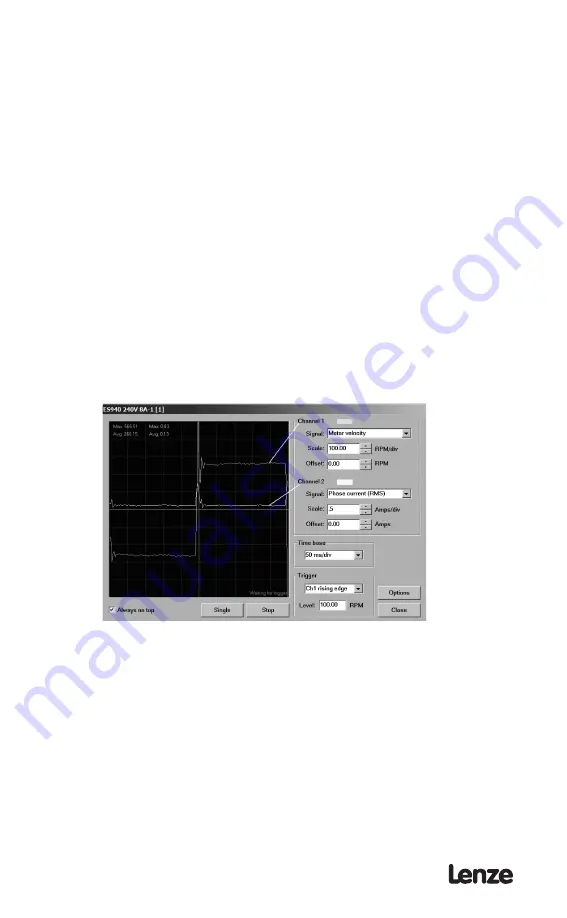
S94P01B
52
7. On the Scope tool select:
• Channel 1:
“Motor Velocity”
• Scale:
100 Rpm/Volt
• Channel 2:
“Phase Current (RMS)”
• Scale:
Motor peak current parameter / 3
• Timebase:
50mS
• Trigger:
Channel 1, Rising
• Trigger level:
100 Rpm
(Choose closest integer value: if 10A/3=3.33(3) choose 3A)
8. Select “Compensation” from the Node tree. Set “Gain Setting” to “-2” if the
motor is equipped with an encoder and to “-4” if the motor is equipped with a
resolver.
9. Set the Velocity P-gain to 5000 and the Velocity I-gain to 20.
10. Apply voltage to IN_A3 input and press F5 on the keyboard. Alternatively you
can use menu “Indexer” -> “Run” or use button on the toolbar.
11. If the motor vibrates uncontrollably, disable the drive, rest P-Gain to 1000,
and re-enable the drive.
12. Slowly increase the “Velocity P-gain” and observe the motor velocity
waveform. Increasing the P-gain should increase the angle of the
acceleration edge of the wave form. Continue increasing the P-gain to get
the leading edge of the wave form as vertical as possible and stop once
you start to get a slight overshoot. The current wave form should be spiking
during the acceleration segment of the move. Continue to increase the P-gain
until instability starts to appear in the waveform.
S949
Stop increasing the gain once you see oscillation appearing on either the
current waveform or velocity waveform flat portion. Then lower the P-gain
until the oscillation disappears
Summary of Contents for PositionServo 940
Page 1: ...Model 940 USERS MANUAL S94P01B S929...
Page 12: ...S94P01B 10 3 2 Clearance for Cooling Air Circulation S924...
Page 66: ...S94P01B 64 Notes...
Page 67: ......