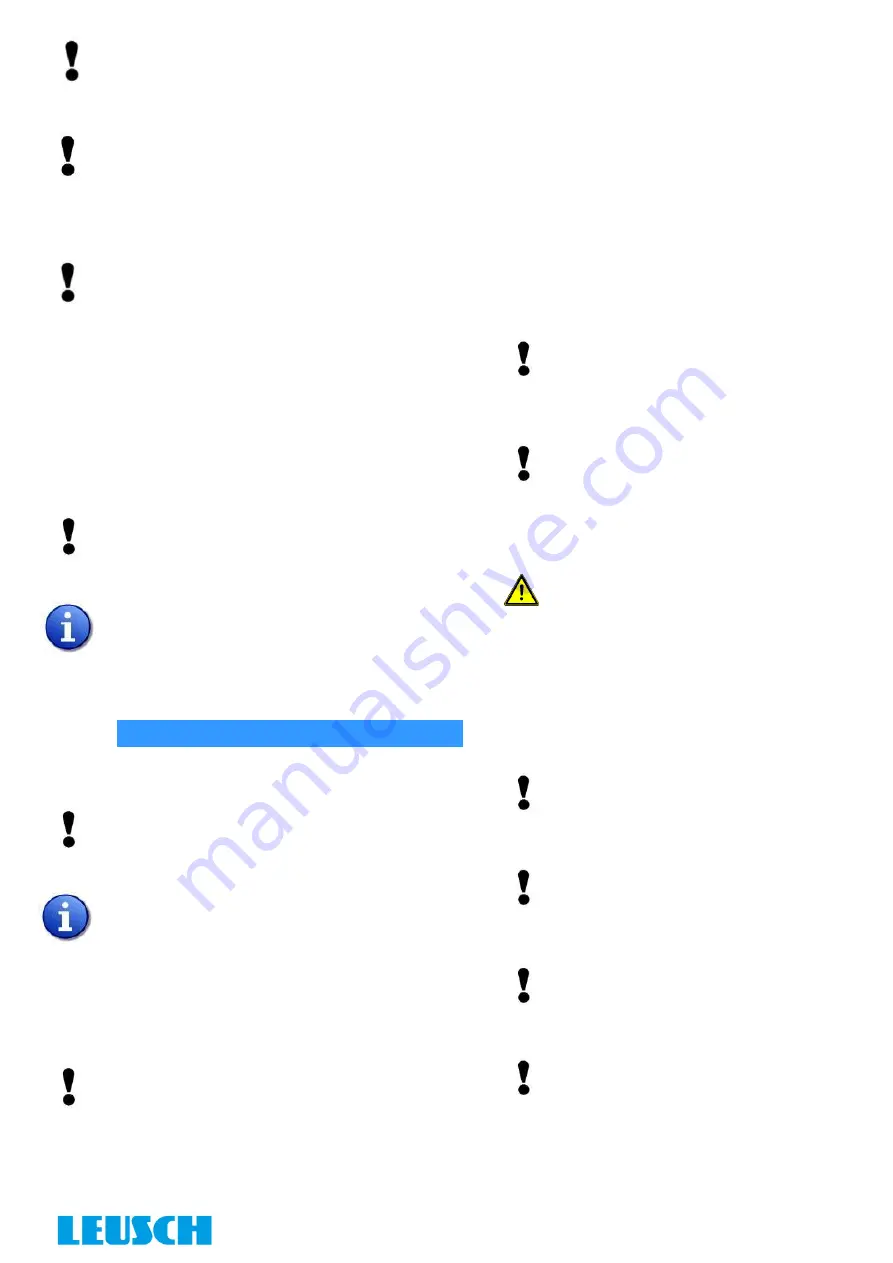
4
4.
The disc should be closed during installation of the
valve.
5.
The following must be ensured for the welding
work to be carried out:
All welded connecting joints are made and
checked in accordance with current and recog-
nised welding procedures.
They are only carried out by specialist personnel
in compliance with the relevant regulations.
Overheating of body and trim is avoided.
The valve is closed to protect sealing elements
from welding beads and dirt.
6.
If there is a risk of static charge on the device,
the operator must ensure that a suitable
ground / earthing connection is installed to pre-
vent this.
7.
Butterfly valves in Series LTR43-2, LTR43-5 and
LTR43-9 have a non-continouis sealing surface.
In Case of Sealing Surfaces acc to EN1092-1
(B1 and B2 only) and ASME (B16.5 RF and
B16.47 RF), please consider flat Gasket type
acc. To EN 1514-1 and ASME B16.21 respec-
tively. For the use of spiral-wound- or kammpro-
file-gaskets, non-standard dimensions have to
be requested from Leusch GmbH.
General installation instructions:
A minimum gap of
5 x pipe diameter
must be kept from
the next component upstream and downstream of the
valve (e.g. pump valve or elbow). If it is not possible to
maintain the prescribed gap due to technical reasons,
we recommend installing the valve in the following posi-
tion. The valve shaft and centre of the elbow cross-
section should be arranged parallel to reduce the dy-
namic forces on the disc
(Fig. 3)
.
For installation on the pressurised side of a centrifugal
pump, the valve shaft must be arranged at a 90° angle
offset to the pump shaft
(Fig. 3)
.
Commissioning, operation, de-commissioning
1.
Commissioning of the device may only be carried
out once the operator has ensured that:
All installation work has been completed on the
pipeline and the device has been correctly in-
stalled in the system.
The pipeline and valve are free of dirt and parti-
cles to ensure faultless functioning (opening/
closing). Residue and operation with fluid that
contain a high proportion of particles could lead
to functional breakdowns and shortened mainte-
nance intervals. If this is to be expected, addi-
tional suitable measures must be planned for the
prevention of faults, if necessary. The system
should therefore be thoroughly cleaned before
commissioning. If necessary, it is recommended
to remove the valve from the pipeline and to re-
place it with adapters
The device has been checked for proper condi-
tion in regard to installation and safe functioning.
2.
In particular, it should be checked and ensured
that:
The valve disc does not collide with the pipeline
during opening/closing.
The parts which come into contact with
fluid are suitable for the planned usage.
Actuators and accessories (if available)
are connected in accordance with man-
ufacturer's instructions and the device
functions correctly corresponding to the
control commands.
The IP and EEx labelling/details are
correct for electrical components.
The limit values on the name-plate, such
as maximum permissible pressure PS of
the valve, minimum/maximum tempera-
ture TS will not be exceeded due to the
operating conditions (P < PS, TS
min. < T
< TS
max.
). In addition, the pressure/
temperature Rating in accordance with
EN 12516, EN 1092 or ASME B16.34
must be observed.
3.
The operator must operate and monitor
the device using trained personnel so
that employees and third parties are not
endangered. If applicable, nationally
relevant regulations of the country of
destination should also be observed for
the operation of the device.
4.
Modifications
to the factory settings for
actuators
(e.g. limit stops) and accesso-
ries (e.g. filter regulator, booster) are not
permitted and may only be carried out in
individual cases with the approval of the
manufacturer by qualified and specialised
personnel.
5.
ATTENTION: The valve disc must be
open when performing a pressure Test of
the pipeline system. It must be ensured
that the maximum permissible pressure
for the valve is not exceeded. Seals
(flange, cover, gland, or extension, if ap-
plicable) must be checked for leakage. If
the Packing Gland leaks, the nuts of the
gland should be alternately tightened in
small steps until the leak is fixed.
Never tighten nuts more than necessary
Maximum torques
Page 8 Tab.1.
If there is still a leak, the manufacturer
should be contacted.
6.
The system is to be started up or
stopped so that no impermissible volt-
age increases result from the tempera-
ture rise/fall. The device must be con-
stantly observed during starting opera-
tion and checked for possible leaks.
7.
In normal operation, the device may only
be operated when all components of the
device are functional and have not been
deactivated or changed in their intended
function.
8.
Operating the valve in constant throttling
position at a small opening angle may
lead to increase wear of the sealing ele-
ments (seat/seatring). This will possibly
lead to shorter maintenance intervals.
9.
When decommissioning the device, all
safety notes in the “Maintenance and ad-
justments” chapter must be observed. The
disposal of the device must be carried out
in accordance with the operational and
national regulations of the destination
country. The relevant operating instruc-
tions of the installed components or acces-
sories must also be followed here.