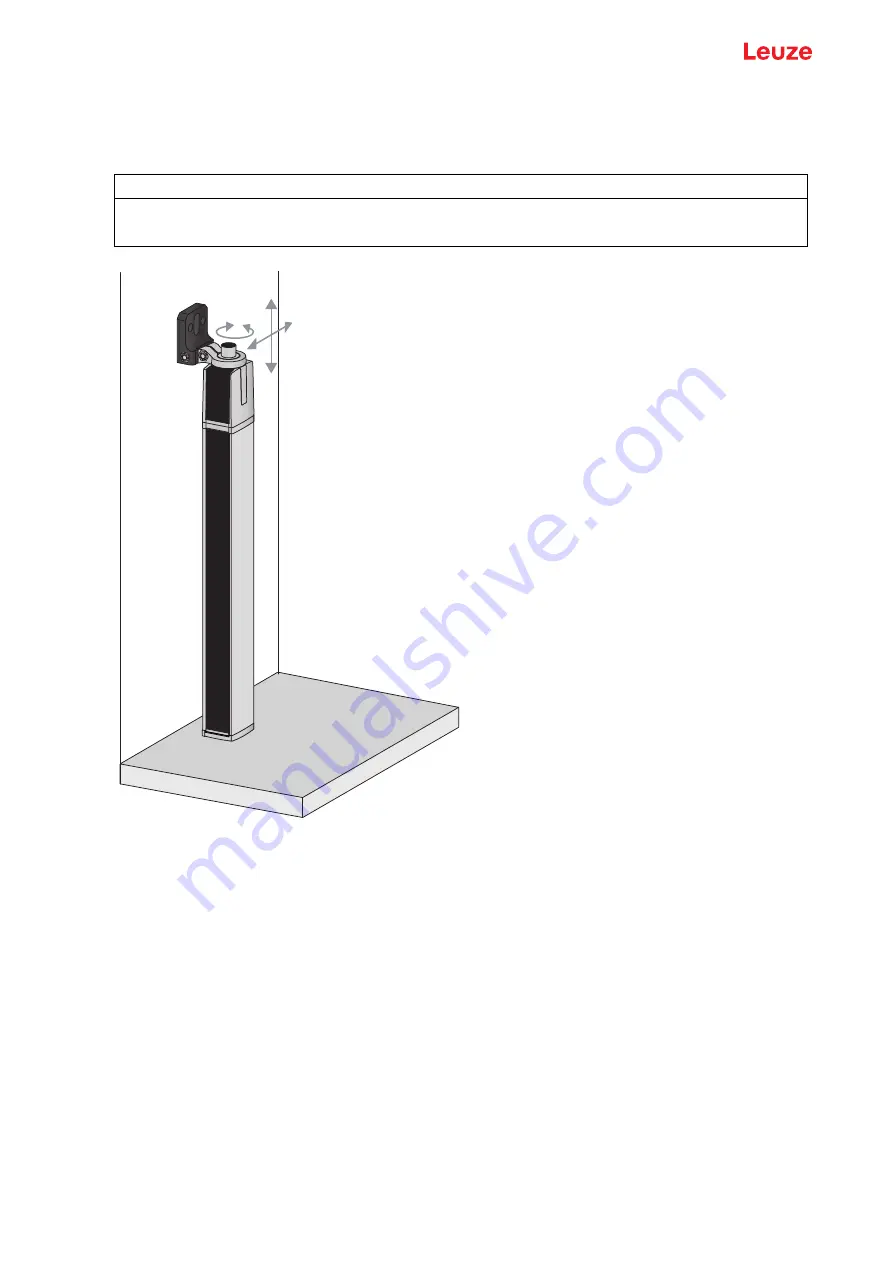
Mounting and installation
Leuze electronic GmbH + Co. KG
CML 730i
49
One-sided mounting on the machine table
The sensor can be mounted directly on the machine table via an M5 screw on the blind hole in the end
cap. On the other end, a BT-2R1 swivel mount can be used, for example, so that turning movements for
alignment are possible despite the fact that the sensor is mounted on one side.
Figure 6.4: Mounting directly on the machine table
6.5
Fastening via swiveling mounting brackets
When mounting with the BT-2SSD/BT-4SSD or BT-2SSD-270 swiveling mounting brackets (see
table 21.26), sold separately, the light curtain can be aligned as follows:
• Sliding in the direction of slot
• T/- 8° around the longitudinal axis
The BT-SSD (see figure 20.7) swiveling mounting brackets are also equipped with a vibration damper.
NOTICE
Avoid reflection bypasses at the machine table!
Make sure that reflections on the machine table and in the vicinity are prevented reliably.