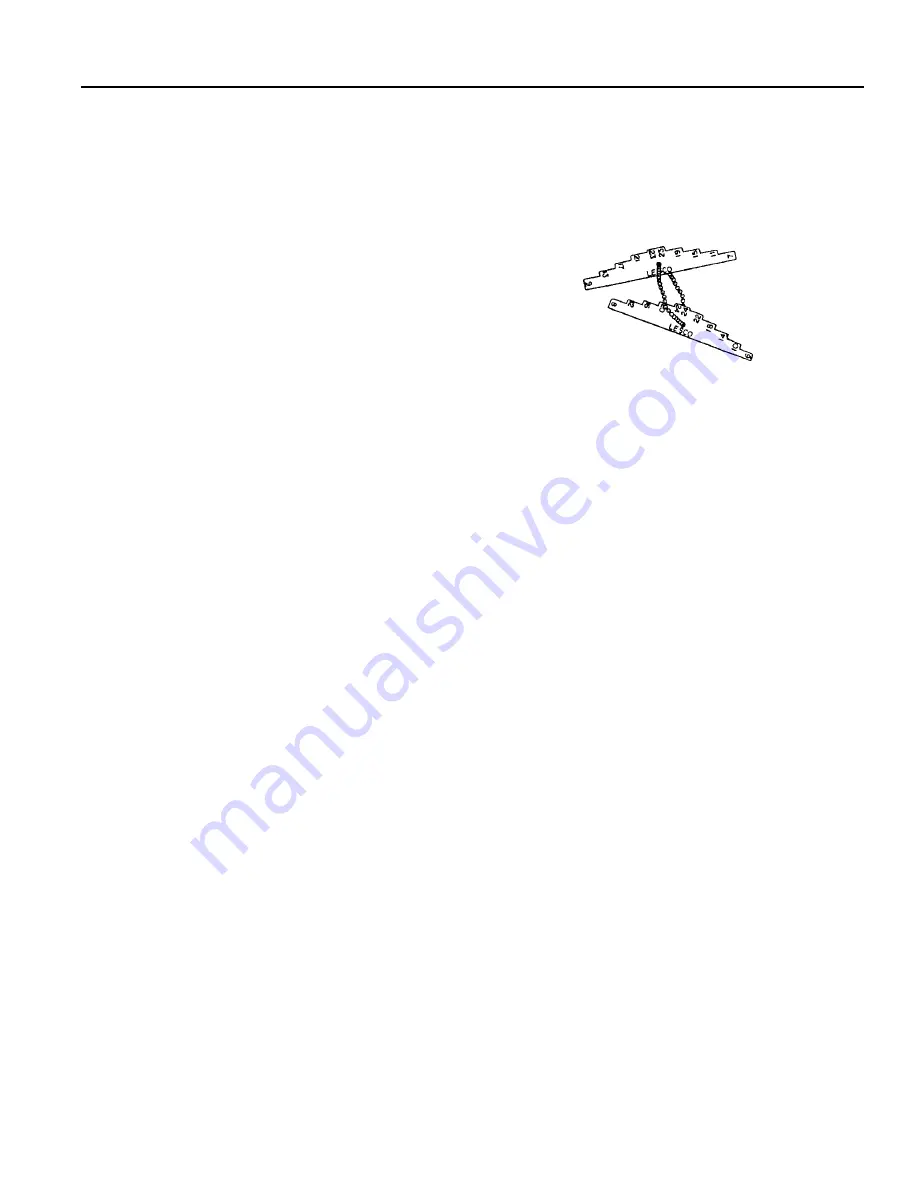
2
Calibration
Spreader calibration is simplified using the LESCO Professional Granular Applicator Calibration Kit LESCO No. 011900
Two Items must be considered when calibrating a spreader. The
first is the distribution pattern of the spreader. That is, the pattern
the product makes as It strikes the ground after being thrown out
by the spreader's impeller. There are many factors which affect
the distribution pattern of a rotary spreader and some of them
relate directly to the product. For this reason, we recommend
that the spreader be calibrated separately for every product to
be applied. Spreader calibration should be checked at least once
a month, or more often when the spreader is used frequently.
The second item Is the product application rate, that is the amount
of product applied per thousand square feet. This is important
because over-application can be costly and may cause plant
injury, while under-application will reduce the effectiveness of
the product.
TO CALIBRATE A SPREADER, FOLLOW THESE STEPS:
A. Check the spreader discharge holes with the operating lever
in the closed position. If the discharge holes are not fully
closed, thread the upper nut on the operating lever rod fur-
ther up the rod. Tighten the lower locknut and recheck. Re-
peat this procedure until the holes are fully closed.
B. TO ACHIEVE A UNIFORM DISTRIBUTION PATTERN:
The accurate method for checking pattern uniformity is to lay
out shallow boxes or pans in a row on a line perpendicular to
the direction of spreader travel. Eleven boxes or pans, two
inches high placed on one-foot centers will provide accurate
calibration. To conduct the test, begin with the remote and
third hole slide plates completely open and set the calibrat-
ing slide at the suggested approximate setting. Make three
passes over the boxes, pushing the spreader in the same
direction each time. The product caught in each box is then
evaluated to determine the distribution pattern. Weighing the
product in each box Is the most accurate, but a simpler method
Is to pour the contents of each box into a separate small vial
or bottle. Then set he eleven vials or bottles side-by-side in
order. This makes the pattern variation quite visible.
To reduce the amount of discharge to the right side (operator's
right) partially close the remote slide plate using the remote
cable lever and repeat the test until the distribution pattern is
uniform.
To reduce the amount of discharge to the left side (operator's
left) loosen the knob and partially close the third hole slide
plate and repeat the test until the distribution pattern is uni-
form.
C. TO ACHIEVE THE CORRECT APPLICATION RATE:
The approximate spreader settings printed on the product
label should only be used as the initial setting for calibration.
Set the calibrating slide at this approximate setting. Using
the collection boxes or pans, make a single pass over them
to determine the effective pattern width. The effective pattern
width is twice (2x) the distance to the point where the rate
drops by one-half the average rate at the center. Example: If
the product In the vials from the center boxes averages two
inches in depth, count out to the vial which has one inch of
product. If this is the fifth vial from the center and the boxes
were on one-foot centers, the effective pattern width is ten
feet (2 x 5 ft.).
Knowing the effective pattern width (ten feet), measure out a
lineal distance to equal 1,000 sq. ft. (10 ft. x 100 ft. = 1,000 sq.
ft.). Weigh 20 Ibs. of product and place it in the spreader hop-
per and spread it over the distance necessary to equal 1,000
sq. ft. (100 ft.). Then weigh the product left in the hopper and
subtract this amount from the amount with which you started.
The result is the application rate for this product in pounds
per 1,000 sq. ft. that your spreader is currently adjusted to
disperse. Adjust the calibrating slide as needed and repeat
this procedure until the correct application rate is achieved.
D. TO USE THE LESCO CALIBRATION GAUGES:
The LESCO Calibration Gauges provide a series of “steps”,
numbered in 1/32-inch increments, that will allow you to “fine-
tune” the LESCO Spreader. Once you have calibrated your
LESCO Mark II spreader for the product chosen, open the
operating lever and insert the calibration gauges until you
determine which step fits tightly into one of the open holes in
the hopper bottom. Record that step number for future refer-
ence when using that product. You may choose to set other
LESCO Mark II spreaders for application of the same prod-
uct by adjusting the main slide plate to that calibration gauge
step. This will provide consistent settings for all of your LE-
SCO spreaders. To recalibrate your LESCO Mark II spreader
after a period of use, adjust the calibrating slide to the “S”
position. Open the operating lever and insert the even-num-
bered LESCO Calibration Gauge into one of the open holes
in the hopper bottom. Close the operating lever and let the
main slide plate on the underside of the hopper make con-
tact with the number ten step on the LESCO Calibration
Gauge. Move the calibrating slide back toward the “A” posi-
tion until the bottom of the slide makes contact with the cali-
brating rod. If your spreader is properly adjusted, the cali-
brating window should be pointing at setting “D” on the top of
the calibrating slide. To correct a variance, adjust the cali-
brating window by loosening the machine screws which hold
it.
E. SPREADER OPERATION:
1. Always push the spreader; do not pull.
2. Push the spreader at a consistent speed (approximately 3
m.p.h. is recommended).
3. Always close the operating lever before filling the hopper.
4. Be sure the screen is in place to prevent lumps or paper
scraps from plugging the holes in the hopper bottom.
5. Always start moving forward before opening the operating
lever; close the operating lever before forward motion is
stopped.
6. Hold the handle at a height that will keep the impeller level.
7. Empty the spreader after each use. Wash the spreader thor-
oughly and allow it to dry. Keep the impeller clean.
8. Lubricate all linkages with LESCO 5-Way Spray Lubricant,
LESCO No. 019428. Grease the gears with LESCO general
purpose Gun Grease, LESCO No. 050539.
Summary of Contents for Commercial Plus 024200
Page 4: ...Gear Set and Controls Figure 1 3 ...
Page 6: ...Frame Figure 2 5 ...